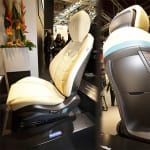
Po przedstawieniu prototypu na pokazie Los Angeles Motor Show pod koniec 2009 r. nastąpiło dalsze udoskonalenie fotela o nazwie SUSCO 1.5 (skrót od Sustainable Comfort). Poddostawcy przemysłu samochodowego liczą na to, że pierwsze produkowane seryjnie fotele pojawią się na drogach za cztery lata.
Specjalnie na potrzeby tego projektu firma BASF opracowała nowe tworzywo Ultramid-Type (PA). W nowej technologii dotychczasowa konstrukcja metalowa została zastąpiona jednoczęściowym elementem z tworzywa sztucznego, co pozwala jednocześnie zredukować ilość pianki i okładziny.
Fotel ten jest o około 20 proc. lżejszy i o 30 mm cieńszy od zwykłego fotela, co jest odpowiedzią na potrzebę wdrażania lekkich konstrukcji. Fotel z tworzywa sztucznego wykorzystuje możliwości oferowane przez ten surowiec i łączy wygodę z nowoczesnym, cienkościennym i wysokojakościowym wzornictwem.
Szczególną cechą oparcia tego fotela jest zastosowanie taśmy z włókien ciągłych, na którą w kolejnym etapie natryskuje się Ultramid. Zastosowany nowy rodzaj poliamidu firmy BASF, dzięki specjalnie wyregulowanemu zachowaniu mechanicznemu, posiada właściwości dokładnie dostosowane do łączenia ze strukturami włókien ciągłych.
Przedmiotowy projekt łączy znajomość materiałów i technologii z know-how w zakresie konstrukcji i produkcji fotela samochodowego.
Tak jak w przypadku innych ważnych części samochodowych wykonywanych z tworzyw sztucznych, także w przypadku wzmacniania włókien ciągłych, pierwszym krokiem przy opracowaniu produktu są symulacje zachowania przy zderzeniu.
BASF wsparła w tym zakresie firmę Faurecia narzędziem symulacji Ultrasim, które w tym celu rozbudowano o dane dotyczące półproduktów z włókien ciągłych, aby można było z dużą niezawodnością przewidzieć zachowanie podczas zderzenia elementów z dużą zawartością włókien o wysokiej anizotropii.