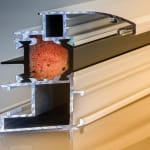
Każdy z nas zapewne nie raz otwierał butelkę napoju gazowanego, takiego jak cola, którą wcześniej wstrząsał. I jak pewnie każdy się przekonał, wystrzeliwała z niej wówczas obfita piana. W zasadzie formowanie wtryskowe pianki działa dokładnie w ten sam sposób. Do surowca dodaje się propelent, który pod wpływem wysokiego ciśnienia i wysokiej temperatury równomiernie rozpuszcza się w materiale. Jeśli do wnęki formy zostanie wtryśnięty roztwór gazowego polimeru pod ciśnieniem, spowoduje to nagły spadek ciśnienia w materiale, mieszanina stanie się przesycona, a rozpuszczony gaz ulotni się, tworząc pianę. Formowanie wtryskowe pianki, w przeciwieństwie do eksperymentu z butelką coli, odbywa się jednak w kontrolowanych warunkach - w końcu chcemy uzyskać działający komponent, a nie bałagan.
Wstępnie o spienianiu
Światowa produkcja tworzyw sztucznych rośnie nieprzerwanie od lat 80. XX w., uzupełniając lub wypierając materiały tradycyjne (w tym stal) w wielu sektorach przemysłu. Jednym z rodzajów tworzyw, które opracowano w celu zaspokojenia potrzeb przemysłu dotyczących zmniejszenia kosztów materiałowych bez utraty właściwości mechanicznych, są tworzywa porowate (pianki i gąbki).
Ogólnie rzecz biorąc, spienianie polimerów termoplastycznych jest procesem topienia tworzywa sztucznego, a następnie dodawania środka spieniającego w celu utworzenia struktury komórkowej w stopionym materiale. Spienione tworzywo sztuczne powstaje w procesie wytłaczania lub formowania wtryskowego. Technologię spieniania wykorzystuje się do produkcji takich części z tworzyw sztucznych, w których wnętrzu znajduje się spieniona struktura komórkowa.
Spienione polimery mogą być wytwarzane za pomocą poroforów chemicznych lub fizycznych. Przeznaczony do spieniania chemicznego (w temperaturze topnienia do ok. 250°C) granulat zawiera najczęściej dodatki porotwórcze zmieszane fabrycznie, które są włączane w procesie produkcyjnym lub dodawane jako przedmieszka, powodując powstawanie dwutlenku węgla lub azotu podczas topienia, w efekcie czego tworzą się pęcherzyki. Takie granulaty można przetwarzać na maszynach bez skomplikowanych dodatkowych systemów.
W przypadku spieniania fizycznego, które jest również odpowiednie dla wyższych temperatur, do stopu podczas wytłaczania lub formowania wtryskowego wtryskiwane są odpowiednie porofory gazowe. Dzięki temu można otrzymać materiały porowate o szerokim zakresie gęstości pozornych, najczęściej od 15 do 1000 kg/m3. Najbardziej popularnymi tworzywami, które można spieniać są: poliuretany, polistyreny, poli(chlorek winylu), polietyleny, polipropylen, kauczuki naturalne, kauczuk butadienowo-styrenowy. Także tworzywa konstrukcyjne poddaje się spienianiu: polimetakryloimidy, silikony, polietery sulfonowe i kompozyty. Kluczowe zastosowania obejmują przemysł obuwniczy, zabawkowy, motoryzacyjny, logistyczny, lotniczy, opakowaniowy i budowlany.
Tworzywa porowate można podzielić na elastyczne (gdy matryca polimerowa jest elastomerem lub kauczukiem), giętkie (gdy matryca polimerowa jest elastomerem, np. plastyfikowanym PVC, LDPE, PU) i sztywne (matrycą jest PS, nienasycone estry, żywice fenolowe, poliuretany).
Spienianie tworzyw termoplastycznych jest często stosowane ze względu na interesujące właściwości fizyczne i technologiczne przetworzonego w ten sposób materiału. Do zalet tego typu tworzyw należą m.in.: zmniejszenie masy wyrobu, mała gęstość, oszczędność kosztów i materiałów, bardzo dobre właściwości termoizolacyjne i tłumiące, zmniejszenie skurczu materiałowego, zwiększenie sztywności czy możliwość nowych zastosowań otrzymanego produktu. Nie są one jednak pozbawione wad. Należy tu chociażby wspomnieć o takich kwestiach, jak mniejsza wytrzymałość mechaniczna, skomplikowane przetwórstwo czy często negatywny wpływ na środowisko.
