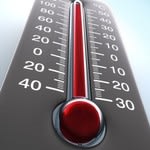
Najlepsza temperatura formy pod kątem długookresowych właściwości produkowanych detali, to temperatura nieznacznie niższa od temperatury krystalizacji tworzywa, np. 155 st. C. Taka temperatura umożliwi krystalizację polimeru w optymalnych warunkach oraz wyeliminuje wszelkie ryzyko związane z rekrystalizacją, czyli skurczem poprodukcyjnym. Oczywiście ustawienie temperatury formy na takim poziomie jest niemożliwe z ekonomicznego punktu widzenia, ponieważ czas krystalizacji zostałby przedłużony prawie w nieskończoność w porównaniu z czasem cyklu.
W praktyce stosuje się więc niższą temperaturę formy, co prowadzi do krótszego czasu krystalizacji, a tym samym do krótszego czasu cyklu, mniejszego skurczu pierwotnego, ale większego skurczu wtórnego - szczególnie wtedy, gdy detal jest później wystawiony na działanie podwyższonej temperatury. Dlatego też trzeba znaleźć rozwiązanie kompromisowe w zależności od stosowanej temperatury form oraz wymaganej tolerancji wymiarowej produkowanego detalu i to zarówno pod kątem jego długoterminowej, jak i krótkoterminowej eksploatacji.
W przypadku standardowych gatunków tworzyw temperatura formy w zakresie 80-100 st. C jest dobrym kompromisem jeśli chodzi o normalne zastosowania detali. Taka temperatura oznacza stosunkowo krótki czas krystalizacji, duży skurcz pierwotny i jednocześnie niewielki skurcz wtórny. Wyższa temperatura formy prowadzi do większego skurczu pierwotnego, dłuższego czasu cyklu, ale przy tym niższego skurczu wtórnego. Jest ona szczególnie zalecana przy produkcji detali o wysokiej precyzji, które są wykorzystywane w wysokiej temperaturze. Z kolei niższa temperatura formy prowadzi do osiągnięcia krótszych czasów cyklu, mniejszego skurczu pierwotnego, ale też do znacznie wyższego skurczu wtórnego, co jest przyczyną powstawania naprężeń i odkształceń.
Dla tworzyw wzmocnionych dopuszczalne jest użycie niższej temperatury formy ok. 50 st. C. bez zagrożenia osłabienia długoterminowych parametrów eksploatacyjnych detali.
Jeszcze dwie uwagi. Choć stosuje się określenie „temperatura formy”, to ważnym parametrem jest także temperatura powierzchni ścian gniazda. Przy operacjach szybkiego cyklu może zajść konieczność zastosowania chłodziwa formy o niższej temperaturze, tak aby utrzymać temperaturę powierzchni ścian gniazda formy w zalecanym zakresie. Dla bardzo krótkich cykli lub do chłodzenia kołków formujących otwory w wyprasce, jak również do innych sekcji formy, które mają tendencje do nadmiernego rozgrzewania się, bardzo często stosuje się zimną wodę.
Druga uwaga dotyczy chłodziwa. Najczęstszym typem stosowanym obecnie są zamknięte obwody chłodzące. Chłodziwa do obwodów zamkniętych muszą być odporne na zamarzanie, ciśnienie oraz podciśnienie. Nie mogą zostawiać osadu w obwodzie, ani też korodować kanałów chłodzących i rurek.
Początkowo wymiana cieplna bywa mniej wydajna niż w przypadku zastosowania wody, co wynika z faktu, że płyn jest bardziej lepki z uwagi na lepkość glikolu. Potrzebna jest tu większa energia do przepływu turbulentnego. Jednak przy dłuższym zastosowaniu płyn jest bardziej efektywnym rozwiązaniem z uwagi na brak korozji, brak osadu, mniejszą korozję wynikająca z kawitacji.
W przypadku chłodziwa w otwartych kolumnach chłodzących trzeba zastosować obróbkę chemiczną, aby zapobiec rozwojowi organizmów mikrobiologicznych, które powodowałyby choroby oraz problemy z oddychaniem.
Wykorzystano materiały firmy DuPont.