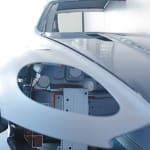
Najpopularniejszą metodą produkcji wyrobów z kompozytów polimerowych jest technika kontaktowa (laminowania ręcznego). Sprawdza się, gdy wyrób powstaje bez stosowania wysokich temperatur i ciśnienia, za to w wyniku kontaktu materiałów wyjściowych z nieskomplikowaną jednostronną formą.
Zaletą metody jest brak ograniczeń co do gabarytów wyrobu oraz możliwość wykonywania wyrobów nawet o dość skomplikowanym kształcie. Wykonuje się je wtedy w postaci skorupy uzyskanej w odpowiednio dzielonej formie lub jako zestaw kształtek z kilku form. Takie kształtki są łączone monolitycznie w kolejnych operacjach laminowania.
Metodą formowania kontaktowego można produkować zarówno niewielkie obudowy sprzętu laboratoryjnego i elektronicznego, jak i osłony maszyn, karoserie samochodowe, łodzie żaglowe i kutry rybackie.
Metoda nakłada jedynie pewne ograniczenia co do wykonania i konstrukcji wyrobów. Tylko jedna powierzchnia produkowanego detalu jest gładka, czyli posiada fakturę powierzchni formy. Druga powierzchnia ma fakturę zbliżoną do faktury stosowanego wzmocnienia.
Grubość ścianek wyrobu, formowanych ręcznie z wielu warstw kompozytu, nie jest równomierna. Zawartość włókna wzmacniającego zależy od formy użytego wzmocnienia i wynosi dla maty szklanej ok. 30 proc., a dla tkaniny ok. 40 proc.
W przypadku maty szklanej rozłożenie włókna szklanego w wyrobie jest przypadkowe. W przypadku. stosowania tkanin lub włókna ciągłego można w pewnym zakresie uzyskać pożądaną kierunkowość tych własności.
Niektóre cechy wyrobu można uzyskać stosując określone rozwiązania konstrukcyjne. Na przykład zwiększaną sztywność wyrobów otrzymuje się za pomocą odpowiednich przetłoczeń ścianek wyrobu, żeber uformowanych na jego wewnętrznej powierzchni, konstrukcji przekładkowej czy przez stosowania włókien o wyższym module sprężystości, np. wstawek z włókna węglowego w kompozycie z włókna szklanego.
Należy także pamiętać, że jakość wyrobu produkowanego metodą kontaktową zależy w dużym stopniu od dobrze przygotowanej technologii produkcji, przestrzegania zawartych w niej procedur i operacji kontroli i samokontroli. Zależy także od rzemieślniczych umiejętności i solidności bezpośredniego wykonawcy wyrobu. Zatem czynnik ludzki odgrywa tu istotną rolę.
Odmianą metody kontaktowej jest metoda natrysku. W metodzie tej nie stosuje się włókien wzmacniających w postaci mat i tkanin, lecz włókno ciągłe. Najczęściej spotyka się je w postaci tzw. rowingu szklanego. Włókno to jest za pomocą specjalnych urządzeń cięte i - równocześnie z kompozycją żywicy - natryskiwane na formę, tworząc na niej rodzaj luźnego kożucha.
Po jego dociśnięciu do formy za pomocą pędzli i wałków, podobnie jak w klasycznej metodzie kontaktowej, powstaje skorupa wyrobu. Metoda ta pozwala na stosowanie włókien wzmacniających w tańszej postaci, mechanizuje niektóre elementy procesu produkcyjnego oraz wymusza uporządkowanie procesu wytwarzania. Równocześnie jednak utrudnia kontrolę grubości wyrobu, który przy stosowaniu mat i tkanin szklanych jest regulowany ilością nałożonych warstw wzmocnienia.
Natrysk, obok nakładania pędzlem, stosuje się także do formowania w wyrobach kompozytowych warstwy tzw. żelkotu, czyli warstwy barwionej żywicy; spełniającego w tych wyrobach funkcję warstwy ochronnej i dekoracyjnej. Stosowanie urządzeń natryskowych zwiększa oczywiście nakłady inwestycyjne na uruchomienie produkcji.
W tekście wykorzystano materiały firmy Bella.