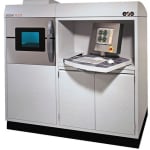
Jednym z głównych zastosowań technologii DMLS jest Rapid Tooling, czyli cała grupa procesów technologicznych wspomagających szybkie wytwarzanie form. Proces ten, jest nowoczesnym rozwiązaniem tworzenia konformalnych kanałów chłodzących trudnych do uzyskania metodami tradycyjnymi. To ważne, bo w momencie gdy nie tylko jakość produktu, ale też takie aspekty jak kształt i atrakcyjny wygląd przesądzają o sukcesie wyrobu, warstwowe technologie wytwarzania są standardem na rynku wytwarzania narzędzi.
Najważniejszą zaletą jest możliwość uzyskiwania dowolnych geometrii oraz tworzenia kanałów o budowie dostosowanej do kształtu gniazda formującego. Kanały chłodzące położone w jednakowej odległości od powierzchni gniazda zapewniają szybkie i bardziej równomierne chłodzenie wyprasek. W efekcie skurcz jest równomierny, co z kolei wpływa na polepszenie jakości wtryskiwanych detali i tym samym skrócenie czasu cyklu oraz opłacalność całej produkcji.
Specjalistą w tego typu rozwiązaniach jest na polskim rynku choćby firma Bibus Menos, korzystająca z osiągnięć niemieckiej spółki EOS, której jest partnerem. Jej System EOSINT M 270 tworzy metalowe części poprzez selektywne topienie cienkich warstw proszku metalowego skanowanych wiązką laserową z zakresu podczerwieni. Cały proces zaczyna się od naniesienia i wyrównania warstwy proszku o grubości od 20 do 100 mikronów. Następnie wiązka laserowa o mocy 200 W stapia cząsteczki nanoproszku na powierzchni obiektu a stół obniża się o grubość warstwy. Cykl powtarza się aż do stworzenia całego obiektu, który jest idealnym odwzorowaniem pliku CAD 3D.
W komorze następuje przepływ gazu - azotu lub argonu. Oprócz krótkiego czasu wytwarzania, najważniejszą zaletą technologii DMLS jest możliwości tworzenia dowolnych geometrii bezpośrednio na podstawie zapisu elektronicznego. Jedną z najważniejszych kwestii w wytwarzaniu form w procesie DMLS jest możliwość wykonywania kanałów chłodzących o dowolnym kształcie. Dzięki temu można skuteczniej kontrolować temperaturę formy i zwiększyć efektywność chłodzenia.
Należy podkreślić, iż chłodzenie jest jednym z najważniejszych czynników w procesie wtrysku i stanowi 70 proc. całego czasu cyklu. Powinno się zatem rozważyć skrócenie etapu chłodzenia formy przy jednoczesnym zachowaniu jakości wyprasek oraz ciągłości całego procesu. Równomierny rozkład temperatur w formie z wykorzystaniem tradycyjnego wiercenia bloku jest bardzo trudny do uzyskania natomiast dla technologii Direct Metal Laser Sintering nie stanowi najmniejszego problemu. Uzyskane narzędzia mogą być wykorzystywane do wtrysku milionów elementów z tworzyw sztucznych lub tysięcy metalowych części w procesie odlewania ciśnieniowego.