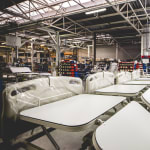
Wdrożenie rozwiązań gospodarki obiegu zamkniętego pozwoliło największemu wytwórcy sprzętu medycznego w Polsce znacząco ograniczyć ilość odpadów wytwarzanych w procesie produkcji. Jednocześnie aż 99,95 proc. z nich jest wykorzystywane w recyklingu.
Stoły operacyjne i łóżka szpitalne Famedu wspomagają leczenie w niemal każdym polskim szpitalu. Po zakończeniu cyklu życia zużyte urządzenia również są poddawane recyklingowi.
Famed walczy z odpadami
Famed wytwarza rocznie ponad 3 tysiące egzemplarzy swoich wyrobów - łóżek szpitalnych, stołów operacyjnych czy wózków do transportu pacjentów. Do ich produkcji zużywanych jest m.in. 288 ton stali różnego gatunku, 135 km rur i profili stalowych, a także tworzywa sztuczne. Firma, będąc pionierem tego typu działań na Żywiecczyźnie, konsekwentnie doskonali procesy technologiczne inwestując w nowoczesny - precyzyjny, energooszczędny i niskoemisyjny - park maszynowy oraz doskonaląc procedury. Kilkanaście zrealizowanych w zakresie czystszej produkcji projektów i dobre praktyki Gospodarki Obiegu Zamkniętego pozwoliły uzyskać rekordowe efekty.
W 2017 roku w efekcie działalności produkcyjnej spółki powstały 183 tony odpadów, z których niemal 99 proc. zostało ponownie wykorzystanych. Ubiegłoroczny wynik jest jeszcze lepszy.
W 2018 roku spółka o prawie 12 proc. zmniejszyła - mimo zwiększonej wielkości produkcji - ilość wytworzonych odpadów poprodukcyjnych. Żywiecki zakład wytworzył 160,869 ton takich odpadów, z których aż 99,95 proc. przekazano do ponownego zagospodarowania w formie odzysku lub recyklingu przez firmy zewnętrzne. Jedynie 84 kilogramy, czyli 0,05 proc., trafiły do składowania.
- Skuteczna walka z odpadami pozwala nam ograniczać negatywny wpływ na środowisko i przynosi wymierne korzyści finansowe. Naszą firmę tworzy zespół około 300 pracowników. Wykorzystujemy rocznie kilkaset ton różnych materiałów. To, że efektem działalności tak dużej organizacji są jedynie 84 kg odpadów poprodukcyjnych, które trafiają do składowania, uznajemy za nasz sukces - mówi Małgorzata Kotajny-Szewczyk, Dyrektor ds. Logistyki Famedu Żywiec.
Nie bez znaczenia dla środowiska pozostaje również okres użytkowania sprzętu medycznego, bowiem odpowiedzialność firmy nie kończy się w momencie dostarczenia sprzętu odbiorcy.
Famed spełnia określone prawem wymagania dotyczące zbierania oraz przetwarzania zużytego sprzętu elektrycznego i elektronicznego, do którego zalicza się wyroby medyczne. Produkty spółki wykonane są z materiałów bezpiecznych, posiadających odpowiednie certyfikaty i atesty, a w konsekwencji nadających się, po zakończeniu cyklu życia, do procesów odzysku lub recyklingu. Co więcej, o ile np. telefony komórkowe (podobnie jak wyroby medyczne będące sprzętem elektronicznym) wymieniane są średnio co 3 lata, to w przypadku łóżek czy stołów Famed oferuje 70-miesięczną gwarancję na swoje produkty, a okres ich użytkowania wynosi od kilkunastu do nawet kilkudziesięciu lat. Wyeksploatowane łóżka szpitalne czy stoły operacyjne przekazywane są bezpośrednio przez placówkę medyczną bądź za pośrednictwem Famedu, do zakładów przetwarzania prowadzących demontaż sprzętu i jego dalsze zagospodarowanie.
Pracownicy zaangażowani w inicjowanie zmian
W projekty środowiskowe zaangażowani są pracownicy spółki. W Famedzie prowadzone są szkolenia i instruktaże wdrażane z myślą o podnoszeniu świadomości ekologicznej oraz zwiększaniu zaangażowania załogi w działania na rzecz poprawy stanu środowiska naturalnego.
- Naszymi działaniami chcemy dać dobry przykład, nie tylko jako przedsiębiorstwo. Naszym celem jest również uświadamianie pracowników, że każdy może swoimi codziennymi praktykami przyczyniać się do polepszania stanu środowiska. Szczególnie w świetle problemów ze złym stanem powietrza, z którym boryka się Żywiec. Propozycje zmian w procesach technologicznych
czy rozwiązaniach konstrukcyjnych, które przedstawiają nasi pracownicy, przekładają się nie tylko na korzyści ekonomiczne, ale również na ekologiczne i społeczne, np. poprawę warunków pracy - wyjaśnia Małgorzata Kotajny-Szewczyk.
