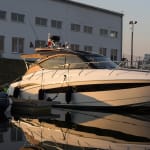
Firma Galeon jest jednym z czołowych producentów luksusowych jachtów w Europie. Jej dwa zakłady znajdują w pobliżu Gdańska. Jachty motorowe firmy Galeon mają długość do 25 m, a ich główne komponenty, takie jak kadłub, pokład i nadbudowa, są wykonane z tworzywa sztucznego wzmacnianego włóknem szklanym. Materiał ten jest ręcznie laminowany lub wytwarzany przy użyciu infuzji próżniowej. Komponenty muszą być wytrzymałe na działanie dużych naprężeń i pozbawione jakichkolwiek wizualnych czy strukturalnych wad. System podciśnieniowy używany w procesie infuzji próżniowej musi działać bezawaryjnie i być odporny na opary żywicy. W lipcu 2013 r. firma Galeon zdecydowała się na wykorzystanie systemu próżniowego Busch z kłową pompą próżniową Mink. System ten dostarcza podciśnienie do całego działu laminatów, umożliwiając produkcję komponentów o wysokiej jakości.
Firma Galeon została założona w 1982 r. i od samego początku produkuje łodzie motorowe o długości do 25 m. Prowadzone wciąż przez założyciela przedsiębiorstwo stało się jednym z czołowych producentów luksusowych jachtów w Europie. W dwóch zakładach w pobliżu Gdańska firma zatrudnia ponad 500 pracowników. Znani architekci morscy projektują serie łodzi, które są produkowane jako modele podstawowe z możliwością dostosowania do wymagań poszczególnych klientów. Przy opracowywaniu nowego modelu najpierw tworzy się prototyp, na podstawie którego kształtuje się formę negatywową umożliwiającą laminowanie poszczególnych elementów. Największymi komponentami wytwarzanymi przy użyciu procesu infuzji próżniowej są kadłub, pokład i nadbudowa. W przeszłości firma Galeon używała eżektorów próżniowych mocowanych bezpośrednio do poszczególnych form. Na początku 2013 r., w związku z planowanym zwiększeniem produkcji w przyszłości, zaczęto szukać wydajniejszego i skuteczniejszego systemu próżniowego, który mógłby dostarczać podciśnienie do maksymalnie wielu form. Po wstępnych rozmowach firma Busch wysłała specjalistę ds. rozwiązań próżniowych do zakładu Galeona, aby ocenić wymagania projektu. Zaproponowano następnie scentralizowany system dostarczania podciśnienia zasilany przez próżniową pompą kłową Mink, ze zbiornikiem próżni oraz modułem sterownika. Firma Busch świadczyła także usługi doradcze przy konstrukcji rurociągu podciśnieniowego w obszarze laminowania. Sieć próżniowa jest wyposażona w złącza podciśnieniowe w bezpośrednim sąsiedztwie każdej formy, które umożliwiają odprowadzanie powietrza z form zgodnie z zapotrzebowaniem. Próżniowa pompa kłowa Mink umożliwia jednoczesne odprowadzanie powietrza z dwóch form kadłubów i trzech form mniejszych elementów. W przypadku zwiększenia produkcji w przyszłości można zainstalować drugą identyczną kłową pompę próżniową, która pozwoli na podwojenie wydajności systemu. Moduł sterownika i konstrukcja systemu są już przygotowane do takiej rozbudowy.
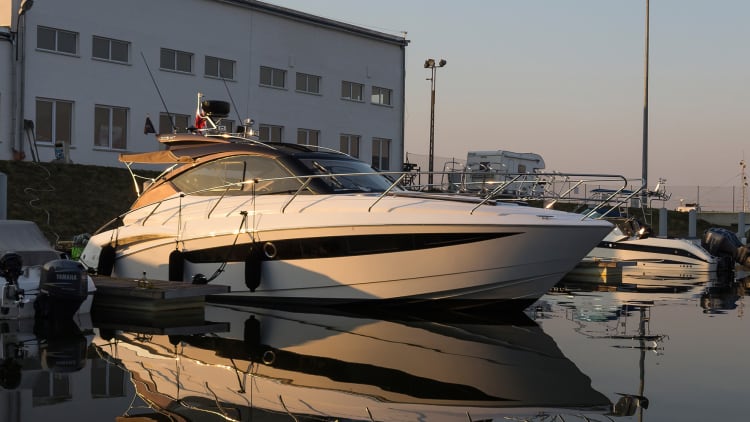
Wytwarzanie komponentów trwa od pięciu do siedmiu dni, od wprowadzenia żelkotu po wyjęcie z formy gotowego elementu. Najpierw woskuje się formę i wprowadza żelkot. Po stwardnieniu żywicy żelkotowej nakłada się ręcznie kilka warstw włókna szklanego. Następnie w formie umieszcza się suche włókno szklane. Jego ilość zależy od rozmiaru części. Po zakończeniu tego procesu pokrywa się formę folią próżniową, wstrzykuje się żywice i uszczelnia krawędzie formy. Następnie podłącza się formę do systemu próżniowego i usuwa się powietrze. Pompa próżniowa pracuje w tym czasie bez przerwy, aby umożliwić wykrycie i ręczne uszczelnienie wszelkich upływów. Czujniki podłączone do złącza podciśnienia monitorują osiągnięcie i utrzymanie wymaganego poziomu próżni, wskazując całkowitą szczelność powietrzną formy. Ta procedura pozwala upewnić się, że nie ma upływów i że folia próżniowa odpowiednio przylega. Zwykle trwa ona ok. 1-2 godz. Następnie do formy zostaje wessanych od 200 do 600 kg żywicy, w zależności od rozmiaru formy. Podciśnienie w formie zapewnia równomierne rozprowadzanie żywicy, a także zapobiega powstawaniu pęcherzyków powietrza. Następnie potrzeba jeszcze od 1 do 2 godzin, aby żywica dotarła do wszystkich części formy. Podczas tego procesu pompa próżniowa działa cały czas w trybie „automatycznym”. Oznacza to, że pompa próżniowa wytwarza wstępnie określony poziom próżni w zbiorniku przeciwprądowym, a następnie wyłącza się. Powietrze z formy wlatuje do tego zbiornika. Gdy ciśnienie w zbiorniku wzrasta powyżej określonego poziomu, pompa włącza się ponownie. W ten sposób pracuje z przerwami, oszczędzając energię.
