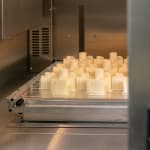
W przypadku produkcji masowej technologia formowania wtryskowego wydaje się najlepszym wyborem. Jednak co w przypadku produkcji o mniejszych wolumenach? Wybór form wtryskowych nie jest już tak oczywisty. Artykuł pomoże w odpowiedzi na pytanie, czy warto zastąpić technologię formowania wtryskowego drukiem 3D i jakie oszczędności może przynieść firmie implementacja technologii addytywnej.
Z czym wiążę się inwestycja w technologie formowania wtryskowego?
Zanim otrzymamy konkretną część wykonaną w technologii wtrysku musimy stworzyć jej formę. Firma, która specjalizuje się w produkcji więcej niż jednego elementu będzie zmuszona do tworzenia formy do każdego z nich, co znacznie wpłynie na wzrost kosztów.
Samo wytworzenie formy wtryskowej, zakładając średni stopień skomplikowania, może stanowić koszt od 20, do nawet 50 tysięcy złotych. Dokładny koszt wykonania formy uzależniony jest oczywiście od stopnia zaawansowania geometrii oraz wymiarów. Kolejnym wydatkiem będzie zakup materiału, z którego wykonamy element końcowy. Znając powyższe wartości oraz cenę naszego produktu możemy obliczyć, jaki wolumen należy sprzedać, by inwestycja w technologię wtrysku była dla nas opłacalna.
Warto również dodać, że kolejnym dość istotnym czynnikiem, który wpływa na tak wysoki koszt wytworzenia formy, jest czas realizacji zlecenia. Przyjmuje się, że całkowity czas realizacji może wynieść nawet od 2 do 4 miesięcy.

Korzyści płynące z druku 3D
Technologia druku 3D nie wymaga tworzenia dodatkowych form, a zakup drukarki jest jednorazowy. Jeśli firma nie chce inwestować w zakup drukarki 3D, może skorzystać z usług firm świadczących druk 3D na zamówienie.
Czas realizacji wydruku w technologii addytywnej również jest nieporównywalnie krótszy od czasu potrzebnego na wytworzenie formy wtryskowej. Czas wytworzenia elementu wydrukowanego na drukarce 3D liczymy w godzinach, jednak ostatecznie na długość procesu druku wpływa rozmiar, wybór materiału jak i drukarki. Dlatego warto rozpocząć przygodę z technologią addytywną od skorzystania z usług druku 3D.
Centra produkcji addytywnej realizują projekty dla firm, dostarczając narzędzia produkcyjne, części zamienne i końcowe oraz projektując funkcjonalne prototypy. Zespół doświadczonych inżynierów kontroluje proces na każdym etapie, dobiera odpowiednie materiały i parametry druku.
Jeden z większych parków maszynowych drukarek 3D znajduje się w Przyszowicach k/Gliwic, w firmie 3DGence, gdzie do dyspozycji klienta jest ponad 50 przemysłowych systemów druku 3D. W połączeniu z dwuzmianową pracą zakładu otrzymujemy gwarancję jak najszybszego czasu realizacji zamówionego elementu.
Takie rozwiązanie sprawdza się zwłaszcza przy niskonakładowej produkcji seryjnej oraz prototypowaniu. Oczywiście w przypadku kilkutysięcznych wolumenów w pewnym momencie czas pracy drukarki 3D przewyższy czas potrzebny na przygotowanie wtryskarki. Za drukiem 3D przemawiają jednak jeszcze inne argumenty.