Żywieckiego producenta do podjęcia działań w obszarze zmian w technologii produkcji skłoniły rosnące wymagania klientów i presja ze strony konkurentów. Konkretna inicjatywa pojawiła się w czasie wdrażania Systemu Zarządzania Środowiskiem ISO 14001 oraz podpisania w 1999 roku Międzynarodowej Deklaracji Czystszej Produkcji UNEP oraz Deklaracji Poparcia dla Inicjatywy Sekretarza Generalnego ONZ- United Nations Global Compact we wrześniu 2004r.
Polska marka medyczna w ostatnich latach dynamicznie się rozwija. Wyroby żywieckiej spółki wspomagają leczenie w szpitalach w 97 krajach. Na przestrzeni minionych lat łączne wpływy Famedu z rynku krajowego to ponad 100 mln złotych, a przychody z eksportu od 2014 roku osiągnęły wartość ponad 110 mln. Najważniejszą ubiegłoroczna premierą jest Famed Flare, stół operacyjny do chirurgii małoinwazyjnej, który pobił światowy rekord przezierności dla promieni rentgenowskich. Obniżenie tego parametru (do poziomu 0,36mmAI) i tym samym dawki promieniowania niezbędnego do wykonania dobrej jakości zdjęcia RTG, pozwoliło podnieść bezpieczeństwo lekarzy i pacjentów.
Famed produkuje czyściej
Optymalizacji poddany został m.in. proces mycia na Wydziale Produkcji Podzespołów Metalowych. Taka obróbka chemiczna jest jednym z procesów stosowanych do przygotowania (np. odtłuszczania) stali przed lakierowaniem czy nakładaniem powłoki galwanicznej. Żywotność kąpieli myjącej wydłużono z okresu
6 miesięcy na pracę ciągłą, która trwa nieprzerwanie od 2006 roku. Przed wdrożeniem zmian do sporządzenia nowej kąpieli oraz jej eksploatacji zużywano rocznie 6,6 m3 wody i 510 kg chemii, a w efekcie powstawało 6,6 m3 wymagających utylizacji odpadów niebezpiecznych (zużyta kąpiel).
Po modernizacji chemia używana jest jedynie do korekty stężeń, w ilości 110 kg/rok (mniej o 79 proc.), a ilość wytwarzanych odpadów niebezpiecznych wymagających utylizacji to jedynie 0,1 m3 (mniej o 98 proc.). Efekt ekonomiczny wprowadzenia opisanej zmiany to około 4500 zł oszczędności w skali roku, której osiągnięcie nie wymagało żadnych nakładów inwestycyjnych. Famed od lat 90-tych XX w. zrealizował także kilkanaście innych projektów Czystszej Produkcji.
Skuteczna segregacja odpadów
Wprowadzona w latach 90-tych segregacja odpadów poprodukcyjnych i komunalnych przyczyniła się do znacznego ograniczenia ilości tych odpadów, które wymagają składowania oraz kilkukrotnego zwiększenia ilości odpadów przeznaczonych do recyklingu i odzysku. Już w pierwszym roku jej stosowania ilość odpadów przeznaczonych do składowania ograniczono o ok. 60 proc.
Recykling materiałów opakowaniowych
Materiały wykorzystywane do pakowania wyrobów spółki to papier, tektura, folie oraz drewno. Wszystkie używane materiały spełniają wymagania Ustawy o gospodarce opakowaniami i odpadami opakowaniowymi oraz Rozporządzenia Min. Środowiska w sprawie zawartości ołowiu, kadmu, rtęci i chromu sześciowartościowego w opakowaniach. Dzięki wdrożonym zmianom ograniczono ilości opakowań z tworzyw sztucznych nie nadających się do recyklingu materiałowego, a tylko do odzysku ciepła. Większość wyrobów na rynek krajowy jest przekazywana odbiorcom na paletach drewnianych, z użyciem niezbędnych zabezpieczeń foliowych poszczególnych elementów. Natomiast produkty za granicę są pakowane na paletach lub w drewnianych klatkach oraz w karton. Zużyte opakowania są selektywnie zbierane wg. rodzajów odpadów i przekazywane firmom zewnętrznym do recyklingu materiałowego (makulatura i tworzywa) lub do odzysku ciepła (opakowania z drewna).
Działania żywieckiej firmy wpisują się w sugestie ekspertów, którzy wskazują, że dla polepszenia skuteczności zagospodarowywania odpadów konieczne jest zwiększenie odpowiedzialności producentów za wprowadzane na rynek opakowania.
Minimalizacja odpadów w procesie termoformowania tworzyw
Proces przetwórstwa tworzyw prowadzony w Famedto przykład procesu o minimalnej ilości powstających odpadów/folia zabezpieczająca płyty ABS, w którym surowiec znajduje się w obiegu zamkniętym.