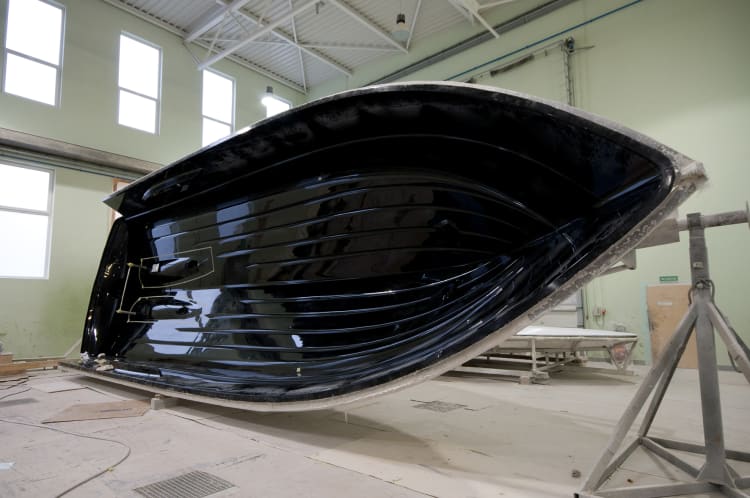
Podczas procesu infuzji forma jest kontrolowana przez personel firmy Galeon, aby zapewnić natychmiastowe usuwanie wszelkich nieszczelności. Jest to szczególnie ważne, ponieważ firma Galeon pragnie oferować klientom produkty najwyższej jakości.
Jakość produktów i niezawodność systemu to główne przyczyny wyboru firmy Busch i technologii kłowych pomp próżniowych Mink. Kłowe pompy próżniowe Mink są pompami suchymi, co oznacza, że usuwane powietrze nie styka się z cieczami roboczymi. Opary żywicy mogą reagować z cieczami roboczymi w konwencjonalnych pompach próżniowych, negatywnie wpływając na smarowanie i ograniczając wydajność systemu. Ponadto pompy próżniowe Mink pracują bezstykowo, nie zużywają się i prawie nie wymagają konserwacji. Po dwóch latach pracy technicy firmy Busch wymienili filtr wlotowy i olej przekładniowy. Kontrola pompy próżniowej nie wykazała śladów zużycia ani uszkodzeń, a na elementach wewnętrznych nie było cząstek ani osadów skondensowanych oparów żywicy.
Firma Galeon jest zadowolona z wyboru technologii próżniowych pomp kłowych Mink, ponieważ wsparcie i doradztwo ze strony firmy Busch podczas instalacji były na najwyższym poziomie. Dodatkową zaletę stanowi możliwość łatwej rozbudowy rozwiązania Busch, ponieważ firma Galeon jest pewna, że w przyszłości produkcja ulegnie zwiększeniu.
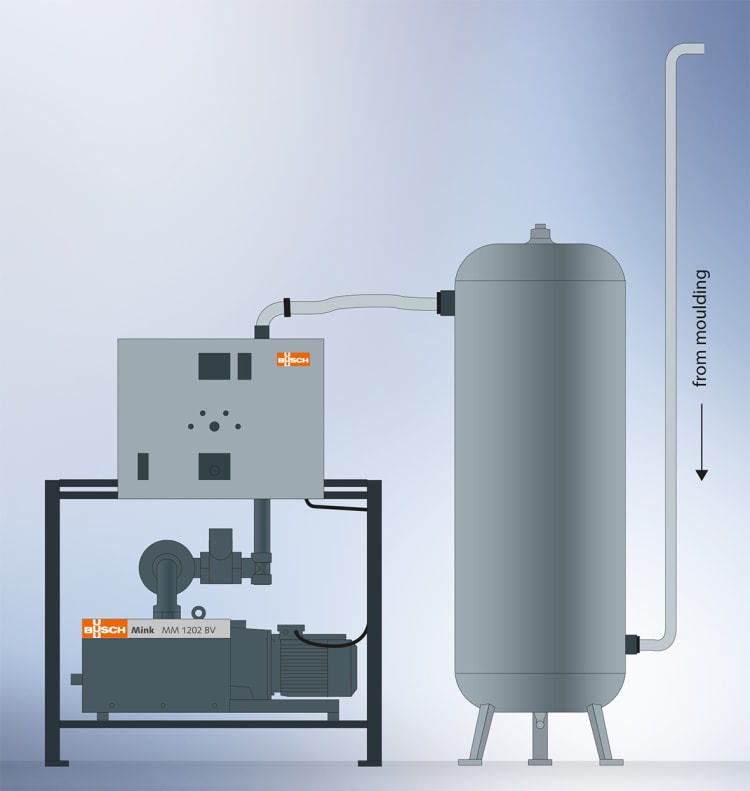