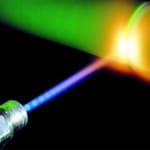
Technologia formowania wtryskowego wykorzystującego dwa materiały oraz metoda tłoczenia na gorąco są już wykorzystywane przy produkcji tzw. detali MID (ang. Moulded Interconnect Device). Obydwie z tych metod wykorzystują specjalne narzędzia do stworzenia obwodu drukowanego na powierzchni komponentu. Koszty wytworzenia połączone z tym procesem są początkowo dosyć wysokie. Fakt ten w dużym stopniu wpływa na ograniczenie ich efektywności dla małych partii produkcji oraz hamuje wprowadzanie modyfikacji. Tworzenie prototypów tuż przez zapoczątkowaniem seryjnej produkcyjnej jest prawie niemożliwe. Ponadto, wzrastająca miniaturyzacja podzespołów montowanych na elementach MID, prowadzi do znaczącego wydłużenia czasu zaopatrzenia w odpowiednie narzędzia oraz wzrostu kosztów. Warto wyjaśnić, że pod pojęciem MID kryją się wszelkiego rodzaju formowane wtryskowo termoplastyczne część ze zintegrowaną ścieżką obwodu spotykane w takich branżach jak elektronika, telekomunikacja, motoryzacja i sektor medyczny.
Alternatywę stanowi tu metoda LDS (ang. Laser Direct Structuring).
Proces LDS wykorzystuje termoplastyczne materiały lakierowane przy pomocy tworzywowo – metalowych dodatków i aktywowane laserem. Technologia LDS jest bardzo elastyczna, ponieważ laser bezpośrednio przenosi obraz z komputera na uformowany wtryskowo komponent z tworzywa sztucznego. Strukturyzacja ma miejsce wyłącznie na podstawie istniejących danych CAD. Koszty oprzyrządowania są zredukowane, ponieważ laserowo ukształtowane elementy MID mogą zostać stworzone przy zastosowaniu formowania wtryskowego dla jednego komponentu. Lasery są idealne dla produkcji bardzo precyzyjnych struktur na tworzywowych detalach typu MID.
Cały proces LDS składa się z kilku etapów.
Pierwszy z nich to selekcja materiałów i projektowanie. Dostępna jest duża liczba różnego rodzaju materiałów lub tworzyw termoplastycznych, które są niezbędne do tego, aby móc wyprodukować uformowane wtryskowo detale MID w oparciu o technologię LDS. Materiały te są odpowiednie dla wielu odmiennych aplikacji, cechuje je szerokie spektrum właściwości. Do materiałów tych zaliczyć można PA6 posiadający bardzo wysoką stabilność kształtu w funkcji temperatury odpowiednią do lutowania technologią rozpływową oraz bardzo dobre właściwości mechaniczne.
Kolejny nadający się do tej metody materiał to m.in. tworzywa PBT, PET i mieszanki. Wszystkie one cechują się dobrymi właściwościami mechanicznymi i elektrycznymi oraz bardzo wysoką stabilnością kształtu funkcji temperatury.
Kolejnym etapem po selekcji materiałów i projektowaniu jest formowanie wtryskowe. Części o skomplikowanym kształcie mające być poddane dalszej obróbce laserem są pojedynczo wytwarzane na wtryskarce. Suchy, wstępnie podgrzany granulat tworzywa jest wtryskiwany pod wysokim ciśnieniem do formy.
Po schłodzeniu, sztywny komponent staje się dokładną repliką formy. Uformowany wtryskowo detal MID jest gotowy na strukturyzację przeprowadzaną za pomocą lasera 3D.
Wtedy też następuje aktywowanie laserem. Takie tworzywo termoplastyczne posiada specjalny dodatek w postaci związku organicznego, który jest aktywowany poprzez reakcję fizyczno-chemiczną inicjowaną przez skupioną wiązkę lasera. Pęknięcia rozbijają wiązania złożonych związków domieszkowanego tworzywa i odrywają atomy metalu. W ten sposób powstają jądra do nanoszenia w kolejnym etapie warstwy pokrycia miedzią. W dodatku po aktywizacji laser powoduje jednocześnie powstanie mikroskopijnie małej nieregularności powierzchni.
Metalizacja to kolejna część procesu LDS. Etap ten ma na celu usunięcie zabrudzeń. Po nim następuje końcowy montaż elementów MID.
Wiele laserowo aktywowanych tworzyw o wysokim stopniu stabilności kształtu w wysokich temperaturach, takich jak PA6/6T, LCP i wzmacniane włóknami PBT, mogą być lutowane rozpływowo i dlatego są kompatybilne ze standardowym procesem montażu SMT.
Lutowie może być nanoszone za pomocą sitodruku. Jednakże jest to możliwe wyłącznie dla płaskich powierzchni na tym samym poziomie. Nanoszenie pasty za pomocą dyspensera powinno być zastosowane jeżeli występują elementy na różnych wysokościach lub lutowie ma być nanoszone w otworach.
To samo odnosi się do montowania komponentów tworzywowych SMD. Jeżeli wszystkie komponenty znajdują się na tym samym poziomie, to wówczas możliwy jest automatyczny montaż. Wypukłe powierzchnie mogą być automatycznie montowane wyłącznie wtedy, gdy automat układający ma regulację osi Z. Inaczej procedura ta przebiega dla powierzchni nachylonych oraz o dowolnym kształcie. W takim przypadku automatyczny montaż jest dużo bardziej skomplikowany, a często jedynym wyjściem jest montaż ręczny. W dodatku do montażu komponentów SMD, elementy MID wytwarzane przy zastosowaniu technologii LDS są również odpowiednie dla zastosowania samych chipów półprzewodnikowych.