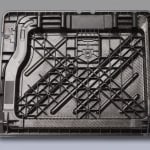
Koncepcje nowych kompozytów dla przemysłu samochodowego
Pierwszy prototyp produkcyjny prezentujący pakiet Ultracom: Tylna kanapa wyprodukowana przez Johnson Controls
Po lipcowej premierze nowego produktu BASF Ultracom, firma już teraz zaprezentuje pierwszy element kompozytowy demonstrujący wyjątkowy pakiet serwisowy na Targach Composites Europe 2013. Jest to oparcie tylnych foteli opracowane przez firmę Johnson Controls Automotive Seating we współpracy z BASF. Produkt ten został stworzony na bazie tworzywa Ultralaminate, wzmocnionego włóknem materiału termoplastycznego obtryskiwanego przy użyciu tworzywa Ultramid ZG7 COM, wysoko odpornego na wstrząsy zmodyfikowanego poliamidu 6. W czasie opracowania produktu, w ramach pakietu Ultracom, firma BASF zapewniła rozszerzone wsparcie symulacyjne. Złożony element kompozytowy jest o ponad 30 proc. lżejszy od swojego metalowego odpowiednika.
Element CIFO: Materiał, technologia, opracowanie komponentu
Ponadto podczas Targów Composites Europe 2013 zaprezentowany zostanie nowy produkt CIFO (nazwa oznacza kombinację technologii formowania wtryskowego i obtrysku). Produkt został opracowany przez BASF aby w pełni wykorzystać wszystkie możliwości projektowania elementów kompozytowych przy użyciu nowej komórki produkcyjnej Ultracom. Wielofunkcyjny element testowy stworzony w celu zbadania kompozytowego komponentu wzmocnionego włóknem pod względem produkcji masowej składa się z formowanego laminatu o grubości 1,5 mm oraz wytworzonych metodą obtrysku elementów funkcjonalnych o grubości 3 mm (żebra i krawędzie). Dzięki elementowi posiadającemu ok. 20 różnych funkcjonalności, możliwe jest zaprezentowanie charakterystyki produkcji części kompozytowych. Szczególne cechy komponentu to m.in. uszczelnienie krawędzi, długie ścieżki przepływu, uformowane otwory, uszeregowanie żeber, wielokrotnie formowane elementy oraz żebrowany ceownik.
Prototyp epoksydowego błotnika produkowanego metodą RTMZespół specjalistów Lightweight Composite Team opracowuje również w firmie BASF koncepcje kompozytów wzmocnionych włóknem bazujące na systemach poliuretanowych i żywic epoksydowych do zastosowań konstrukcyjnych i pół-konstrukcyjnych. Na przykładzie błotnika wzmocnionego włóknem węglowym, firma zaprezentuje nowy system żywic epoksydowych Baxxodur System 2202 opracowany specjalnie do wysokociśnieniowej produkcji metodą RTM. System żywic epoksydowych utwardza się w temperaturze 120 stopni Celsjusza, a czas wyjęcia z formy wynosi 2,5 minuty, cechuje się dobrymi właściwościami mechanicznymi oraz szerokim oknem formowania.