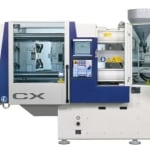
Ze względu na ekstremalnie podwyższone wymagania odnośnie produkcji elementów formowanych wtryskowo wykorzystywane są wszystkie środki prowadzące do uzyskiwania powtarzalnej jakości produkcji i podwyższania dyspozycyjności wtryskarki. W tym właśnie celu firma Krauss-Maffei rozpoczęła kilka lat temu poprawę czystości stosowanych komponentów maszyn oraz optymalizację koncepcji układu hydraulicznego wtryskarek pod kątem pielęgnacji oleju. Przedsięwzięcia te objęły wszystkie wchodzące w kontakt z olejem elementy konstrukcyjne własnej produkcji oraz komponenty kupowane.
Dla stworzenia odpowiednich warunków uzyskiwania wyższej czystości, konieczne były najpierw daleko idące procesy zmiany sposobu myślenia. Oto bowiem producenci komponentów układów hydraulicznych sądzili przykładowo, że zawory sterujące nie wymagają tak wysokiej czystości jak zawory proporcjonalne. Uznano, że ważne jest jedynie to, aby komponenty hydrauliczne o wysokiej czystości nie ulegały uszkodzeniu przez zanieczyszczenia pochodzące z innych elementów konstrukcyjnych, np. z cylindrów lub węży znajdujących się we wtryskarce. Z uwagi na to, że wszystkie komponenty pracują w jednym układzie, najbardziej wrażliwy element - zawór proporcjonalny - określa wymaganą klasę czystości dla wszystkich części.
Punktem wyjścia do podwyższenia czystości wytwarzania okazał się tzw. Component Cleanliness Audit (CCA). Element konstrukcyjny poddawany badaniom był przemywany cieczą pod ciśnieniem przefiltrowaną z dokładnością 1 mikrona. Ciecz ta była następnie przepuszczana przez membranę w celu oceny zanieczyszczenia.
Badaniu poddawana była czystość elementów lub czystość mechaniczna - wykonano badania ilościowe przy pomocy grawimetrii i badania jakościowe poprzez wykrywanie największej szkodliwej cząstki metalu lub krzemianu oraz czystość cieczy lub czystość hydrauliczna - wykonano badanie cieczy płuczącej lub próbnej przy czyszczeniu i kontrolowaniu komponentów wg ISO 4406.
Przykład ten pokazuje, że zanieczyszczona już ciecz myjąca nie nadawała się do zadawalającego usuwania pozostałości poprodukcyjnych z elementu konstrukcyjnego. Niemniej jednak setny tłok musiał być umyty z taką samą dokładnością co pierwszy, a do tego potrzebna była nieustannie oczyszczana ciecz myjąca.