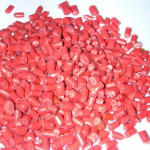
Cały proces podzielony jest na kilka etapów i rozpoczyna się od uplastycznienia tworzywa. To wtedy granulat we wtryskarce doprowadzany jest do odpowiedniej temperatury dochodzącej nawet do 400 st. C. Tak uplastycznione tworzywo wtryskiwane jest do specjalnej formy wtryskowej pod ciśnieniem ponad 1000 bar, niekiedy zaś nawet ponad dwukrotnie wyższym. Wtryskiwanie odbywa się do zamkniętej formy wtryskowej. Ilość wtryskiwanego do formy tworzywa zależy od wielkości używanej wtryskarki.
Po wtryśnięciu tworzywa do formy wtryskowej następuje skurcz tworzywa. Jest to kolejna faza procesu wtrysku termoplastu określana mianem chłodzenia. W czasie chłodzenia termoplast powraca do stałego stanu skupienia. Na tym etapie najważniejszą sprawą jest utrzymanie stałej temperatury formy wtryskowej. Po schłodzeniu ukształtowanego termoplastu następuje otwarcie formy wtryskowej. Proces wtrysku odbywa się cyklicznie. Po otwarciu formy wtryskowej znów mamy do czynienia ze stapianiem i wtryskiem tworzywa.
Objawy | Typ tworzywa | Miejsce i czas występowania wady | Przyczyna powstawania | Możliwe sposoby zapobiegania |
---|---|---|---|---|
smugi w kierunku przepływu | wszystkie | - przy każdym wtrysku na większości powierzchni |
- wilgotny granulat;
- rozpad termiczny |
- sprawdzić zawartość wilgoci w granulacie;
- sprawdzić proces suszenia; - sprawdzić temperaturę uplastyczniania |
efekt marmurkowy | z wypełniaczami mineralnymi |
- przy każdym wtrysku;
- poza ostrymi kantami; - w pobliżu przewężki |
- zbyt duża prędkość ścinania;
- efekt slip-stick (przesunięcia warstwy naskórkowej) |
- obniżyć prędkość wtrysku, ewentualnie zmienić jego profil;
- zaokrąglić ostre krawędzie; - zwiększyć przewężkę |
zimne korki | wszystkie, szczególnie wzmocnione |
- występuje często tylko w jednym miejscu;
- przebiega przez całą grubość ściany |
- zimne korki docierają z dyszy i gorących kanałów do wypraski |
- przewidzieć miejsca zalegania zimnych korków (w kanale);
- podnieść temperaturę dysz |
wyciągnięcia, zapadnięcia | wszystkie, szczególnie bez wypełniaczy |
- naprzeciwko żeber;
- w obszarze ze spiętrzeniem tworzywa |
- większy skurcz w miejscu nagromadzenia tworzywa (nieskuteczne ciśnienie docisku) |
- zmienić konstrukcje wypraski (węższe żebra, równomierne grubości ścian);
- zmienić położenie przewężki |
przypalone powierzchnie | wszystkie | - zawsze w tym samym miejscu | - utlenianie tworzywa w wyniku szybkiego sprężania powietrza przy braku odpowietrzeń (efekt Diesla) |
- przewidzieć, ewentualnie poprawić odpowietrzenia;
- zmniejszyć prędkość wtrysku |
nieprzetopione cząstki tworzywa | wszystkie szczególnie niewzmocnione | - sporadycznie w różnych miejscach | - tworzywo źle uplastycznione lub niedostatecznie ujednorodnione |
- sprawdzić temperaturę uplastyczniania (może być za niska);
- podnieść ciśnienie wtrysku; - sprawdzić obroty ślimaka przy uplastycznianiu; - zastosować większą jednostkę uplastyczniającą (dłuższy czas przebywania tworzywa) |
wolny strumień | wszystkie |
- przy każdym wtrysku;
- najczęściej rozpoczyna się od przewężki |
- strumień stopionego tworzywa wtryskiwany jest przez przewężki, tak że nie styka się ze ścianami gniazda formy;
- brak wypełnienia "od źródła" |
- wtryskiwać z mniejszą prędkością, aby uzyskać wypełnienie od źródła;
- przewidzieć za punktem wtrysku rozbicie strumienia tworzywa; - zmienić sposób doprowadzenia tworzywa |
sporadycznie występujące brązowe plamy | wszystkie | - 5-15 wtrysków prawidłowych, później 1-2 wtryski nieprawidłowe i dalej cykl się powtarza | - tworzywo zalega w dyszy, gorących kanałach lub w komorze wstępnej, gdzie ulega rozpadowi, po czym dostaje się tam świeże tworzywo i proces powtarza się |
- poprawić zmiany kierunku płynięcia;
- usunąć miejsce zalegania tworzywa |
szorstka powierzchnia, zabielenia | typy z wypełniaczami |
- na końcu drogi płynięcia;
- poza kantami i zmianą kierunku płynięcia; - w obszarze żeber |
- chwilowe zatrzymanie czoła strumienia;
- tworzywo krystalizuje, zanim dotrze do ścian formy; - włókna szklane leżące na powierzchni |
- podnieść prędkość wtrysku;
- sprawdzić temperaturę uplastyczniania; - sprawdzić punkt i sposób przełączania na ciśnienie docisku (nie wypełniać pod ciśnieniem docisku) |
W tekście wykorzystano materiały z publikacji wydawnictwa Verlag Dashofer "Tworzywa sztuczne w praktyce".