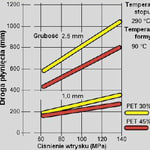
Analizując problem grubości ścian widać, że z praktyki wynika fakt, iż przy projektowaniu wyrobów z technicznych tworzyw sztucznych stale powtarzają sie pewne problemy, które o wiele łatwiej rozwiązać przestrzegając prostych wytycznych dotyczących konstrukcji. Jednym z takich problemów jest określanie grubości ścian, ponieważ wywiera ona decydujący wpływ na końcową jakość wyrobu.
Jeśli chodzi o wpływ na określone własności wyrobu i przebieg procesu, to zmiana grubości ścian wyrobu wywiera silny wpływ na takie własności i parametry jak ciężar, długości dróg płynięcia w formie, czas cyklu wtrysku, jakość wyrobu z punktu widzenia jakości powierzchni, paczenia się i powstawania jam skurczowych.
Biorąc pod uwagę stosunek drogi płynięcia do grubości ścian widać, że już na samym początku należy zastanowić sie nad tym, czy stosując wybrany materiał można będzie uzyskał wymagane grubości ścian. Stosunek drogi płynięcia do grubości ścian wywiera decydujący wpływ na sposób napełniania gniazda w trakcie procesu wtryskiwania. Jeżeli przy małych grubościach ścian trzeba w formie wtryskowej zaprojektować długie drogi płynięcia, to konieczne jest zastosowanie tworzywa o stosunkowo małej lepkości stopu. Chodzi tu o stop o dużej płynności.
Przegląd charakterystyk płynięcia stopionych tworzyw sztucznych uzyskuje sie metodą określania długości dróg płynięcia w specjalnej formie.
Sztywność płaskiej płyty przy zginaniu zależy od charakterystycznego dla tworzywa modułu E oraz od geometrycznego momentu bezwładności powierzchni przekroju płyty. W przypadku tworzyw częściowo krystalicznych dowolne zwiększanie grubości ścian w celu usztywnienia wyrobów jest bardzo często przyczyną poważnych problemów. Zmiany grubości ścian wyrobów z tworzyw wzmocnionych włóknem szklanym pociągają za sobą zmianę kierunku ułożenia włókien. W pobliżu ściany formy włókna układają sie w kierunku płynięcia. Natomiast pośrodku przekroju ścian wyrobu ułożenie włókien jest przypadkowe.
Przy zwiększaniu grubości ścian zwiększa sie przekrój, w którym włókna układają sie w sposób przypadkowy, a grubość warstwy z włóknami ułożonymi w kierunku płynięcia prawie nie ulega zmianie. Tym samym zmniejsza sie procentowy udział obszaru brzegowego w przekroju ściany, a w przypadku tworzyw sztucznych wzmocnionych włóknem szklanym właśnie ten obszar decyduje o sztywności wyrobu. Wyjaśnia to, dlaczego przy zwiększaniu grubości ścian zmniejsza sie moduł sprężystości wzdłużnej przy zginaniu.
Nieprzemyślane zwiększanie grubości ścian pociąga za sobą wzrost kosztów materiałowych i kosztów produkcji, natomiast nie zapewnia wyraźnej poprawy sztywności.
Czy zwiększać grubość ścian?
Zwiększenie grubości ścian wywiera wpływ nie tylko na własności mechaniczne, lecz także na jakość wyrobu. Przy projektowaniu wyrobów z tworzyw sztucznych należy pamiętać o konieczności zachowania jednakowej grubości ścian. Różne grubości ścian są przyczyną różnych skurczów, a to z kolei pociąga za sobą - zależnie od sztywności wyrobu - wypaczenia i problemy związane z zachowaniem dokładności wymiarowej.
Jednakowe grubości ścian można zachować wykonując wybrania w grubościennych częściach wyrobu. Zapobiega sie w ten sposób powstawaniu jam skurczowych i ogranicza naprężenia wewnętrzne. Ponadto zmniejsza sie do minimum podatność wyrobu na paczenie sie. Jamy skurczowe i mikropory w wyrobie w drastyczny sposób pogarszają własności mechaniczne, ponieważ następstwem ich występowania są przewężenia przekroju, duże naprężenia wewnętrzne, a po części również działanie karbu.