Ściśle współpracując z zajmującą się formowaniem firmą Fielding Mfg., XTech na początku zastosowała to przewodzące tworzywo sztuczne do produkcji płyt czołowych obudów – po części dlatego, że każda z nich ma tak wiele wariantów. Jak wyjaśnia Richardson, rodzina płyt czołowych może obejmować pięć do dziesięciu (lub więcej) różnych form, w których można zamontować różnorodne zestawy płytek drukowanych. – Jednym z wyzwań było stworzenie pojedynczej formy z różnymi wkładkami, które umożliwiłyby dostosowanie układu otworów do wymagań klienta – mówi Richardson.
Jak do tej pory, wyniki projektu obudów z tworzyw sztucznych są obiecujące. Richardson twierdzi, że – wbrew powszechnemu przekonaniu – tworzywa sztuczne spisały się dobrze przy wyższych częstotliwościach podczas testów odporności na zakłócenia elektromagnetyczne, które zazwyczaj przeprowadza się do częstotliwości 20 GHz. – W przypadku tworzyw sztucznych działanie ochronne faktycznie poprawiało się wraz ze wzrostem częstotliwości – mówi Richardson. Uważa on, że formowane tworzywa sztuczne przyniosą także inne korzyści, między innymi poprawioną odporność na korozję w przypadku instalacji na zewnątrz budynków oraz możliwość dodania na etapie formowania elementów takich, jak np. zatrzaski.
Nie spodziewajcie się jednak, że w niedalekiej przyszłości tworzywa sztuczne całkowicie zastąpią metale. – Metal posiada samoistne właściwości ekranujące oraz zmniejszające palność w cieńszych odcinkach ścianek – zaznacza Richardson. Zwłaszcza metale wytłaczane i blachy cienkie trudno pobić z punktu widzenia kosztów – o ile nie występują specjalne wymagania konstrukcyjne lub duże ilości, które działają na korzyść tworzyw sztucznych. – Wybiegając w przyszłość zauważycie, że jest miejsce i dla metali, i dla tworzyw sztucznych – kończy Richardson.
Joseph Ogando
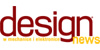
Źródło: Design News 2(21) luty 2007, s. 10