Spienione tworzywa termoplastyczne zawierają pęcherzyki, które albo pozostały nienaruszone podczas przetwarzania (pianka o zamkniętych komórkach), albo zostały połączone ze sobą (pianka o otwartych komórkach). Specjalnym rodzajem pianek zamknięto komórkowych są pianki integralne - produkowane najczęściej metodą wtrysku. Mają one gęstą, stabilizującą powłokę zewnętrzną, którą można również pomalować, np. zwiększając liczbę i wielkość bąbelków. Wszystkie typy są lekkie, izolują termicznie oraz tłumią dźwięk i wibracje mechaniczne. Pianki o otwartych komórkach mogą także absorbować ciecze i gazy.
Procesy spieniania tworzyw sztucznych często opierają się na konwencjonalnych środkach spieniających, takich jak fluorowęglowodory (HFC) lub węglowodory. Coraz bardziej rygorystyczne kontrole regulacyjne ograniczają lub zakazują stosowania takich związków ze względu na ich wysoki potencjał globalnego ocieplenia (GWP) i potencjał niszczenia warstwy ozonowej (ODP). Dlatego wielu producentów pragnie zastąpić lub wycofać te środki. Gazy przemysłowe mogą być bezpiecznym dla środowiska sposobem wspierania strategii wycofywania. Dwutlenek węgla jest doskonałą, ugruntowaną alternatywą dla tych szkodliwych czynników. Stanowi idealny fizyczny środek porotwórczy do spienionych polimerów przeznaczonych do zastosowań takich jak izolacja budynków (np. płyty izolacyjne XPS) oraz opakowania (np. te wykonane z pianki PE o dużej gęstości). Dwutlenek węgla łączy niski GWP i zerowy ODP z dobrą kompatybilnością z tworzywami sztucznymi. Ponadto jego użycie zapewnia znaczne korzyści finansowe.
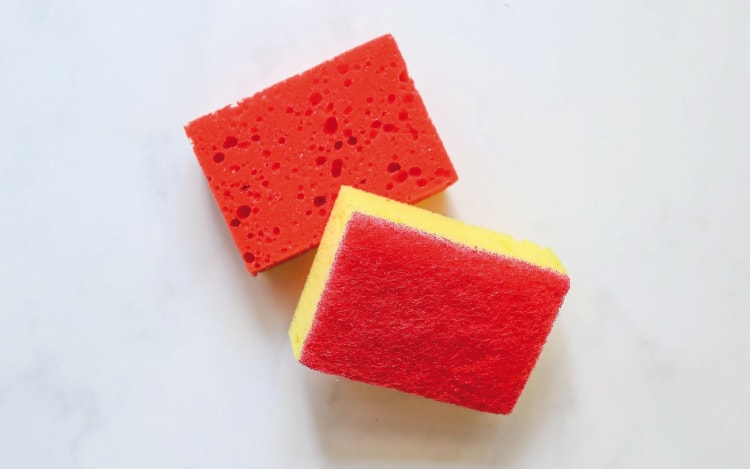
Metody spieniania w procesie wytłaczania tworzywa
Przykład spieniania lotnymi cieczami
Jako środki spieniające stosowane są węglowodory, które są łatwopalne i dlatego podczas procesu należy stosować regulacje ogniowe. Następuje tu rozpuszczenie lotnego węglowodoru w polistyrenie i wytworzenie oraz formowanie perełek EPS, które obejmuje wstępną ekspansję, stabilizację perełek oraz właściwe formowanie - perełki po umieszczeniu w formie są podgrzewane, po czym następuje ekspansja do finalnego kształtu.
Zaletą tej metody jest m.in. możliwość otrzymania produktu o bardzo małej gęstości i niskich kosztach, ponadto istnieje opcja wykonania małych i dużych profili, a koszty formy plus innych narzędzi z aluminium są umiarkowane. Do wad zaliczyć można np. trudności w otrzymywaniu detali o cienkich ściankach i dobrej powierzchni; dodatkowo wybór żywic jest ograniczony i występuje konieczność wprowadzenia w formy pary.