Innym ważnym kryterium przy wyborze materiałów np. na komponenty maszyn jest ich zachowanie trybologiczne. Czynniki takie jak zużycie i tarcie determinują żywotność komponentów takich jak łożyska ślizgowe, rolki prowadzące i koła zębate. Śrutowanie ma pozytywny wpływ na zachowanie trybologiczne. Na przykład w przypadku PA 66 obniża współczynnik zużycia o 60 do 70 procent.
- Sieciowanie radiacyjne tworzywa sztucznego jest zawsze przeprowadzane na gotowym elemencie przez dostawcę usług - podkreśla Daněk. - Producent komponentu może zatem wykonywać formowanie wtryskowe, rozdmuchowe lub przez wytłaczanie w zwykły sposób - Nie ponosi więc dodatkowych kosztów związanych z zakupem nowych maszyn lub narzędzi. Może on przeprowadzać standardowy proces produkcji z optymalną prędkością. Sieciowanie radiacyjne części u dostawcy usług można zintegrować z trasą transportu do klienta końcowego, oszczędzając w ten sposób czas. Obróbka końcowa nie jest konieczna.
Niższe koszty produkcji i materiałów
Formowanie wtryskowe tworzyw sztucznych zasadniczo eliminuje kosztowne etapy przetwarzania końcowego i montażu, które są często wymagane, gdy stopiony metal jest wlewany pod wysokim ciśnieniem do stalowej formy i zestalany w jednolity odlew. W celu przygotowania metalowego odlewu do użycia stosowane są zwykle procesy takie jak gratowanie, piaskowanie, frezowanie lub gwintowanie. Kolejną zaletą części z tworzyw sztucznych w porównaniu z częściami metalowymi jest brak konieczności stosowania ochrony antykorozyjnej. Wszystko to przyczynia się do tego, że oprócz kosztów materiałowych, koszty produkcji części formowanych wtryskowo są również niższe niż w przypadku części metalowych odlewanych ciśnieniowo.
Ale to nie wszystko: formowanie wtryskowe umożliwia produkcję bardziej złożonych geometrii i kolorowych komponentów. Daje to większą swobodę projektowania niż w przypadku odlewania ciśnieniowego metali. Kolejną zaletą tworzyw sztucznych jest to, że są lżejsze od metalu. Jest to szczególnie ważne w przypadku pojazdów: każdy gram zaoszczędzony na przykład w samochodach elektrycznych pomaga zmniejszyć zużycie energii. Zwiększa to dystans, jaki można przejechać na jednym ładowaniu akumulatora. Ponadto elementy z tworzyw sztucznych tłumią hałas lepiej niż metale, co jest ważne w przemyśle motoryzacyjnym i maszynowym.
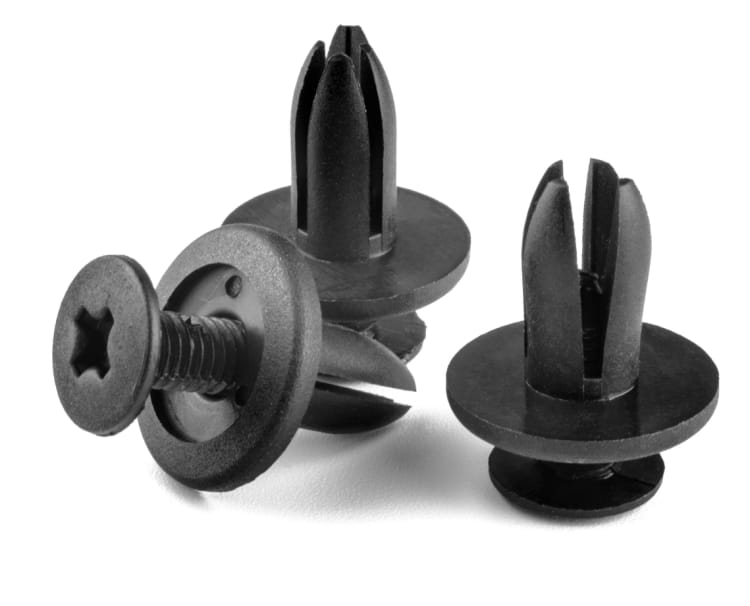
Śruby, rolki, wirniki i pokrywy wentylatorów
- Biorąc pod uwagę potencjalne oszczędności i wiele korzyści, producenci powinni sprawdzić, czy w niektórych zastosowaniach mogą zastąpić metalowe części odlewane ciśnieniowo usieciowanymi tworzywami sztucznymi - radzi Dr. Daněk, specjalista spółki BGS. Które konkretnie części odlewane ciśnieniowo? - Na przykład śruby, zaciski mocujące i rolki w samochodach oraz innych pojazdach, wirniki wentylatorów w pompach ciepła, obudowy sprzętu elektronicznego i klejone kompozyty plastikowo-metalowe w przemyśle stoczniowym.
Wnioski
Istnieje wiele czynników, które należy wziąć pod uwagę: Oprócz konkretnego zastosowania, obejmują one liczbę jednostek, złożoność konstrukcji i wymaganą jakość komponentów. Aby uwzględnić wszystkie aspekty, zalecana jest ścisła współpraca między inżynierami materiałowymi, konstruktorami i projektantami produktów. Metalową część odlewaną ciśnieniowo można następnie zastąpić bardziej opłacalną częścią z tworzywa sztucznego, formowaną wtryskowo.
Autor: dr Michal Daněk, BGS Beta-Gamma-Service