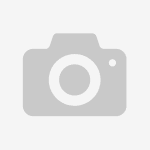
Podczas konferencji omówiono symulację procesu wtryskiwania wybranej wypraski, z użyciem narzędzi numerycznych działających z zastosowaniem Metody Elementów Skończonych (MES). Obiektem badań był element pokrywy komory nabojowej karabinka wojskowego. Zastanowiono się nad możliwością wykorzystania tworzyw polimerowych jako materiału konstrukcyjnego wybranych części składowych broni palnej. Takie zastosowanie tworzyw poprawiłoby ergonomiczność obiektu badań. W założeniach konstrukcyjnych tego typu elementy cechować powinny się takimi właściwościami użytkowymi jak: tolerancje wymiarowe i kształtowe, odporność termiczną, a także duża trwałość.
Dzięki zastosowaniu narzędzi numerycznych, wykorzystujących Metodę Elementów Skończonych możliwa jest symulacja danego procesu wytwarzania w celu prognozowania wybranych parametrów technologicznych. Zaprezentowano wyniki analizy MES procesu wtryskiwania produktu z uwzględnieniem jego przetwórczych tendencji skurczowych.
Do analizy MES procesu wtryskiwania wypraski użyto modelu lewej wkładki, która została wygenerowana w systemie 3D MCAD UGS Solid Edge V17. Geometrię wyeksportowano za pośrednictwem formatu *.stl do aplikacji CAE MPA Moldflow 7.0. W pierwszym kroku badań dokonano porównania wpływu zastosowania liczności punktów wtrysku na: deformacje, rozkłady spadków ciśnienia, temperatury czoła strugi, czasu wypełnienia, skurczu lokalnego, orientacji powierzchni i linii łączenia strug.
Przeprowadzona symulacja numeryczna procesu wtryskiwania wykazała, że odkształcenia skurczowe dla jednego punktu wtrysku są większe i bardziej skupione niż w przypadku zastosowania dwóch punktów wtrysku.
Dlaczego tak się dzieje?
Wywołane jest to większymi drogami płynięcia tworzywa, w przypadku jednego punktu, co powoduje większe spadki ciśnienia, temperatur. Prowadzi to jednocześnie do zróżnicowania skurczu lokalnego i w konsekwencji zwiększenia deformacji całej wypraski. Dla dwóch punktów wtrysku czas cyklu wytwarzania jest krótszy o około 27 proc., co przyśpiesza produkcję.
Zastosowanie dwóch punktów wtrysku jest korzystniejsze ze względu na odkształcenia i czas cyklu, jednak powstające linie łączenia strug dyskwalifikują to rozwiązanie. Ze względu na równomierną wytrzymałość wypraski linie łączenia strug w newralgicznych obszarach są niedozwolone.
Jeśli chodzi o dobór materiału konstrukcyjnego, to dominujący wpływ na właściwości wypraski ma zastosowanie odpowiedniego tworzywa, które należy dobierać pod kątem postawionych założeń. W przeprowadzanych badaniach, które omawiano w trakcie konferencji, użyte zostały tworzywa polimerowe zróżnicowane ze względu na budowę struktury wewnętrznej: krystaliczne i amorficzne.
Tworzywa krystaliczne mają uporządkowany rozkład łańcuchów węglowych, większy skurcz o charakterze anizotropowym, zależnym od kierunku płynięcia.
Rozkład łańcuchów w tworzywach amorficznych jest losowy, posiadają one mniejszy skurcz o charakterze izotropowym. Tworzywami krystalicznymi użytymi do badań był polipropylen, poliamid oraz poliamid napełniony włóknem szklanym. Amorficznymi zaś polistyren.