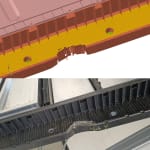
Inżynieryjne tworzywa sztuczne, takie jak poliamid 6, oferują liczne korzyści przy projektowaniu obudów akumulatorów dla pojazdów elektrycznych - na przykład w zakresie zrównoważonego rozwoju, kosztów produkcji, zmniejszenia masy oraz ekonomicznej integracji funkcjonalnej. Jednak wcześniej istniały wątpliwości, czy te duże i złożone komponenty są również w stanie spełnić bardzo wysokie wymagania w odniesieniu do wytrzymałości mechanicznej i właściwości trudnopalnych. Kautex Textron i Lanxess przeprowadziły właśnie kompleksowe badania w tym zakresie, wykorzystując wspólnie opracowany demonstrator technologii z poliamidu 6. Lanxess był odpowiedzialny za rozwój materiału, a Kautex Textron za inżynierię, projekt i proces produkcji demonstratora.
- Demonstrator z serii near-series przechodzi wszystkie testy mechaniczne i termiczne, które są istotne dla tego typu obudów. Ponadto opracowano rozwiązania dotyczące np. zachowania w zmiennych warunkach termicznych i szczelności obudowy. To wszystko potwierdziło techniczną wykonalność elementów, które wymagają wysokiego stopnia bezpieczeństwa, są złożone i podlegają wysokim obciążeniom - wyjaśnia dr Christopher Hoefs, kierownik projektu e-Powertrain w firmie Lanxess. Aby sprawdzić jego przydatność do codziennego użytku, prototyp obudowy aktualnie jest testowany w pojeździe testowym w trasie. - Obecnie wspólnie z producentami samochodów zajmujemy się pierwszymi projektami rozwoju, aby wdrożyć nową technologię do produkcji seryjnej - dodaje Felix Haas, dyrektor ds. rozwoju produktu w Kautex Textron.
Mniejszy ślad węglowy
- Obliczenia wykazały, że ślad węglowy obudowy z tworzywa sztucznego jest o ponad 40 procent mniejszy w porównaniu z konstrukcją aluminiową. Niższe zużycie energii przy produkcji poliamidu 6 w porównaniu z metalem, jak również inne czynniki - takie jak pominięcie czasochłonnego katodowego malowania zanurzeniowego w celu zapobiegania korozji w przypadku zastosowania stali - pomagają zminimalizować ślad węglowy - mówi Hoefs. Konstrukcja elementów z tworzyw termoplastycznych ułatwia również recykling obudowy w porównaniu z materiałami termoutwardzalnymi, takimi jak na przykład SMC.
Wysoka trwałość, odporność na zewnętrzne źródła ognia
Testy demonstratora technologii zostały przeprowadzone zgodnie z uznanymi międzynarodowymi standardami dla pojazdów elektrycznych zasilanych z akumulatorów, takimi jak ECE R100 Europejskiej Komisji Gospodarczej lub chińskim standardem GB 38031. Wielkoformatowa obudowa wykonana w całości z tworzywa sztucznego, która mierzy około 1400 milimetrów długości i szerokości, wykazała swoją wydajność we wszystkich istotnych testach. Na przykład, spełnia wymagania testu wstrząsów mechanicznych, który służy do badania zachowania się komponentu w przypadku silnych wstrząsów, oraz testu zgniatania, który konstruktorzy wykorzystują do badania odporności obudowy akumulatora w przypadku powolnych odkształceń. Wyniki testów upadku i wibracji również były pozytywne, podobnie jak wyniki testu uderzenia od spodu. Test ten bada stabilność akumulatorów, które w większości są umieszczone w podłodze pojazdu, w przypadku kontaktu konstrukcji pojazdu z podłożem lub uderzeń sporych kamieni. - Wszystkie wyniki testów potwierdzają wcześniejsze symulacje i obliczenia. Krytyczne uszkodzenie obudowy z tworzywa sztucznego nie wystąpiłoby w żadnym z przypadków obciążenia - wyjaśnia Haas. Demonstrator udowodnił również swoją odporność na zewnętrzne źródła ognia pod pojazdem zgodnie z normą ECE R100 (pożar zewnętrzny).
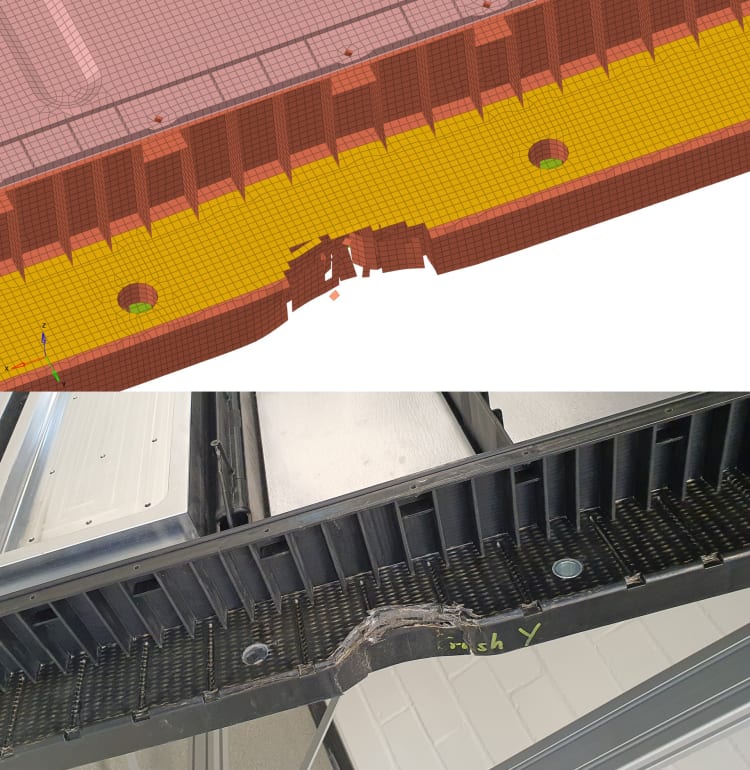
Test zgniatania w kierunku: Wyniki symulacji bardzo dobrze pokrywają się z wynikami testu fizycznego elementu. fot: Kautex
Niższa waga, niższe koszty produkcji
Demonstrator został opracowany na podstawie aluminiowej obudowy akumulatora średniej wielkości pojazdu elektrycznego i przeznaczony do produkcji masowej. Jest on wytwarzany w jednoetapowym procesie formowania ciśnieniowego przy użyciu masy formierskiej na bazie związku poliamidu 6 Durethan B24CMH2.0 firmy Lanxess i nie wymaga żadnych dalszych przeróbek. Obszary narażone na zderzenia są specjalnie wzmocnione za pomocą lokalnie umieszczonych półfabrykatów wykonanych z kompozytu Tepex dynalite 102-RGUD600 wzmocnionego włóknem ciągłym na bazie poliamidu 6. W porównaniu z konstrukcją aluminiową uzyskano zmniejszenie masy o około 10 procent, co jest korzystne dla zasięgu, a tym samym dla śladu węglowego pojazdu. Integracja funkcji - takich jak elementy złączne, żebra wzmacniające i komponenty do zarządzania termicznego - znacznie zmniejsza liczbę pojedynczych elementów w porównaniu z konstrukcją metalową, co upraszcza montaż i wysiłek logistyczny oraz obniża koszty produkcji.