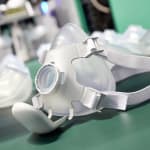
Oprócz produkcji okularów ochronnych firma Arburg powołała do życia kolejny projekt, zapobiegający rozprzestrzenianiu się koronawirusa: od 11 maja formowane wtryskowo są maski z na usta ciekłego silikonu i polipropylenu. Wielofunkcyjne maski nadają się do sterylizacji, a dzięki temu do wielokrotnego użytku.
Zaawansowana technologia: wyrób z LSR samodzielnie zaprojektowany i wytwarzany w Loßburgu
Firma Arburg samodzielnie zaprojektowała zaawansowane technologicznie i trwałe maski oddechowe, a następnie wyprodukowała pierwsze prototypy metodą addytywną na maszynach freeformer. Produkt składa się z miękkiej maski z ciekłego silikonu, zakładanej na nos i usta, i sztywnej tarczy polipropylenowej z oczkami do mocowania elastycznych pasków. Na środku znajduje się znormalizowane przyłącze z otworem (DIN EN ISO 5356-1:2004). Zapotrzebowanie jest ogromne. Zautomatyzowana produkcja seryjna tych obu komponentów jest realizowana w Loßburgu na dwóch elektrycznych maszynach Allrounder. Każdego dnia przewidywana produkcja wynosi około 3500 masek oddechowych.
Wielofunkcyjność: maski do codziennego noszenia, opieki nad chorymi
Elastyczne, zaawansowane technicznie maskisą wielofunkcyjne: aby zapobiec zakażeniu, otwór zamyka się tak zwanym Flow Gate (elementem wydmuchowym). W kolejnym stopniu rozbudowy można na niego założyć obudowę filtra. Już wkrótce Arburg wspólnie z partnerami będzie wytwarzać także ten element. Przy zastosowaniu odpowiednich filtrów FFP2 lub FFP3 np. lekarze i pracownicy opieki mogą chronić się przed chorobą Covid-19.
Kooperacja: wspólna praca licznych partnerów
Symulacja ciekłego silikonu elementów i narzędzi maski oddechowej została zrealizowana we współpracy z firmą Sigma Engineering. W rekordowym czasie, wynoszącym zaledwie pięć tygodni, partnerzy Polar-Form i Foboha stworzyli odpowiednie formy wtryskowe do komponentów z LSR i PP. W realizacji formy wtryskowej uczestniczyły ponadto firmy Ewikon (zimny kanał) i männer (gorący kanał). Kolejnymi partnerami byli Barth Mechanik (chwytak) i Packmat (technika opakowań), a materiał na około 10 000 masek ufundowały firmy Wacker i Borealis. W kontynuacji projektu, polegającej na produkcji obudów filtrów, uczestniczą firmy Weber (narzędzie), Günther (gorący kanał), Küfner (materiał filtrujący), Herrmann Ultraschall (technika spawalnicza) i Packmat (technika opakowań).