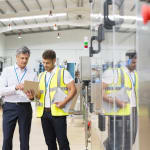
Według Bitkom (Niemieckiego Federalnego Stowarzyszenia Technologii Informacyjnych), segment budowy maszyn jest nadal najsilniejszym motorem wzrostu w aplikacjach Przemysłu 4.0, a za nim plasują się sektory motoryzacyjny i elektroniczny. Coraz więcej firm korzysta z nowych możliwości cyfrowych, aby poprawić wydajność swojej działalności i zmniejszyć koszty związane z produkcją, łańcuchem dostaw i konserwacją.
W dziedzinie innowacji cyfrowych wiele firm zakończyło już fazę testów i optymalizacji, a obecnie dąży jedynie do poprawy swojej globalnej konkurencyjności w zrównoważony sposób. W dzisiejszych czasach firmy są w stanie zarządzać wszystkimi procesami biznesowymi za pomocą zdefiniowanych wskaźników wydajności. Coraz więcej firm polega teraz na zarządzaniu sprzedażą poprzez systemy CRM, na optymalizacji marketingowej poprzez cyfrową ocenę wyników oraz na planowaniu produkcji poprzez MES (systemy realizacji produkcji).
W tym celu należy określić odpowiednie parametry poprzez dokładne pomiary i przedstawić je do analizy, aby podejmować decyzje przyjazne dla użytkownika. Procesy zarządzania produkcją już teraz opierają się na dużych ilościach danych, w tym na prognozach sprzedaży w kwestii planowania. Zarządzanie rzeczywistym procesem produkcyjnym wymaga jednak również planowania zasobów i optymalizacji procesów łańcucha dostaw. Oprócz gromadzenia danych eksploatacyjnych, cyfrowy zbiór danych o maszynach nabiera coraz większego znaczenia w celu optymalizacji, planowania, konserwacji i skrócenia czasu pracy maszyn i systemów.
Od IoT do IIoT
Internet Rzeczy (IoT) umożliwia łączenie w sieć standardowych produktów konsumenckich i generowanie danych o ich stanie, zarówno dla poprawy ich dostępności, jak i świadczenia dodatkowych usług. Przykładowo, nowe systemy grzewcze są teraz zwykle wyposażane w zintegrowany interfejs transmisji danych. Operatorzy zazwyczaj mogą uzyskać dostęp do istotnych informacji, takich jak zużycie energii przez grzejniki czy wszelkie zaplanowane interwencje konserwacyjne, za pośrednictwem aplikacji lub strony internetowej producenta.
Dodatkową korzyścią dla producentów jest to, że dzięki dostepowi do tych danych mogą uzyskać dodatkowe informacje, takie jak komunikaty o błędach lub wartości statusu określonych komponentów maszyn. Informacje statusowe pozwalają producentom na wcześniejsze zaplanowanie czynności konserwacyjnych systemu grzewczego, zgodnie z rzeczywistymi potrzebami, a nie tylko w oparciu o regularne przeglądy.
W kontekście aplikacji przemysłowych często używa się terminu Przemysłowy Internet Rzeczy (IIoT). Opisuje on połączenie w sieć czujników i urządzeń przemysłowych, które mogą być połączone ze sobą również przez Internet. IoT i IIoT opierają się na tej samej infrastrukturze do przesyłu danych, ogólnoświatowej sieci www. W ramach IIoT szczególne znaczenie mają cyberbezpieczeństwo i ochrona danych. Transmisja danych jest zwykle szyfrowana i odbywa się za pośrednictwem wirtualnych sieci prywatnych (VPN). Systemy operacyjne bram internetowych muszą spełniać najnowsze standardy cyberbezpieczeństwa.
Jak przygotować maszynę do pracy w IIoT?
Od pewnego czasu komunikacja z maszyną to coś więcej niż tylko przesyłanie poleceń sterujących (np. wydanie polecenia uruchomienia przemiennika częstotliwości). Gromadzenie danych dotyczących temperatury i prądu silnika jest współcześnie standardem. W wielu przypadkach dane te są jednak wykorzystywane wyłącznie do wykrywania krytycznych odchyleń od normalnych warunków pracy w celu ochrony systemu przed uszkodzeniem.
Przykładowo, dzisiejsze wyłączniki silnikowe mogą mapować konfigurację silnika i rejestrować jego prądy. Jeśli zostanie przekroczona pewna wartość progowa w przypadku zwarcia lub przeciążenia, wyłącznik zadziała, aby chronić silnik przed uszkodzeniem. Jednakże, zadziałanie urządzenia ochronnego zwykle prowadzi do przerwy w działaniu systemu. Chociaż nie da się tego uniknąć w przypadku zwarcia, takie przerwy serwisowe są zazwyczaj możliwe do opanowania, pod warunkiem, że wyłącznik może być ponownie włączony po usunięciu przyczyny usterki. Jednakże, jeśli przeciążenie spowodowane jest zużyciem mechanicznym, na przykład uszkodzonym łożyskiem na taśmie przenośnika, rozwiązanie problemu może potrwać znacznie dłużej, w zależności od dostępności serwisantów i niezbędnych części zamiennych. W takich przypadkach idealnym rozwiązaniem byłoby nie tylko wyłączenie sprzętu w przypadku jego uszkodzenia, ale przede wszystkim niedopuszczenie do jego uszkodzenia. Tutaj właśnie wkracza transformacja cyfrowa, która pozwala maszynom na zbieranie dodatkowych danych i sprawia, że są one w stanie zrobić znacznie więcej niż tylko wyłączyć się w przypadku awarii.
W wielu zastosowaniach prąd silnika jest dobrym wskaźnikiem uszkodzeń mechanicznych, ponieważ jego stopniowy wzrost w czasie sygnalizuje prawdopodobieństwo zbliżającej się awarii. Informacje te mogą być następnie uzupełniane o dane z dodatkowych czujników. Inteligentny aparat łączeniowy, który wymaga mniejszego okablowania i ma mniejszą powierzchnię zabudowy, jest często najlepszym rozwiązaniem w tej sytuacji.
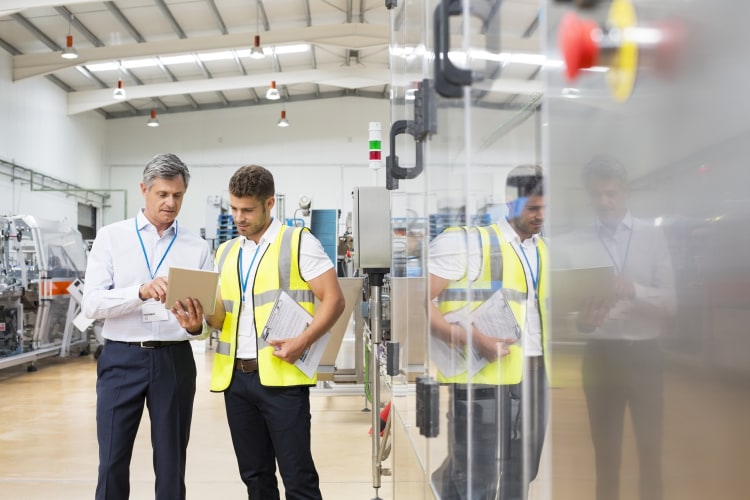
: Dane o maszynie mogą być wykorzystane do monitorowania stanu maszyny i planowania serwisowania, aby uniknąć nieplanowanych przestojów