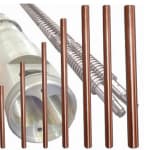
System GamartTherm zapewnia praktycznie izotermiczne warunki pracy na wszystkich powierzchniach formy. Prędkością rozchodzenia się ciepła w Heat Pinie przekracza kilkaset razy szybkość rozchodzenia się ciepła w pręcie miedzianym o tych samych wymiarach. Dzięki temu powierzchnie form szybko uzyskują temperaturę określoną dla wymagań przetwórstwa. Podczas pracy na całej długości rurki stabilizuje się stała temperatura, która na długości od parownika do skraplacza zazwyczaj mieści się w zakresie ±1 st.C. Poprawa warunków pracy urządzeń widoczna jest natychmiast. Utrzymywane są jednolite warunki formowania a proces przebiega bez zakłóceń. Maleje ilość przestojów, spada liczba awarii, zmniejsza się ilość odpadów.
Zastosowanie Heat Pinów GamartTherm:
- przetwórstwo tworzyw sztucznych i gum,
- układy plastyfikujące - termostatowania ślimaków,
- termostatowanie form,
- inne maszyny i narzędzia, czyli wszędzie tam gdzie istotne dla procesu jest wyrównanie temperatur.
Zamontowanie Heat Pinów na całej długości wewnątrz ślimaka ułatwia prowadzenie procesu wytłaczania. Tak zainstalowany przewodnik termostatuje ślimak przenosząc nadmiar ciepła z części ślimaka gdzie po uplastycznieniu masy jest go zbyt dużo i może dojść do przegrzania masy, do części ślimaka o niższej temperaturze. Przeniesienie nadmiaru ciepła do strefy zasypu, gdzie ciepła jest za mało, przyspiesza proces nagrzewania wytłaczanego surowca.
Przewody Heat Pin nie wymagają żadnej, szczególnej kontroli i konserwacji. Nie ma potrzeby stosowania wyspecjalizowanych pomiarów temperatury oraz skomplikowanej aparatury sterującej procesem. Nie potrzeba dodatkowej obsługi czuwającej nad przebiegiem procesu. To wszystko przyczynia się do zwiększenie wydajności i wzrostu zysków.
Zalety systemu GamartTherm
- umożliwia błyskawiczne ogrzanie lub schłodzenie wybranej część urządzenia oraz równomierny rozkład temperatury na całej jego powierzchni,
- gwarantuje równomierny i wydajny przebieg procesu technologicznego, umożliwiający jednorodny rozkład temperatury na całej jego powierzchni,
- eliminuje problemy związane z niedogrzaniem lub przegrzaniem pracujących urządzeń i ich części,
- daje możliwość ulepszenia receptur mieszanek, zastosowanie mniej wymagających surowców i dodatków z węższymi oknami obróbki termicznej,
- ułatwia jednolitą stabilizację mieszanek co przekłada się na lepszą jakość produktu gotowego,
- ogranicza ilość odpadów,
- umożliwia oszczędność czasu pracy i poprawę wydajności pracy,
- zmniejszenie zapotrzebowania na energię cieplną, oszczędność kosztów energii,
- gwarantuje równomierne, stabilne warunki pracy urządzeń i wydłużenie ich czasu życia.