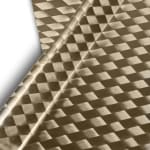
Chcąc podkreślić swoje zaangażowanie w opracowywaniu konstrukcji lekkich w przemyśle motoryzacyjnym, firma BASF powołała zespół zajmujący się lekkimi kompozytami. Grupa skupia się na rozwijaniu materiałów i technologii, które służą w przemyśle samochodowym do produkcji wysokiej jakości części i elementów wzmacnianych włóknem. Tylko lekkie, a jednocześnie mocne materiały kompozytowe mogą zastąpić metal w pojeździe.
Dzięki bogatemu portfolio produktów BASF może jednocześnie poddawać analizie trzy różne systemy matryc z tworzyw sztucznych i w ścisłej współpracy z klientami planuje rozwijać kompozycje „na miarę”. Koncern chce bazować na własnej wiedzy w dziedzinie chemii żywic epoksydowych, poliuretanowych i poliamidowych. Chce ponadto wykorzystać efekt synergii i w nadchodzących latach dokonać poważnych inwestycji - dwucyfrowych liczonych w milionach euro - w rozwój tej dziedziny.
Pierwszym osiągnięciem BASF jest opracowanie metody RTM. Pod tym skrótem kryje się technologia przetwarzania nowych materiałów „Resin Transfer Molding”, którą można wykorzystać w produkcji dużych i złożonych elementów kompozytowych w jednej operacji wyciskania-formowania.
Wymaga to wprowadzenia wielowarstwowych struktur włóknistych do ogrzanej formy, która jest zamontowana w prasie. Następnie wtryskuje się do formy ciekłą żywicę całkowicie nasączającą włókna, po czym utwardza się ją w sposób kontrolowany.
W nowo powstałym laboratorium BASF w niemieckim Ludwigshafen i w centrum badań poliuretanu specjaliści BASF pracują nad pokonaniem chemicznych i technicznych problemów stawianych przez nowe systemy matryc kompozytów. Części samochodowe, które w przyszłości powstaną z tych materiałów, będą mimo niskiej wagi wytrzymywać duże obciążenia.
Oprócz własności mechanicznych części wykonanych z kompozytów wzmocnionych włóknem, dobra płynność żywicy, a przede wszystkim krótki czas twardnienia jej składników, odpowiadają najważniejszym wyzwaniom stawianym trzem opracowywanym materiałom. Pod marką Baxxodur i Elastolit R BASF już dziś oferuje rozwiązania oparte odpowiednio na systemach epoksydowych i poliuretanowych.
Systemy na bazie żywicy epoksydowej są używane do produkcji łopat wirnika turbin wiatrowych. Oba rozwiązania stosują nowe mechanizmy utwardzania. Niska lepkość początkowa pozwala na bardzo dobrze nasączenie struktury włókien, po czym w zaledwie kilka minut dochodzi do twardnienia. Usuwa to jeden z problemów, które uprzednio stanowiły przeszkodę w wykorzystaniu wysokiej jakości kompozytów do produkcji samochodów.
Ponieważ są to układy samowyzwalające, to mogą być przetwarzane na istniejącym sprzęcie tak wysokiego, jak i niskiego ciśnienia. Ponadto aktualnie opracowywane nowe systemy poliamidowe łatwo poddają się spajaniu, a także recyklingowi jak termoplasty.
Elementy konstrukcyjne podwozia lub komponenty karoserii mogą być także wykonane tylko z materiałów kompozytowych opartych na włóknach ciągłych węglowych lub szklanych. Wymagają wtedy tego, by włókna stanowiły ok. 65 proc. masy kompozytu.
Włókna ciągłe są już stosowane w samolotach i elektrowniach wiatrowych oraz innych konstrukcjach, w prototypach i w krótkich seriach zastosowań w przemyśle motoryzacyjnym. Włókna węglowe jako materiał wzmacniający zapewniają dużą sztywność, a zatem są szczególnie interesujące.
Warto wiedzieć, że aby cały system składający się z matrycy z tworzywa sztucznego i z wzmocnienia z włókien, poddawał się przetwarzaniu według obliczalnych zasad i dawał się łatwo przystosować do produkcji w dużych ilościach, to komponenty kompozytowe w porównaniu do tradycyjnych, metalowych muszą mieć ciężar mniejszy o około 50 proc.
Dotychczas stosowane technologie, polegające na osadzaniu w tworzywie sztucznym wstawek z płytek metalowych lub wzmocnionych włóknem termoplastycznych mat i taśm UD (jednokierunkowe wzmocnienie włóknem), są uzupełniane o nowe rozwiązania. Ponadto warstwy wzmocnione włóknem ciągłym można łączyć z lekkim rdzeniem z pianki w celu uzyskania wysokiej jakości struktury wielowarstwowej o wyjątkowo dobrej sztywności konkretnych części i dobrych właściwościach izolacyjnych w połączeniu z niewielkim ciężarem. Systemy piankowe PU opracowane dla takich części przez BASF charakteryzują się wysoką wytrzymałością na ściskanie i odpornością na ciepło w połączeniu z niską gęstością.