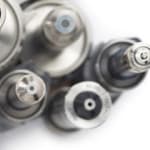
Zakresy przetwórstwa i zachowania się tworzywa odzwierciedlane przebiegiem krzepnięcia tworzyw amorficznych znacznie odbiegają od takich samych parametrów dla tworzyw semikrystalicznych. Należy zwrócić na to szczególną uwagę. W każdym przypadku konieczny jest staranny dobór systemu z gorącymi kanałami doprowadzającymi, w szczególności jeżeli przetwarzane będą niepalne gatunki tworzyw.
Dlatego warto przedstawić główne wskazówki dotyczące doboru systemu z gorącymi kanałami doprowadzającymi oraz wymagania konstrukcyjne przy przetwarzaniu tworzyw.
Ze względu na wąski przedział technologiczny wyznaczany temperaturą topnienia konieczne jest zastosowanie bardzo dobrze zaprojektowanej izolacji termicznej pomiędzy gorącym kanałem doprowadzającym a formą. Celem tego jest uniknięcie dużych różnic temperatury w obrębie systemu. Uwaga musi być zwrócona także na rozdzielacz. Prawidłowe traktowanie stopionego tworzywa wymaga zapewnienia równomiernego rozkładu temperatur. W konstrukcji rozdzielacza uwzględnione musi być kilka kluczowych zasad.
Pierwsza z nich to niski spadek ciśnienia. Zaleca się stosowanie tylko takich rozdzielaczy, których średnica w pełni odpowiada prawidłowemu przepływowi strumienia stopionego tworzywa. Nie jest wskazane stosowanie systemów z ogrzewaniem wewnętrznym i przepływem pierścieniowym. Ponadto doradzane jest stosowanie ścieżek przepływu bez ślepych kanałów oraz stosowanie zrównoważonych układów dysz. Gwarantuje to równomierny spadek ciśnienia i identyczne czasy dopływu w każdym punkcie wtrysku.
Jeśli chodzi z kolei o dysze, które też są niezbędnym elementem całego układu, to podstawą uzyskania dobrych wyników jest zapewnienie małego spadku ciśnienia i dobrego rozkładu temperatur. Odbywa się to dzięki zastosowaniu termopary w obrębie otworu wtryskowego. Stosowane być powinny, o ile jest to możliwe, otwarte dysze z ogrzewaniem zewnętrznym i kanałem zapewniającym swobodny przepływ stopionego tworzywa. Rozwiązanie takie można stosować tam, gdzie wykorzystywane są zimne pomocnicze kanały doprowadzające. Ten sposób jest szczególnie zalecany dla materiałów wzmocnionych włóknem szklanym lub materiałem mineralnym. Otwór znajdujący się na przeciw otworu wtryskowego wychwytuje wszelkie zimne wtrącenia stałe wydobywające się z otworu wtryskowego.
Rozwiązaniami mniej korzystnymi są natomiast dysze dzielące strumień na dwa lub kilka małych strumieni, dysze z przestrzeniami umożliwiającymi zaleganie tworzywa w strefie przedniej oraz systemy ogrzewane wewnętrznie z przepływem pierścieniowym. Jeżeli konieczne jest zastosowanie takich konstrukcji do wtrysku bezpośredniego w celu uzyskania bardzo małego punktu wtryskiwania, to bardzo istotne jest zastosowanie tulejki w charakterze izolacji termicznej.
Użycie dysz igłowych zawsze stanowi kompromis. Jeżeli będą one zastosowane w celu uzyskania bardzo wysokiej jakości powierzchni w strefie otworu wtryskowego, to pamiętać należy o tym, że są one nie tylko bardzo drogie, ale powodują także duży spadek ciśnienia. Jest to wywołane przez pierścieniowy przepływ cieczy. Nie jest możliwe w nich dobre zaprojektowanie dróg przepływu. W przypadku przetwórstwa tworzyw wzmocnionych pojawić się mogą problemy w systemie zamykającym. Zastosować należy kombinację dysza /igła o dużym przekroju. Zaleca się stosowanie zespołów sterowanych hydraulicznie i unikanie systemów sprężynowych.
Gdy mowa jest z kolei o regulacji temperatury, to powinno się sięgać po odrębne systemy regulacji temperatury rozdzielacza i poszczególnych dysz. Powinny to być systemy ze sprzężeniem zwrotnym. Najlepsze wyniki uzyskuje się stosując automatyczne regulatory temperatury typu PID, gdyż zapewniają one najmniejsze wahania temperatury wokół zadanego punktu pracy.
Korzystnym rozwiązaniem jest również zastosowanie odrębnych kanałów chłodzących w obszarze dyszy z gorącym kanałem doprowadzającym. W takim układzie łatwo można uzyskać odpowiednie warunki temperaturowe w obszarze gorącego kanału doprowadzającego bez równoczesnego oddziaływania na temperaturę całej formy.
Wykorzystano materiały firmy DuPont.