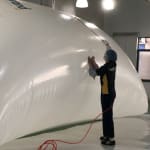
Hillebrand, operator logistyczny specjalizujący się w obsłudze branży beverage, wdraża procesy recyklingu swoich opakowań i środków transportu. Flexitanki są bezpiecznymi, wydajnymi i ekologicznymi zbiornikami do transportu płynów luzem. Hillebrand w wielu oddziałach na świecie wdrożył programy ich odzysku i recyklingu.
Już w pierwszym etapie projektowania flexitanków inżynierowie Hillebrand, w oparciu o koncepcję gospodarki o obiegu zamkniętym, uwzględnili w ich produkcji sprasowane warstwy polietylenów (LLDPE) w 100% nadające się do recyklingu. Zespoły projektowe Hillebrand badają możliwości wykorzystania polimerów pochodzących z recyklingu starych flexitanków w produkcji tych nowych. Zespół inżynierów Hillebrand prowadzi również badania nad zmniejszeniem grubości folii, wykorzystywanej do produkcji flexitanków, bez jednoczesnej utraty ich jakości. Na przykład w nowo opracowanych flexitankach ML wykorzystano o 18,6 proc. mniej plastiku niż w przypadku tradycyjnych modeli, co przekłada się na zmniejszenie emisji CO2 o 1,5 proc.
Trzy metody recyklingu lub odzysku flexitanków
Po zakończeniu rozładunku u klienta, opróżnione flexitanki są przewożone do magazynów Hillebrand. Tu usuwane są metalowe części, nadające się do ponownego użytku, a sam zbiornik jest przeznaczony do recyklingu.
Do recyklingu i odzysku flexitanków Hillebrand wykorzystuje 3 metody - mechaniczną, chemiczną oraz termiczną. W przypadku zbiorników, w których przewożono wcześniej np. wino, najlepszym rozwiązaniem jest recykling mechaniczny. Tutaj tworzywo sztuczne, z którego wykonany jest flexitank, jest sortowane, czyszczone, mielone, regranulowane i mieszane, a powstała w wyniku tych procesów żywica może być wykorzystana jako surowiec wtórny do produkcji np. folii budowlanej, worków na śmieci czy plastikowych rur. Ta metoda pozwala na zachowanie 70 proc. wartości zużytej energii, w porównaniu z jednorazowym odzyskiem termicznym.
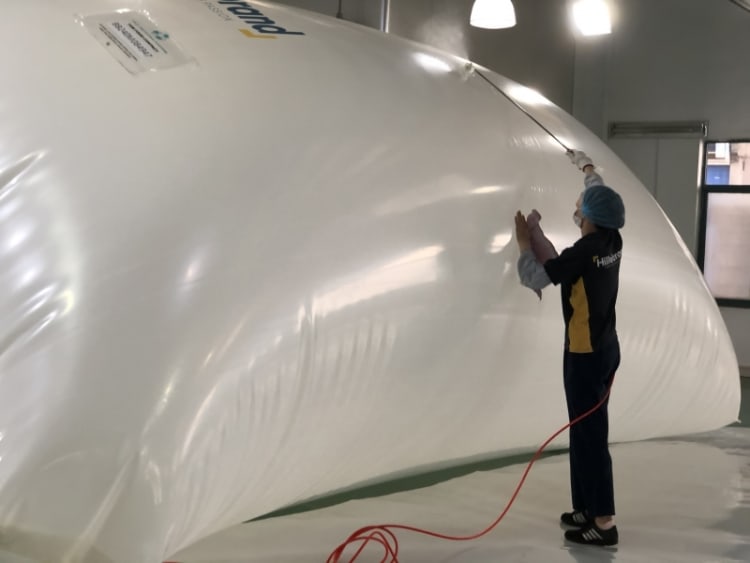
Drugim sposobem jest recykling chemiczny uznawany dedykowany klientom, którzy chcą uzyskać z utylizacji flexitanków odpady o wyższej jakości do ponownego wykorzystania. Tutaj w odzysku stosowana jest depolimeryzacja, czyli rozkład polimerów na monomery w celu wykorzystania ich jako surowiec do produkcji nowych polimerów posiadających pierwotną jakość. Inną możliwością jest piroliza - przekształcanie mieszanych odpadów z tworzyw sztucznych w benzynę do produkcji paliwa lub nowych polimerów. Odpady są przetwarzane na surowce, wykorzystywane do produkcji różnego rodzaju chemikaliów i tworzyw sztucznych. Co warto podkreślić, 1 tona odpadów tworzyw sztucznych przetworzonych w ramach odzysku energii generuje 1,8 tony CO2 w porównaniu z recyklingiem chemicznym generującym 0,4 tony CO2. Trzecim rozwiązaniem, wykorzystywanym przez Hillebrand, jest recykling termiczny albo odzysk energii, polegający na przekształcaniu materiałów odpadowych w ciepło, energię elektryczną lub paliwo za pomocą różnych metod m.in. spalania lub gazyfikacji. Najczęściej jest stosowany wtedy, gdy usunięcie resztek cieczy, ze względu na jej właściwości, nie jest opłacalne ekonomicznie.
Wybór odpowiedniej metody recyklingu
Przy wyborze odpowiedniej metody recyklingu flexitanków eksperci Hillebrand muszą uwzględnić kilka czynników. Należą do nich przepisy prawne regulujące recykling tworzyw sztucznych w danym kraju, które określają najlepszą metodę odzysku i wskazują dostępną infrastrukturę. Ważnym elementem wyboru jest efekt skali, im więcej pustych flexitanków trzeba zutylizować w danej lokalizacji, tym korzystniejsza ekonomicznie będzie budowa odpowiedniej infrastruktury. Pod uwagę brane są także właściwości przewożonego płynu i to jak łatwo jest usunąć pozostałości i oczyścić z nich powierzchnię zbiornika.
- W zakresie recyklingu flexitanków współpracujemy z autoryzowaną i certyfikowaną firmą, zajmującą się gospodarką odpadami. Możemy zapewnić dostawy pustych flexitanków do magazynu, gdzie są opróżniane i przygotowywane do dalszego recyklingu i odzysku - mówi Bartosz Mierzejewski, sales manager, Hillebrand Poland.