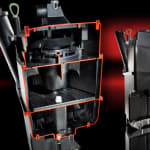
Pomysłowa geometria i równie pomysłowy materiał
Zbiornik na olej wyróżnia się zaawansowaną geometrią: składa się z 10 różnych, wtryskowych części poliamidowych, połączonych z 13 kolejnymi elementami, takimi jak: czujniki, sita, pokrywy i śruby, tworząc jeden komponent. Składa się go przy użyciu odprężania wibracyjnego w procesie spawania oraz różnych mechanizmów zatrzaskowych. Optymalne wykorzystanie dostępnej przestrzeni sprawia, że w komponent można wbudować wiele różnych funkcji. Poza przechowywaniem oleju odpowiada on za wentylację skrzyni korbowej, w tym separację oleju, a także umożliwia uzupełnianie i wymianę oleju oraz kontrolę jego poziomu i jakości. Ponadto spowalnia napływ i wstępnie filtruje spływający olej.Zastosowany Ultramid® wyróżnia się świetną odpornością na olej i korozję oraz zachowuje stabilność termiczną do 180°C (a nawet 240°C przez krótkie okresy czasu). Co więcej, jego zastosowanie ogranicza drgania i hałas z uwagi na właściwości tłumiące i sztywność materiału. Oznacza to, że zbiornik z tworzywa sztucznego jest znacznie cichszy niż wersje z metalu. Sprawdzony poliamid PA66 również charakteryzuje się odpowiednią sztywnością dla tego zastosowania, dzięki której materiał może wytrzymać zakładane ciśnienie rozrywające.
Precyzyjne projektowanie zapewnia lepszą dynamikę jazdy
- Nowy zbiornik oleju wyprodukowany z tworzywa BASF to nie jest po prostu przeróbka starego modelu ze spawanego aluminium - wyjaśnia Thomas Wolf, szef działu sprzedaży technicznej w spółce Hummel-Formen. - Zoptymalizowaliśmy konstrukcję komponentu w taki sposób, żeby ograniczyć jego wagę i sprawić, aby był cichszy i bardziej kompaktowy. Można go zainstalować wewnątrz komory silnika, pod zderzakiem. Tak złożonej konstrukcji wewnętrznej, obejmującej różne elementy i funkcje umożliwiające separację oleju, nie dałoby się wytworzyć z metalu.ElringKlinger odpowiada za cały zbiornik – począwszy od koncepcji, obliczeń i prototypów, skończywszy na matrycach do produkcji seryjnej i właściwej produkcji. Prace rozwojowe, czyli droga od modelu 3D do pierwszych działających prototypów wykonanych przy użyciu form silikonowych, trwały 12 tygodni. Produkcja pierwszych części przy pomocy matryc do produkcji seryjnej trwała około roku.
Wysiłek konstrukcyjny przełożył się m.in. na lepszą dynamikę jazdy Mercedesem AMG GT: pojazd ma niżej umieszczony środek ciężkości, więc lepiej trzyma się drogi, osiągając wyższe prędkości na zakrętach.