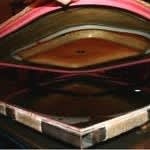
Technologia LRTM jest wykorzystywana głównie w konstruowaniu sprzętu wodnego, głównie łodzi. Jednak możliwości jej zastosowania są liczniejsze. W grę wchodzą np. elementy karoserii, przyczepy, samoloty.
Technika jest rozwinięciem klasycznej technologii RTM, pod którym to skrótem kryje się przetłoczone formowanie żywicy. Standardowa metoda wtryskiwania została rozszerzona o podciśnienie. Dzięki takiemu połączeniu realne stało się używanie dużo niższego ciśnienia (0,4 - 1 bara), co z kolei wpływa na minimalizację kosztów produkcji z racji budowy mniej masywnych form.
To ważne, bowiem koszty form LRTM stanowią przeciętnie połowę ceny odpowiednich form RTM. Niestety coś za coś. Formy te umożliwiają, w najlepszym razie, produkcję w tempie dwukrotnie niższym niż ma to miejsce przypadku RTM. Niemniej jednak proces stanowi atrakcyjny sposób nabywania doświadczenia produkcji w formach zamkniętych.
LRTM rozpoczyna się od przygotowania form. W tym przypadku są to dwie formy. Należy nałożyć na nie kilka warstw separatora i wypolerować w celu uzyskania gładkiej i równej powierzchni. Na tak przygotowane formy nakłada się żelkot, który spełnia rolę ochronną oraz wizerunkową. Nałożenia można dokonać w sposób ręczny lub natryskowy. Kolejnym etapem jest dopasowanie zbrojenia, z którego ma być zbudowany laminat. Przy produkcji wielkoseryjnej wkłada się tzw. preformy z materiału wzmacniającego. Materiał wzmacniający na bazie włókien szklanych, węglowych bądź aramidowych musi mieć strukturę umożliwiającą łatwy przepływ żywicy. Jest to konieczne, aby osiągnąć całkowite jego przesycenie w krótkim czasie.
Kolejnym krokiem jest zamknięcie formy i wtłoczenie spoiwa poprzez pompę. Można to wykonać na dwa sposoby. Po pierwsze wtryskiwać spoiwo w środkowej części formy, a podciśnienie aplikować po obwodzie formy. W drugiej wersji można podawać spoiwo do kanalika na obwodzie formy, a podciśnienie aplikować w centralnej części formy. Jako spoiwa stosuje się żywice poliestrowe, winyloestrowe, epoksydowe, metakrylowe. Wybór zależy od cech laminatu.
Ostatnim etapem omawianego rozwiązania jest rozformowanie i wyciągnięcie gotowego detalu.
Ważną cechą procesu LRTM jest fakt, że szybkości napływu żywicy nie może być w nim podniesiona powyżej poziomu optymalnego. Jest to niemożliwe, ponieważ zalecana konstrukcja formy LRTM oraz ciśnienie atmosferyczne zamknięcia formy, ograniczają ogólne ciśnienie wewnątrz formy.
Zalety i korzyści ze stosowania metody LRTM są wielorakie. Przede wszystkim jest to możliwość osiągnięcia dwóch mechanicznie wykończonych i gładkich stron formowanej części. W trakcie operacji formowania nie dochodzi do emisji zanieczyszczeń. Uzyskuje się wysokiej jakości części warstwowe bez pustych miejsc. Możliwe jest też formowanie z powłoką żelową lub bez niej. Brak jest konieczności zużycia przez formę innych materiałów poza żywicą i szkłem użytymi do produkcji. Wreszcie odpady żywicy sięgają pułapu dochodzącego ledwie do 5 proc.