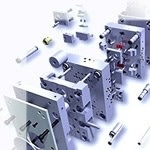
Ze względu na duży wpływ temperatury formy na stopień krystalizacji, a tym samym i własności mechaniczne detali wykonanych z tworzyw krystalicznych, układ chłodzenia powinien być zaprojektowany z dużą starannością. Ma to na celu zapewnienie jednakowej temperatury ścian gniazda formy.
Formy pracujące bez jakiegokolwiek układu chłodzenia osiągają w końcu stan równowagi, gdyż ciepło doprowadzane do nich wraz z płynnym polimerem zrównuje się z ciepłem odprowadzanym poprzez promieniowanie, przewodzenie i konwekcję.
Temperatura formy przy optymalnym cyklu roboczym będzie mieć dużą wartość pośrednią pomiędzy bardzo wysoką, ułatwiającą napełnianie i sprzyjającą uzyskaniu dobrej jakości powierzchni a bardzo niską, przyspieszającą przechodzenie tworzywa w stan stały oraz ułatwiającą uwalnianie wyprasek.
Najlepszym rozwiązaniem w takim przypadku byłoby umieszczenie kanałów chłodzących w tych obszarach, które wymagają największego przepływu ciepła. Kanały takie powinny być oddalone od gniazda formy o co najmniej jedną średnicę kanału.
W celu uzyskania jednakowej temperatury całej formy różnica temperatur pomiędzy dopływem a odpływem cieczy chłodzącej (wody, oleju) powinna być jak najmniejsza, maksymalnie dochodzić 5 st. C. Szybkość przepływu chłodziwa przez kanały powinna być z kolei na tyle duża, by małe jej fluktuacje nie zmieniały temperatury formy. Jeżeli wymagana jest wysoka precyzja formowania, to gniazda powinny być chłodzone w układzie równoległym, który zapewnia mniejsze zróżnicowanie temperatur niż układ szeregowy.
Projektant formy podczas wymiarowania kanałów musi zrealizować dwa przeciwstawne zadania. Po pierwsze przekrój kanału musi być na tyle duży, by mieć pewność, że natężenie przepływu chłodziwa jest wystarczające do odprowadzenia ciepła. Po drugie przekrój kanału musi być na tyle mały, by przepływ w nim miał charakter turbulentny, gdyż współczynnik przejmowania ciepła w takich warunkach jest największy.