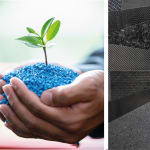
W swojej działalności biznesowej Lanxess kładzie nacisk na zrównoważony rozwój, wspierając w ten sposób gospodarkę o obiegu zamkniętym. Najnowszy owoc tego podejścia stanowią kompozyty termoplastyczne Tepex, wytwarzane z surowców biologicznych lub pochodzących z recyklingu.
- Za pomocą tych materiałów konstrukcyjnych chcemy wesprzeć naszych klientów w tworzeniu bardziej zrównoważonych produktów, które pozostawiają mniejszy ślad węglowy, oszczędzają zasoby i chronią klimat - wyjaśnia dr Dirk Bonefeld, szef marketingu i zarządzania produktami marki Tepex na rynkach globalnych w Lanxess. Specjalistyczny koncern chemiczny wprowadził niedawno na rynek w pełni biopochodny materiał kompozytowy oparty na lnie i kwasie polimlekowym.
Dostosowany do lekkich konstrukcji
Wkrótce zakończą się prace rozwojowe nad tworzywem sztucznym o osnowie poliamidu 6 na potrzeby Tepex dynalite. Wytwarza się je z "zielonego" cykloheksanu – to oznacza, że materiał ten w ponad 80 procentach składa się z surowców odnawialnych. W rezultacie tworzywo spełnia wymagania, które koncern Lanxess postawił przed swoją nową linią „Scopeblue”. W jej skład wchodzą produkty, które zawierają znaczną część surowców cyrkularnych (pochodzących z recyklingu lub bioproduktów) lub pozostawiają znacznie mniejszy ślad węglowy niż produkty konwencjonalne. W przypadku wzmocnienia tworzywa sztucznego osnowy tkaninami z włókien ciągłych, powstałe półprodukty wykazują te same znakomite właściwości, co porównywalne, równorzędne produkty oparte wyłącznie na surowcach kopalnych. Półprodukty o ekologicznej osnowie nadają się tym samym do zastosowań w lekkich konstrukcjach strukturalnych, typowych dla Tepex dynalite, takich jak pasy przednie, obudowy siedzisk czy tace akumulatora.
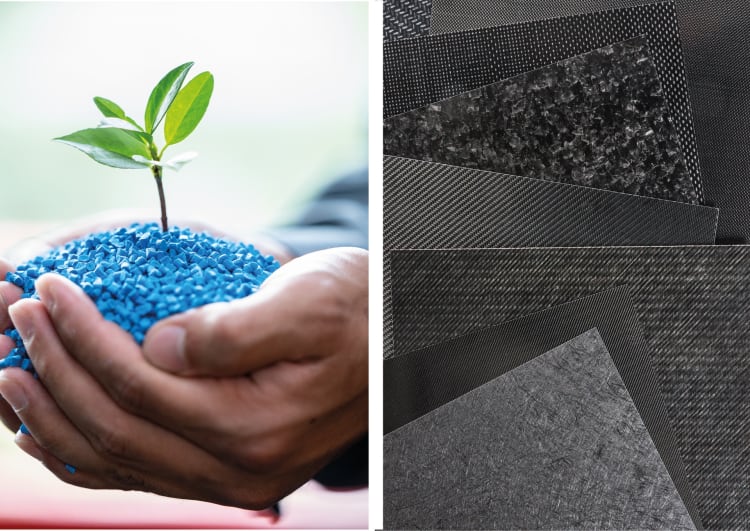
Wysoki poziom estetyczny i doskonałe właściwości mechaniczne
Kolejna nowa linia produktów obejmuje Tepex w wariantach wykorzystujących materiał pochodzący nawet w 80 procentach z recyklingu, które pozwalają uzyskać powierzchnie o wyglądzie tzw. kutego węgla. Elementy charakteryzują się ziarnistością przypominającą marmur. Większa część materiałów pochodzących z recyklingu opiera się na włóknach węglowych uzyskanych z odpadów poużytkowych i poprzemysłowych. Włókna stosuje się w postaci włókniny lub mat z włókien ciętych. Jako materiał osnowy wykorzystuje się z kolei różne tworzywa termoplastyczne, takie jak poliamid 6 i 66, polipropylen lub poliwęglan, przy czym używać można również materiałów z recyklingu składających się z tych tworzyw.
Włókna w półprodukcie kompozytowym nie mają preferowanej orientacji, co oznacza, że właściwości mechaniczne powstałych elementów są izotropowe (takie same we wszystkich kierunkach). Parametry mechaniczne nowych kompozytów węglowych zbliżone są do wysokiego poziomu kompozytów z linii Tepex wzmacnianych ciągłym włóknem szklanym. - W przypadku tych produktów widzimy obiecujące możliwości w zastosowaniach, które wymagają jednocześnie wysokiego poziomu estetycznego, jak i doskonałych właściwości mechanicznych, na przykład we wnętrzu i na zewnątrz samochodu lub w obudowach elektroniki użytkowej - wyjaśnia dr Dirk Bonefeld.
Biopochodne alternatywy dla poliamidu 12
Kolejnym kierunkiem prac rozwojowych są nowe osnowy dla materiałów z linii Tepex oparte na pochodzącym z recyklingu termoplastycznym poliuretanie (TPU) lub politereftalanie etylenu (PET), jak również na biopochodnym poliamidzie 10.10. Produkty z przetworzonego TPU znajdują zastosowanie przede wszystkim w sprzęcie sportowym. Do ich mocnych stron należy dobra adhezja kompozytowa z wieloma innymi materiałami formowanymi wtryskowo przy obróbce metodą insertowania lub formowania hybrydowego. Półprodukty z osnową z recyklatu PET są opłacalną alternatywą na przykład dla pierwotnego poliwęglanu i poliamidu. PET uzyskuje się ze zużytych butelek po napojach. Jest dostępny w dużych ilościach dzięki zamkniętemu łańcuchowi recyklingu takich opakowań. Biopochodny poliamid 10.10 pochodzi z kolei z oleju rycynowego.
- Materiały kompozytowe wykonane z jego wykorzystaniem stanowią zrównoważoną alternatywę dla kompozytów z poliamidu 12 - dodaje dr Dirk Bonefeld - mają bowiem podobne właściwości mechaniczne i porównywalną gęstość.