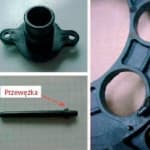
Dla przykładu stosunkowo łatwa do rozpoznania jest szorstka, pofałdowana powierzchnia wyrobu. Powstaje ona wtedy, gdy przekrój przewężki jest zbyt mały. Przewężka krzepnie w takich sytuacjach przed upływem niezbędnego czasu docisku. Zachodzący podczas chłodzenia skurcz nie zostaje skompensowany. Środkiem zaradczym jest tu powiększenie przekroju przewężki. Zgodnie z ogólną zasadą kanał wlewowy i otwór dyszy maszyny nie powinny być nigdy mniejsze od grubości ścianki wyrobu przy przewężce.
Z kolei w przypadku form wielokrotnych nieodzowne jest zbadanie napełniania (metoda niedolewów) i dokładne sprawdzenie wyprasek z każdego gniazda. Jeśli wypraski z poszczególnych gniazd nie są ukształtowane identycznie, oznacza to, że konieczne jest zbalansowanie rozdzielacza, gdyż albo różne są straty ciśnienia, albo długości dróg dopływu do poszczególnych gniazd.
W celu zapewnienia równomiernego napełniania trzeba zbalansować rozdzielacz naturalnie lub reologicznie. W pierwszym przypadku - rozwiązanie konstrukcyjne - przekroje kanałów i drogi płynięcia do każdego z gniazd są jednakowe. W drugim przypadku przy różnych drogach płynięcia przekroje kanałów muszą być obliczone tak, by straty ciśnienia na drogach płynięcia były identyczne dla wszystkich gniazd. Jeśli jednak rozdzielacz został zaprojektowany prawidłowo, to wówczas przyczyną niejednorodnego napełniania gniazd może być nierównomierny rozkład temperatur.
Kolejną widoczną wadą są przypalenia na końcu drogi płynięcia lub w miejscach łączenia się dwóch czół stopu, tzn. na liniach łączenia.
Przyczyną tej wady jest w obu wypadkach niedostateczne odpowietrzanie formy. Powietrze zamknięte przed czołem stopu bardzo szybko spręża się. Przy sprężaniu ogrzewa się i przypala tworzywo. Skutecznym środkiem zaradczym jest tu zastosowanie kanałów odpowietrzających - przekrój tych kanałów zależy od lepkości materiału - lub wstawek ze spieków metalowych. Niekiedy wadę tę można częściowo wyeliminować korygując punkt przełączania i redukując prędkość wtrysku przy końcu drogi płynięcia.
Widoczne rysy (pęknięcia) na wypraskach wtryskowych mogą też powstawać w sytuacjach, gdy zapraski nie są pozycjonowane. To z kolei pociąga za sobą zmiany przekroju przepływu i powstawanie linii łączenia. Przyczyną powstawania rys może być również działanie karbu na ostrych krawędziach w formie lub na wykrawanych zapraskach. Dlatego też zaleca się zaokrąglanie krawędzi w formie i stosowanie zaprasek wykrawanych bez gratu. Zapewnienie niezmiennej pozycji wkładek zapobiega ich obracaniu się aż do pozycji niepożądanej.