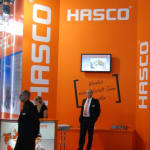
Firma przedstawiła przypadek spółki Akson, będącej jej klientem. Firma te poszukiwała rozwiązań konstrukcyjnych formy dla produkcji zakrętek spychanych z plombą dla opakowań. Zwykle dla większości detali tego rodzaju najpopularniejszym rozwiązaniem było rozformowanie gwintu przy pomocy obracających się elementów i rozformowanie plomby przy pomocy suwaków.
Ponieważ jednak wymagania stawiane formom wielogniazdowym dla przemysłu opakowaniowego z roku na rok stają się coraz bardziej wymagające, to wzrasta zapotrzebowanie na formy wielogniazdowe zaprojektowane w tak zwarty sposób jak to tylko możliwe. Ma to na celu redukcję ich rozmiarów. Rozwiązanie takie jest możliwe w przypadku form do produkcji zamknięć, które nie posiadają plomb. Jednak kiedy taka plomba istnieje to sytuacja ulega zmianie. Konieczne staje się zastosowanie suwaków aby ją rozformować, a to z kolei skutkuje zwiększeniem wymiarów formy. Zwykle takie formy posiadają gniazda w układzie co najmniej dwóch rzędów.
Stąd koniecznością stało się porównanie technologia rdzeni do formowania podcięć z mechanizmem wykręcającym. Porównanie dwóch form próbnych odbywało się dla czasu cyklu, pracochłonności oraz kosztów. W pierwszej formie zastosowano właśnie technologię rdzeni do formowania podcięć, druga została natomiast zaprojektowana z mechanizmem wykręcającym.
Dla celów projektu zostały wybrane dwa detale w postaci zakrętek. Ze względu na różny sposób rozformowania, zakrętki te nie były identyczne, chociaż posiadały podobne cechy konstrukcyjne: plomby, zbliżony profil gwintu, zaczepy na plombach, sposób łączenia plomby z korpusem zakrętki.
Pierwsza zakrętka miała 28 mm średnicy, ważyła 2,9 g, wykonana była z tworzywa HDPE, natomiast formowanie odbywało się za pomocą rdzeni do formowania podcięć Hasco. Druga zakrętka miała średnicę 24 mm, ważyła 2,8 g, także była z tworzywa HDPE, a formowano ją przy zastosowaniu mechanizmu wykręcającego.
Jeśli chodzi o charakterystykę użytych w testach form, to ich parametry technologiczne zoptymalizowano tak, by osiągnąć jak najlepszy czas cyklu przy zachowaniu dobrej jakości zakrętek z obu form. W pierwszej formie zastosowano mechanizm wypychania dwustopniowego, w drugiej zaś siłowniki hydrauliczne.
Już na początku testów można było rozpoznać różnice między obiema formami. Forma z rdzeniami do formowania podcięć miała zwartą budowę, pracowała płynnie i cicho oraz bez problemów podczas uruchomienia. Forma z siłownikiem hydraulicznym byłą większa. Trudniej, z uwagi na wymiary, było ją zamontować na wtryskarce. Z kolei forma z mechanizmem wykręcającym z uwagi na suwaki wymagała uważnego uruchomienia produkcji.
W testach okazało się, że technologia rdzeni formowania podcięć daje większe korzyści w stosunku do technologii z mechanizmem wykręcającym. Ze względu na precyzyjny i płynny ruch formy bez suwaków możliwe było znaczne zredukowanie czasu wypychania, docisku, chłodzenia oraz otwarcia i zamknięcia. Sama przewaga w czasie cyklu wyniosła dla formy z rdzeniami do formowania podcięć blisko 25 proc.
Formy zostały przeanalizowane pod wieloma względami ważnymi dla licznych narzędziowni. Okazało się, że forma z rdzeniami do formowania podcięć daje większe korzyści związane z czasem realizacji, a w szczególności z czasem produkcji elementów gniazda, czasem poświęconym na obróbkę płyt oraz czasem projektowania.
Czas wytworzenia elementów gniazda dla formy z rdzeniami do formowania podcięć był krótszy o 35 proc. niż w przypadku formy z mechanizmem wykręcającym. Zwarta konstrukcja rdzeni do formowania podcięć i brak suwaków pomogły w osiągnięciu mniejszych wymiarów podstawy formy i zaoszczędzeniu czasu potrzebnego na obróbkę. Czas produkcji dla formy z rdzeniami do formowania podcięć był o 45 proc. krótszy niż dla formy z mechanizmem wykręcającym. Konstrukcja tej formy z wymagała też mniejszej ilości płyt i komponentów.
Całkowity koszt produkcji formy z rdzeniami do formowania podcięć, włączając w to montaż, był krótszy o 45 proc.
Testy pokazały, że technologia rdzeni do formowania podcięć jest szczególnie użyteczna zastosowaniach dla form wielogniazdowych z gwintami i podcięciami.