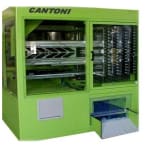
Opracowany przez Włochów system szczególnie mocno nadaje się do produkcji preform do butelek o pojemności 5, 8, 10 i 20 litrów. Cały cykl wtrysku i chłodzenia trwa w opracowanym przez Cantoni systemie 75 sekund w przypadku preform o masie 400 g - 7 sekund zajmuje wtrysk, 35 sekund utrzymanie, 20 sekund chłodzenie, a pozostały czas wypełnia otwieranie, zamykanie, wyrzut. W odniesieniu do preform o ciężarze 700 gram cykl wtrysku i chłodzenia zajmuje więcej, bo 85 sekund.
Najbardziej charakterystycznym wyróżnikiem systemu stworzonego przez Cartoni jest fakt, że przy produkcji preform PET nie jest wymagane stosowanie robota do przekładania, ponieważ preformy są chłodzone bezpośrednio na stemplach wtryskowych usytuowanych na stanowiskach na końcu formy.
Forma z kolei składa się z dwóch zestawów rdzeni i tylu samo stanowisk chłodzących. Połówka ruchoma ze stemplami porusza się wzdłuż osi X i tym samym ruch ten umożliwia wtrysk tworzywa PET na jeden z dwóch zestawów rdzeni, a przy tym równocześnie chłodzenie przez tzw. karuzele preform poprzednio już uformowanych na drugim zestawie.
To na czym dokładnie polega istota tej technologii można przybliżyć biorąc za wzór formę z 16+16 gniazdami do wytwarzania preform o masie 36 g.
Przede wszystkim nieruchoma połówka form posiada 16 gniazd, a także pierwsze urządzenie chłodzące z 16 stanowiskami aluminiowymi z jednej strony oraz drugie urządzenie chłodzące z taką samą liczbą stanowisk chłodzących tego samego rodzaju, tyle że z przeciwnej strony. Pomiędzy tymi urządzeniami ustawionych jest 16 matryc. Ponadto dwa zestawy, z których każdy ma po 16 rdzeni, umieszczone są na ruchomej połówce formy.
Następuje zamknięcie formy. W tym momencie, gdy forma jest zamykana, pierwszy zestaw rdzeni wsuwa się w matryce i odbywa się wtrysk. Przy otwieraniu formy rdzenie z preformami wysuwają się i ruchoma połówka formy przesuwa się wzdłuż osi X. W tym momencie forma ponownie się zamyka i pierwszy zestaw rdzeni wsuwa się w pierwsze stanowisko chłodzące, podczas gdy drugi zestaw rdzeni wsuwa się w matryce by dokonać nowego wtrysku.
Tym samym więc chłodzenie preform uformowanych na pierwszym zestawie rdzeni oraz wtrysk dokonywany na drugim zestawie rdzeni wewnątrz matryc odbywają się w tym samym czasie. Gdy forma ponownie się otwiera, to pierwszy zestaw wyrzuca schłodzone preformy, a ruchoma połówka formy przesuwa się wzdłuż osi X, ale w kierunku przeciwnym do poprzedniego ruchu.
Na tym jednak jeszcze nie koniec całego procesu. Forma ponownie jest zamykana i drugi zestaw rdzeni wsuwa się w stanowisko chłodzenia, podczas gdy pierwszy zestaw wsuwa się w matryce. W tym czasie preformy uformowane na drugim zestawie są chłodzone, a wtrysk następuje na pierwszym zestawie wewnątrz matryc. Gdy forma otwiera się już po raz ostatni, wówczas drugi zestaw rdzeni wyrzuca preformy , a ruchoma połówka formy przesuwa się wzdłuż osi X w kierunku takim jak podczas pierwszego ruchu.
W tym konkretnym przypadku system może osiągnąć wydajność pozwalającą na wyprodukowanie 3900 preform na godzinę. Grubość ścianek każdej z preform to 3,65 mm, co w przypadku dużych opakowań o pojemności 5-20 litrów jest wynikiem bardzo dobrym, oznaczającym osiągnięcie pewnych oszczędności materiałowych. Ponadto stworzona w oparciu o nowa technologię Cantoni preforma ulega mniejszym odkształceniom ponieważ jest chłodzona bezpośrednio na stemplu, który ją stabilizuje.