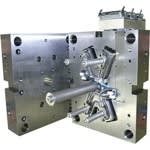
Od prawidłowego wyboru i właściwego zainstalowania systemu gorących kanałów zależy działanie formy i jakość wypraski przy przetwórstwie wtryskowym częściowo krystalicznych termoplastów technicznych. Formy z gorącymi kanałami są bardzo złożonymi układami termicznymi. Bardzo ważne jest nawiązanie kontaktu z producentem form z gorącymi kanałami, gdyż powinien on dopomóc w wyborze rozdzielacza i dyszy najbardziej odpowiednich dla przetwarzanego tworzywa.
Przy projektowaniu formy z gorącymi kanałami do przetwórstwa częściowo krystalicznego PET i PBT mogą być pomocne pewne reguły podstawowe. Dla przykładu konieczne są rozdzielacze zbalansowane w sposób naturalny (konstrukcyjnie) lub obliczeniowo (reologicznie). Przez balansowanie reologiczne, czyli dopasowywanie dyszy lub wielkości przewężki można optymalizować czas napełniania lub ciśnienie docisku. Przy czym te dwa rodzaje balansowania nawzajem się wykluczają.
Bezpośredniego wtrysku w wypraskę należy unikać natomiast przy małych ciężarach wtrysku lub długich czasach cyklu (łączny czas przebywania powyżej 10 minut); przy produkcji wyrobów przezroczystych, ponieważ w okolicy przewężki mogą powstawać wady powierzchniowe; przy produkcji wyrobów, którym stawiane są duże wymagania wytrzymałościowe, ponieważ zawsze istnieje możliwość przedostania się zimnego lub niejednorodnego korka z wierzchołka dyszy do obszaru krytycznego pod względem mechanicznym. Bezpośredniego wtrysku w wypraskę należy unikać również jeśli niedopuszczalne są widoczne ślady pozostające na powierzchni po zerwaniu przewężki.
Rozdzielacze i dysze muszą być zaprojektowane optymalnie z punktu widzenia warunków przepływu, tak by nie powstawały strefy zalegania. Ogrzewane od zewnątrz kanały rozdzielcze są korzystniejsze od kanałów ogrzewanych od wewnątrz, ponieważ umożliwiają lepsze – z punktu widzenia warunków przepływu - zaprojektowanie rozgałęzień, a przepływające przez nie tworzywo jest w mniejszym stopniu narażone na ścinanie.
Bezwzględnie konieczna jest optymalna równowaga termiczna. W formach z gorącymi kanałami niedopuszczalne są różnice temperatur. Dlatego też bardzo ważna jest prawidłowe zestawienie poszczególnych elementów (rozdzielacze, dysze, grzejniki), regulacja temperatury oraz sama budowa (optymalna izolacja termiczna pomiędzy gorącym kanałem a formą).
Należy unikać stosowania dyszy z komorą wstępną. W dyszach tego typu tworzywo wpływa do przestrzeni pomiędzy wierzchołkiem dyszy a powierzchnią formy, optymalizując tym samym termiczną izolację wierzchołka dyszy. W przypadku tworzyw częściowo krystalicznych, takich jak PBT i PET, temperatura tworzywa w szczelinie najczęściej przekracza temperaturę krzepnięcia tego tworzywa. Tworzywo ulega degradacji termicznej. Może to być przyczyną powstawania wad powierzchniowych w nieregularnych odstępach czasu.
Dysze ze swobodnym przepływem są korzystniejsze niż dysze z tzw. torpedą, jeśli na wyrobie dopuszczalny jest ślad w okolicy przewężki. Do przetwórstwa typów wzmocnionych należy stosować materiały o dużej odporności na ścieranie lub poddane specjalnym obróbkom. Dotyczy to zwłaszcza wierzchołka dyszy, ponieważ tam ścinanie jest największe. Zastosowanie twardych spieków gwarantuje znaczne zwiększenie trwałości wierzchołka dyszy. Wierzchołki dyszy powinny być wymienne. Ułatwia to kontrolę zużycia i obniża koszty ewentualnej modyfikacji.
Nagrzewając formę z gorącymi kanałami, w której znajduje się tworzywo, należy pamiętać , że najpierw powinna być ogrzana do temperatury o ok. 20st. C niższej od temperatury topnienia tych tworzyw, a następnie do 210 - 230 st. C. Tę temperaturę należy utrzymywać przez co najmniej 30 minut. Dopiero potem można ją podwyższyć do temperatury zadanej, co zapewnia uzyskanie korzystnej równowagi termicznej.
Nowoczesne regulatory zezwalają na automatyczny przebieg rozruchu według krzywej wysterowania sygnału. Jeżeli przypuszcza się, że w gorącym kanale powstała strefa zalegania, to tworzywo w cylindrze należy wymienić na tworzywo o innej barwie i to nowe tworzywo przetwarzać przez 10 minut. Następnie zatrzymać maszynę, zdemontować system gorących kanałów/dyszę i sprawdzić, w których miejscach widoczne są jeszcze ślady pierwszego tworzywa.