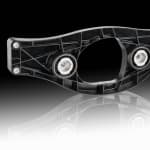
Nośny element konstrukcyjny z tworzywa sztucznego spełnia wszystkie wymagania w zakresie obciążeń statycznych i dynamicznych, którym podlega belka przekładni: jako centralny element tylnej osi przejmuje ona część momentu obrotowego, który jest przenoszony z silnika do przekładni, oraz część obciążenia mechanizmu różnicowego. Dlatego belka z tworzywa Ultramid stosowana jest we wszystkich pojazdach Mercedes-Benz z napędem na cztery koła, z wyjątkiem pojazdów w wersji AMG.
Aby zastąpić aluminium w tym wymagającym elemencie tworzywo sztuczne musi spełniać wysokie wymagania mechaniczne. Ultramid A3WG10 CR (CR = odporne na zderzenia), który jest w 50 proc. wzmocniony włóknem szklanym, wykazuje optymalną wytrzymałość i sztywność, z niewielką tendencją do tzw. pełzania pod wpływem stałego obciążenia. Ponadto, materiał ten wytrzymuje wysokie momenty zginające. Opracowany komponent wykazuje także dobre właściwości NVH (NVH = hałas, wibracje, szorstkość).
- Nowa belka poprzeczna tylnej osi to kamień milowy, jeśli chodzi o wykorzystanie poliamidów w budowie podwozia - mówi Kai Fruehauf, dyrektor działu ContiTech Vibration Control. - Rozwiązanie to ma potencjał, by ustanowić nowy trend w branży motoryzacyjnej. Aby zastąpić metal tworzywem sztucznym o odpowiednich właściwościach, konieczne jest optymalne wykorzystanie materiału i dostosowanie go do konkretnych obciążeń, co właśnie zademonstrował BASF, opracowując Ultramid do produkcji tylnej belki.
BASF wykorzystał swoje narzędzie symulacyjne Ultrasim we wczesnej fazie rozwoju projektu w celu określenia wymiarów komponentu, optymalizacji jego geometrii i próby przewidzenia, jak będzie on się zachowywał przy produkcji w technologii wtryskowej i w eksploatacji. Symulacja skrajnych obciążeń oraz wartości granicznych pod obciążeniem dynamicznym i bezpieczeństwa zderzeniowego bardzo dobrze odzwierciedla rzeczywiste zachowania komponentu. Firma ContiTech Vibration Control zastosowała rozwiązanie Ultrasim Integrative Simulation, aby zbudować model całego łańcucha produkcyjnego. W ten sposób możliwe było określenie geometrii części na wczesnym etapie projektu i zmniejszenie liczby tworzonych prototypów.