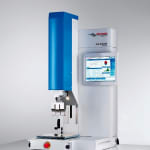
Przy produkcji sprzętu gospodarstwa domowego łączonych jest wiele detali z tworzyw sztucznych, na przykład panel wyświetlacza w części obsługowej pralki albo dwie połówki wirnika napędzającego – by wymienić tu tylko kilka przykładów. W branży motoryzacyjnej występuje ponad 100 zastosowań ultradźwięków, od zestawu wskaźników po puszkę podciśnieniową w bloku cylindrów.
Przy użyciu ultradźwięków można zgrzewać, nitować, poddawać obróbce plastycznej, zatapiać, oddzielać, a nawet wytłaczać termoplasty. Bez używania substancji dodatkowych, wskutek poddania działaniu ultradźwięków w ciągu milisekund uzyskuje się wysoce wytrzymałe, gazo- i wodoszczelne połączenie o korzystnych właściwościach wizualnych. Najważniejszym warunkiem wstępnym jest tutaj właściwe pod względem tworzywa i techniki zaprojektowanie elementu konstrukcyjnego w strefie łączenia, a także na powierzchniach przylegania narzędzia zgrzewającego (sonotrody).
Wysoka technologia maszyn umożliwia zachowanie powtarzalności zgrzewów również w przypadku, gdy detale wykazują różnice tolerancji, spowodowane np. różnym stopniem wysuszenia materiału przed wtryskiem.
Ze względu na niskie zapotrzebowanie na energię elementy wtryskowe są w niewielkim stopniu obciążane termicznie. Twarde, amorficzne tworzywa sztuczne, jak PC, PS, SAN, ABS i PMMA wykazują bardzo korzystne właściwości pod względem przenoszenia energii ultradźwięków. Tworzywa częściowo krystaliczne, jak PA, PP, PE i POM najlepiej jest zgrzewać w bezpośrednim sąsiedztwie sonotrody. Zgrzane detale można od razu poddawać obróbce, dzięki czemu ultradźwięki można bez problemu zintegrować na liniach zautomatyzowanych.