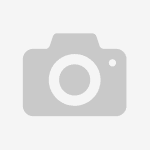
Nowa technologia opracowana przez obydwa podmioty została właśnie wdrożona w firmie PCC Synteza. Jej zakres to 15 tys. ton rocznie. W przyszłości planowane jest jej rozszerzenie do 20 tys. ton w skali roku. Nowa technologia otrzymywania Bisfenolu A odznacza się 15 - letnim czasem życia katalizatora. Warto wiedzieć, że od przyszłego roku oferowany będzie projekt procesowy i licencja na instalację do produkcji Bisfenolu A w skali 100 tys. ton rocznie.
Bisfenol A (BPA) to jeden z najważniejszych surowców wykorzystywanych w technologii wytwarzania tworzyw sztucznych oraz żywic i farb epoksydowych. Otrzymywany jest w warunkach przemysłowych na drodze kondensacji fenolu i acetonu w obecności kwaśnych żywic jonowymiennych. Oprócz Bisfenolu A, w procesie powstają również liczne produkty uboczne, wpływając niekorzystnie na selektywność reakcji.
Aby lepiej zrozumieć genezę, powody i czynniki, które doprowadziły do opracowania omawianej technologii warto wrócić do przeszłości.
Przez ostatnie 34 lata w Instytucie Ciężkiej Syntezy Organicznej w Kędzierzynie - Koźlu opracowana została oryginalna technologia, charakteryzująca się selektywnością 95 proc., porównywalną wówczas z innymi procesami BPA. Technologia ta umożliwiała otrzymywanie Bisfenolu A o czystości spełniającej wymagania niezbędne dla produkcji żywic epoksydowych i poliwęglanów.
W oparciu o tę technologię wybudowano cztery instalacje. Powstały one w PCC Synteza (12 tys. t/r), na Tajwanie (20 tys. t/r), w Chinach (12 tys. t/r) i w Indiach (7 tys. t/r). Osiągnęły zadowalające wyniki w zakresie selektywności procesu oraz czystości produktu powyżej 99,9 proc. Cztery lata temu uruchomiona została piąta instalacja w Iranie (30 tys. t/r), ale od tego czasu nie zawarto żadnego nowego kontraktu.
Powód?
Po prostu technologia, której początki datowane były na 1974 r. przestała już być konkurencyjna w stosunku do nowych rozwiązań firm dominujących na globalnym rynku. Te firmy to Bayer, Sabic Innovative Plastics, Mitsubishi i Dow Chemical.
Najpoważniejszą wadą starego procesu była niska produktywność katalizatora, której konsekwencją była wysoka energochłonność procesu. Jednostkowy wskaźnik zużycia pary według oferty kędzierzyńskiego Instytutu wynosił tylko dla Iranu ok.12 GJ/t, podczas gdy w oferowanej technologii Dow-Kellog, wskaźnik ten nie przekracza obecnie 6 GJ na tonę produktu.