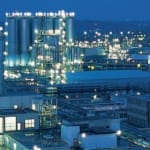
Rygorystyczne zarządzanie kosztami zakładowymi i wytwarzania ma wysoki priorytet podczas energochłonnego przetwarzania tworzyw sztucznych. Dzięki zastosowaniu nowoczesnych koncepcji wytwarzania chłodu oraz regulowania temperatury można osiągnąć znaczne obniżenie kosztów.
Minęły już czasy, w których koszty energii odgrywały raczej poślednią rolę w decyzjach inwestycyjnych - w najlepszym przypadku znikając w ogóle w bloku kosztów ogólnych. Dzisiaj bardziej sensowne może być rozważanie rozwiązań w zakresie długofalowego obniżania kosztów energii, niż dyskutowanie nad obniżeniem czasu cyklu produkcyjnego o kolejne dziesiąte sekundy.
Nowopowstałe rozwiązania systemowe, wykorzystujące dla wspólnego dobra wzajemne oddziaływania pomiędzy regulacją temperatury a wytwarzaniem chłodu, przyczyniają się do osiągnięcia przekonujących oszczędności.
Oczywiście każdy użytkownik życzyłby sobie niskich kosztów energii i wytwarzania. Oszczędności w tych sferach odbijają się przecież bezpośrednio na kosztach produktów. Wytwarzanie chłodu oraz regulacja temperatury często odbywa się nadal przy pomocy nieefektywnych systemów o nadmiernie wysokim zużyciu energii. Przyglądając się dokładniej zagadnieniu samej obróbki tworzyw sztucznych, można dość szybko zidentyfikować wszystkich "pożeraczy" energii.
Są to np. starsze, chłodzone powietrzem maszyny chłodnicze pracujące ze współczynnikiem wydajności pomiędzy 2 a 2,5. Współczynnik wydajności określa stosunek efektywnej wydajności chłodzenia do włożonej energii. Przy współczynniku wydajności równym 2 maszyna zużywa 100 kWh energii chłodzenia. Dla porównania, w podobnych warunkach nowoczesna maszyna chłodząca zużywa do 50 proc. energii mniej.
Do regulacji temperatury, także komponentów technicznych wymagających zachowania temperatury pracy w zakresie pomiędzy 40 a 90 stopni, stosuje się często konwencjonalne regulatory. Nieważne czy są to jedno-, czy dwu-, czy wieloobiegowe metody regulacji temperatury - w zakresie zużycia energii na wszystkich systemach ciąży jeden błąd.
Do wyrównania każdego odchylenia od wartości zadanej, niezależnie od tego czy w górę czy w dół, potrzebna jest dodatkowa energia. Ten zbędny nakład energii grzewczej jest wytwarzany bezpośrednio poprzez wkład grzewczy, a zbędny wydatek energii chłodzącej obciąża produkcję energii chłodzenia. W takim wypadku dochodzi więc nawet do podwójnego obciążenia pod względem użycia energii. Już tylko w tych dwóch sferach można dostrzec istotny potencjał oszczędnościowy.
Warto więc przyjrzeć się możliwości zastosowania urządzeń chłodniczych wyłącznie w miesiącach letnich. Energia stosowana do chłodzenia maszyn i narzędzi w procesach wtryskiwania oraz wytłaczania jest bardzo kosztowna. Co więcej należy liczyć się z dalszymi wzrostami kosztów, warunkowymi rosnącymi kosztami prądu. Z tego powodu maszyny chłodzące powinny być stosowane tylko wtedy, gdy jest to niezbędnie konieczne. Ma to szczególne znaczenie przy chłodzeniu narzędzi podczas formowania wtryskowego lub chłodzenia basenów przy wytłaczaniu, kiedy nieodzowna jest niska temperatura cieczy chłodniczej.