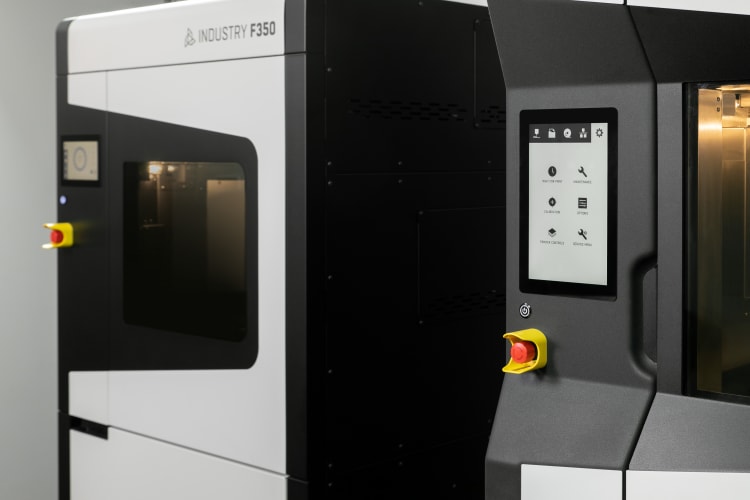
Poprawki w projekcie to często tworzenie nowej formy wtryskowej
Zagrożenia wynikające z wprowadzania poprawek w kolejnych iteracjach produktu to między innymi dodatkowe koszty i czas potrzebny na udoskonalenie formy wtryskowej. W praktyce wygląda to tak, że bardzo często trzeba stworzyć ją od nowa. W drukarce 3D nie trzeba niczego zmieniać. Wystarczy w odpowiednim programie wygenerować na nowo plik do maszyny na podstawie zmienionego modelu 3D.
Otwiera to ogrom możliwości w prototypowaniu i tworzeniu nowych iteracji produktu. Zamiast tworzyć nowe formy wtryskowe lub budować prototypy w inny sposób, można zlecić wydruk 3D modelu.
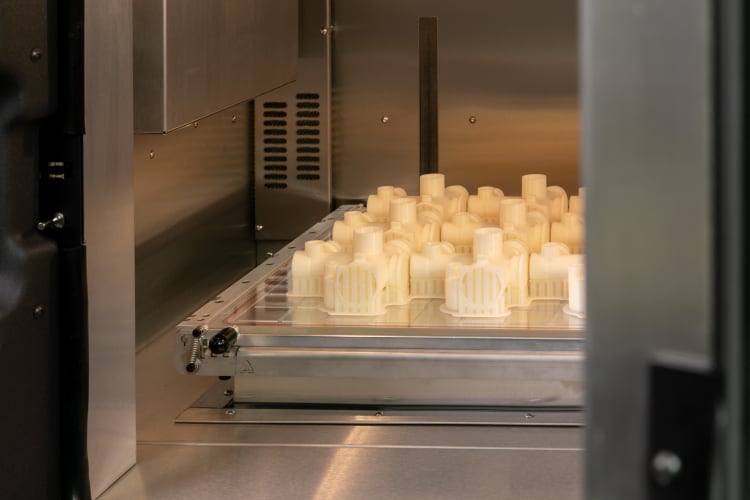
Częstym argumentem przeciwko tworzeniu prototypów za pomocą technologii przyrostowych jest ich niska dokładność. Tak rzeczywiście było, kiedy druk 3D nie był jeszcze rozwiniętą technologią. Obecnie producenci drukarek 3D, oraz firmy świadczące wydruki na zamówienie dysponują chociażby technologią SLA (ang. Stereolitography, czyli utwardzanie płynnej żywicy wiązką lasera), która zapewnia dokładne detale i wysoką precyzję. To idealna metoda do wytwarzania skomplikowanych geometrii.
Inną popularną technologią wykorzystywaną w prototypowaniu jest FFF (ang. Fused filament fabrication), czyli drukowanie przestrzenne za pomocą topionego materiału termoplastycznego. Ta metoda pozwala przede wszystkim zaoszczędzić pieniądze (ceny filamentów zaczynają się już od około 100 zł za kilogram materiału) i doskonale sprawdza się w produkcji niskoseryjnej jeśli firma oferująca wydruki na zamówienie jest w posiadaniu kilkudziesięciu gotowych do pracy maszyn.