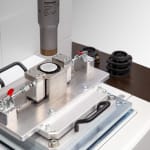
W celu uszczelnienia membrany w systemie odgazowywania awaryjnego firma KACO poszukiwała precyzyjnego i szybkiego procesu łączenia. Dzięki ścisłej współpracy firma Herrmann Ultraschall była w stanie nie tylko opracować idealny proces spawania dla tych specyfikacji, ale także zidentyfikować dalsze obszary zastosowań technologii ultradźwiękowej, dzięki czemu produkcja systemu stała się jeszcze bardziej wydajna.
Jednym z głównych elementów systemu odgazowywania awaryjnego akumulatorów firmy KACO jest cienka membrana wykonana z politetrafluoroetylenu (PTFE), która zapewnia niezbędne wyrównanie ciśnienia. W ramach wspólnego projektu spawalniczego z firmą Herrmann pierwszym zadaniem było połączenie tego wrażliwego komponentu z plastikową obudową.
Wyzwanie: pomimo małej masy i niewielkiej krzywizny membrana musi być zamontowana dokładnie na środku obudowy. Ponieważ wszystkie elementy konstrukcji są do siebie precyzyjnie dopasowane, niewłaściwe umieszczenie membrany może pogorszyć jej funkcjonalność w systemie. Jako że jest to aplikacja o krytycznym znaczeniu dla bezpieczeństwa pojazdów zasilanych przy pomocy baterii, jej prawidłowe działanie musi być zagwarantowane przez cały czas.
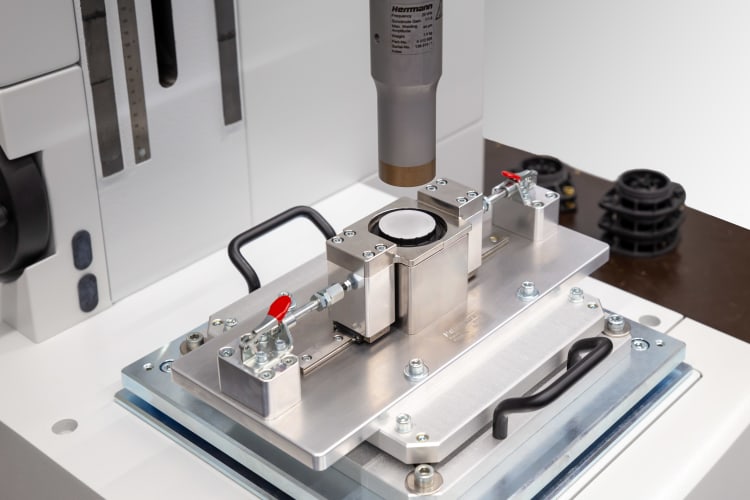
Poszukiwana technologia czystego łączenia
Z różnych powodów firma KACO zrezygnowała ze zwykłej metody łączenia membran z plastikową obudową. Stało się oczywiste, że proces ten utrudniłby dokładne wyśrodkowanie membran z powodu deformacji. Ponadto utwardzanie kleju spowodowałoby wydłużenie czasu produkcji, a chemikalia mogłyby mieć negatywny wpływ na oddychalność cienkiej membrany.
Dlatego też firma KACO zdecydowała się polegać na ultradźwiękach jako czystej i szybkiej technologii łączenia, która pozwala również na oszczędność energii i zasobów w porównaniu z procesem klejenia. W bardzo krótkim czasie od złożenia zapytania firma Herrmann była w stanie wykazać w pierwszych podstawowych testach, że membrana może być niezawodnie i trwale połączona z plastikową obudową za pomocą ultradźwięków. Ze względu na nacisk sonotrody na membranę podczas procesu zgrzewania jej niewielkie zakrzywienie nie stanowiło problemu. Bez konieczności stosowania dodatkowych środków łączących oryginalne właściwości materiałowe cienkiej membrany są zachowane nawet po zgrzewaniu.
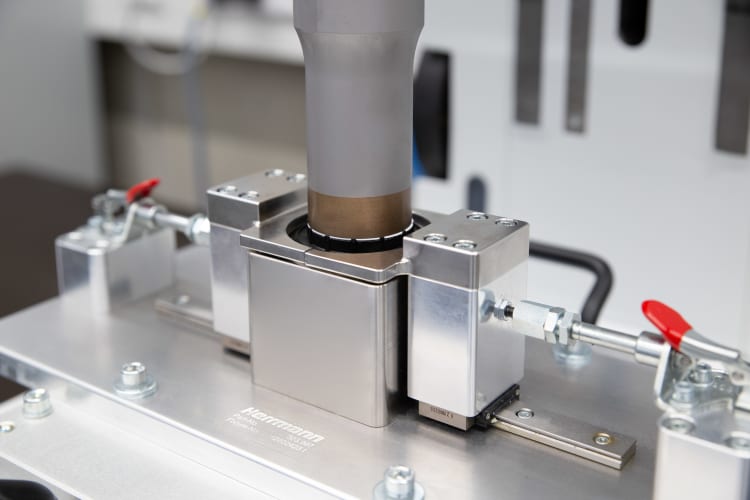
Indywidualność, pneumatyka, bezpieczeństwo
Aby zapewnić dokładne wyśrodkowanie elementu łączonego w aplikacji, opracowano niestandardowe mocowanie i zintegrowano je z uchwytem przedmiotu obrabianego. Ułatwia to operatorowi na ręcznym stanowisku pracy optymalne ustawienie membrany do procesu zgrzewania i zapobiega ślizganiu się elementu łączonego. Podczas testów spawalniczych uchwyt ten był nadal obsługiwany ręcznie, ale do masowej produkcji ma być obsługiwany automatycznie za pomocą pneumatyki.
Połączenie takiego niestandardowego mocowania i dostosowania parametrów zgrzewania zapewniło dokładne uszczelnienie membrany. Jakość wyników spawania została oceniona na zdjęciach przekrojowych. Wyniki wstępnych testów spawalniczych zostały potwierdzone: pod mikroskopem potwierdzono uzyskanie szczelnego połączenia między membraną a plastikową obudową, w pełni spełniającego wymagania klienta.
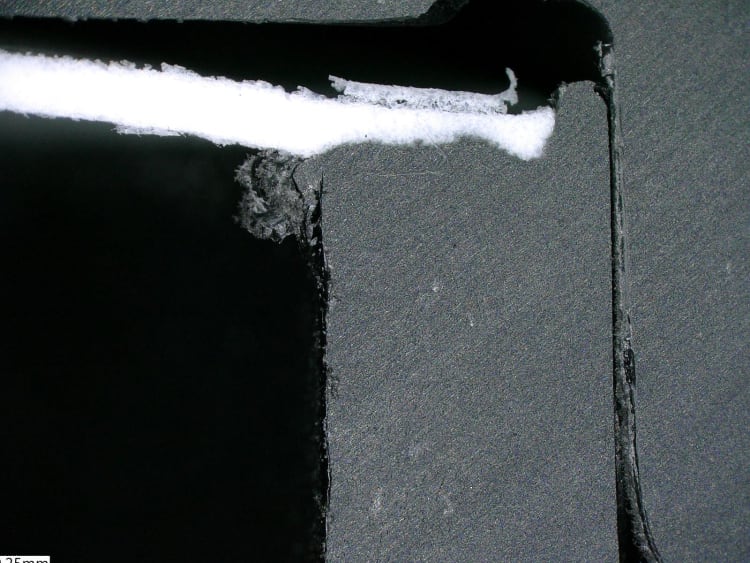