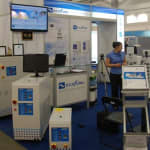
System termowizyjny Ecoflow został już wyróżniony podczas majowych targów Plastpol w Kielcach. Spotkał się tam również z dużym zainteresowaniem ze strony zwiedzających. Zdaniem samych przedstawicieli firmy optymalizacja procesu wtrysku dzięki zastosowaniu kamery termowizyjnej pozwala na szybki pomiar temperatury na całej powierzchni formy. Taka analiza termalna narzędzia umożliwia z kolei określenie węzłów termicznych w gnieździe formy, co dzięki modyfikacjom układu chłodzenia przyczynia się do skrócenia czas cyklu produkcyjnego oraz poprawy jakości produkowanych części. Analiza termiczna pozwala także na optymalizację produkcji, co przynosi korzyści każdemu zakładowi przetwórstwa tworzyw sztucznych.
Warto więc bliżej przyjrzeć się wspomnianemu rozwiązaniu.
Przede wszystkim termowizja odpowiada na kluczowe wymaganie jakim jest obecnie redukcja kosztów produkcji. Zmniejszając czas potrzebny na otwarcie lub zamknięcie formy, ruch wypychaczy czy cykl wtrysku, można z jednej strony zaoszczędzić wielu sekund, z drugiej jednak strony narazić używane narzędzie na uszkodzenie. Tymczasem najwięcej rezerw czasowych ukrytych jest w czasie chłodzenia. Wartość ta zależna jest m. in. od przewodności cieplnej elementów formujących, temperatury medium w obiegu termostatującym, konstrukcji układu chłodzenia, rodzaju tworzywa, grubości ścian detalu wynikających z samej geometrii detalu. Skrócenie czasu chłodzenia możliwe jest do osiągnięcia przy zastosowaniu nowoczesnej technologii.
Czasami forma może posiadać znaczącą cześć powierzchni schłodzoną w sposób prawidłowy, podczas gdy jakiś jej niewielki fragment jest węzłem cieplnym, który nie pozwala na skrócenie czasu chłodzenia. Wykrycie węzłów termicznych formy jest rzeczą niezbędną do zoptymalizowania układu chłodzenia. Wykonanie pomiaru temperatury kamerą termowizyjną jest jedynym skutecznym sposobem pozwalającym na prawidłowe zdefiniowanie miejsca położenia węzłów termicznych.
Wykonanie analizy termograficznej jest szczególnie opłacalne w przypadku produkcji wielkoseryjnych, gdzie koszt potrzebny na modyfikację narzędzia, często stanowi tylko ułamek procentowy oszczędności wypracowanych po skróceniu czasu cyklu. W przypadku produkcji średnio i małoseryjnej również ma to ogromne znaczenie ze względu na racjonalną redukcję kosztów produkcji.
Metody dotykowe i bezdotykowe są niewiarygodne ponieważ nie można ich zastosować bez przerywania ciągłości procesu. Błąd pomiaru w przypadku pomiarów ręcznych jest tak duży, że może generować błędne wnioski. Przy użyciu kamery termowizyjnej dokonuje się w ułamku sekundy skanu temperatury całej badanej powierzchni. W związku z tym relacje pomiędzy punktami pomiarowymi są podane z dużą dokładnością. Ponadto pomiar trwa tylko kilka sekund i można go realizować w cyklu produkcyjnym bez konieczności przerywania owego cyklu, co jest niezwykle istotne do stwierdzenia węzłów termicznych formy w trakcie produkcji.
Wykonana w taki sposób analiza termalna narzędzia umożliwia określenie węzłów termicznych w gnieździe formy, co dzięki modyfikacjom układu chłodzenia przyczyni się do skrócenia czas cyklu produkcyjnego oraz poprawy jakości produkowanych części. Szczegółowy raport przedstawi następnie dokładną analizę termalną badanego narzędzia oraz wypraski, a także wskazówki, opracowane przez konstruktorów, dotyczące modyfikacji narzędzia. Analiza termiczna pozwoli zatem na optymalizację produkcji.
Jeśli chodzi o korzyści wynikające z badania, to przede wszystkim przynosi ono wykrycie gorących punktów, które nawet przy prawidłowej konstrukcji układu termostatującego formy charakteryzują się podwyższoną temperaturą w czasie trwania cyklu. Obszary te wymagają dłuższego czasu chłodzenia.
Inne korzyści to m.in. możliwość modyfikacji narzędzia - wiedza dostarczana przez raport z analizy termalnej narzędzia, pozwala na zmiany narzędzia, takie jak modyfikacje układu chłodzenia lub zmiany materiału, z którego wykonane są powierzchnię obierające ciepło w miejscach węzłów cieplnych. Zaletą jest też skrócenie czasu cyklu. Dzięki optymalizacji układu chłodzenia czas potrzebny na schłodzenie wypraski zmniejsza się. Krótszy czas cyklu podnosi natomiast wydajność formy. Następuje również poprawienie jakości wyprasek.
Wyeliminowanie miejsc o podwyższonej temperaturze wpływa bowiem pozytywnie na ujednolicenie połyskliwości detalu. Nieprawidłowy odbiór ciepła w miejscach o zwiększonej grubości detalu (żeberka), powoduje zwiększony skurcz objętościowy. W tych miejscach na detalu powstawać będą wady takie jak zapady i jamy skurczowe. Optymalizacja układu chłodzenia poprawi więc wytrzymałość mechaniczną detalu.