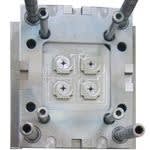
Wybór jest tu uzależniony od wielu czynników, a w szczególności od żądanej jakości, czyli właściwości mechanicznych, aspektów związanych z wykończeniem powierzchni oraz procentowej ilości odpadów.
Wszystkie formy tego typu mają oczywiście swoje zalety, głównie w postaci mniejszej ilości uplastycznianego tworzywa, nie tworzą żadnych (lub minimalne ilości) odpadów oraz posiadają krótsze cykle. Z drugiej jednak strony formy z grzanymi kanałami są droższe i cięższe, a także wymagają staranniejszej konserwacji i lepiej przeszkolonego personelu obsługi niż formy tradycyjne. Ponadto, jeżeli ich konstrukcja nie jest właściwa, wówczas ciepło wymagane do ich pracy może rozchodzić się na wszystkie części formy i paradoksalnie nawet wydłużyć czas cyklu.
Jednym ze sposobów podjęcia właściwej decyzji przy wyborze jest oszacowanie wielkości oczekiwanego zwiększenia produktywności w stosunku do formy tradycyjnej. W sytuacji, gdy oczekiwany wzrost ma być niższy niż 25 proc., wówczas zdecydowanie lepiej jest pozostać przy tradycyjnej formie trzypłytowej. Jest ona bez wątpienia tańsza jeśli chodzi o jej wykonanie, a potem także uruchomienie i użytkowanie. Kryterium wzrostu produktywności o 25 proc. odnosi się natomiast tylko do pełnych systemów z grzanymi kanałami. W przypadku pozostałych rodzajów form z grzaną dyszą oraz dodatkowymi zimnymi kanałami, uprzednio wymieniony próg jest znacznie niższy.
Warto też przybliżyć istotę wtrysku bezpośredniego w porównaniu z dodatkowymi zimnymi kanałami dla tworzyw krystalicznych.
Przy projektowaniu form z grzanymi kanałami do zastosowania z tworzywami krystalicznymi, należy pamiętać, że wtrysk bezpośredni poprzez grzane kanały jest bardziej skomplikowany dla tworzyw krystalicznych niż dla tworzyw amorficznych. Różnica polega na sposobie mięknięcia lub topienia tych dwóch typów polimerów.
Tworzywa amorficzne charakteryzują się stopniowym topnieniem powyżej temperatury od stanu stałego do stanu ciekłego, co w rezultacie daje szerszy zakres przetwarzania w zakresie temperatury i lepkości. W rzeczywistości, wzrost temperatury tworzywa amorficznego pozwala na zastosowanie go najpierw w procesie termoformingu, następnie w procesie formowania rozdmuchowego i ostatecznie w procesie formowania wtryskowego. Sytuacja wygląda zupełnie inaczej w przypadku polimerów krystalicznych. Tutaj temperatura ma ograniczony lub nawet żaden wpływ na strukturę tworzywa, które pozostaje w stanie stałym. Takie zachowanie się tworzyw krystalicznych stwarza dwa zagrożenia.
Po pierwsze wyciekanie wokół otworu wtryskowego i w konsekwencji problem z wadliwym wykończeniem powierzchni oraz deformacje. Po drugie zaś zatykanie przewężek przez zastygłe tworzywo. W tej drugiej sytuacji wepchnięte w gniazda czopy prowadzą do wadliwego wykończenia powierzchni i słabszych własności mechanicznych. Najlepszym sposobem uniknięcia tego typu problemów jest zastosowanie dodatkowych zimnych kanałów.
Wykorzystano m.in. materiały firmy DuPont.