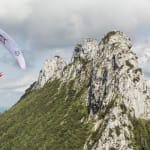
Aby sterować paralotnią, pilot musi balansować ciałem, utrzymując jednocześnie napięcie mięśni. Można to osiągnąć dzięki naciskaniu stopami na podpórkę w uprzęży. W sytuacjach ekstremalnych, takich jak nagłe manewry zwrotne przy zbliżaniu się do stromej ściany skalnej, na podpórkę działają bardzo duże siły, porównywalne z siłą pełnego dociśnięcia pedału hamulca w samochodzie w celu uniknięcia wypadku.
- Podpórka z łatwością wytrzymuje te obciążenia - wyjaśnia Harri Dittmar z Lanxess. - Sztywność i wytrzymałość na zginanie takich materiałów sandwiczowych może być wyższa niż płyty stalowej lub aluminiowej. Zależy to od grubości warstwy okładzinowej i struktury plastra miodu. Jednocześnie materiały te są dużo lżejsze w przeliczeniu na jednostkę powierzchni.
Trudne trasy alpinistyczne wymagają od pilota dużej sprawności fizycznej, ale również możliwie najlżejszego sprzętu.
- Przeprowadziliśmy szeroko zakrojone testy płyt sandwiczowych i jesteśmy bardzo zadowoleni z połączenia niskiej masy, wysokiej sztywności i wytrzymałości - powiedział Manfred Kistler, dyrektor generalny spółki Skywalk. - Płyty są o 20 proc. lżejsze niż ich poprzednia wersja wykonana z żywicy epoksydowej wzmacnianej włóknami węglowymi. Dzięki temu uprząż waży niewiele ponad kilogram. Kolejną zaletą materiału jest niższy koszt. Nowy komponent kosztuje o 25 proc. mniej niż ten wykonany z żywicy epoksydowej.
To nie jedyne zastosowanie materiałów Tepex. Lanxess dostrzega istotne możliwości zastosowania sandwiczowych materiałów kompozytowych w ultralekkich konstrukcjach samochodowych, szczególnie w produkcji większych części, które muszą się charakteryzować odpowiednią sztywnością, takich jak podłoga bagażnika, osłony zbiornika paliwa, obudowa przedłużacza zasięgu, obudowy baterii strukturalnych i elementy foteli.
- Materiał kompozytowy mógłby stanowić alternatywę dla materiałów z włókna szklanego i pianek poliuretanowych w sprayu stosowanych do produkcji podłóg bagażnika w samochodach osobowych - mówi Martin Klocke z firmy Lanxess. - Jedną z zalet tego materiału dla firm przetwarzających jest to, że nie musiałyby się zajmować systemami aktywnymi chemicznie i mogłyby wyeliminować znaczne koszty związane z urządzeniami i systemami bezpieczeństwa.
Materiały te można by też wykorzystać do produkcji osłon zbiorników paliwa, które stanowią część przestrzeni bagażnika. Wykonane z takiego materiału byłyby znacznie lżejsze niż ich odpowiedniki ze stali lub aluminium. Ponadto takie elementy jak rowki, prowadnice czy uchwyty mogłyby stanowić integralną część tych osłon i zostać wytworzone w ramach pojedynczego etapu produkcyjnego, co przyczyniłoby się do dalszej redukcji kosztów.