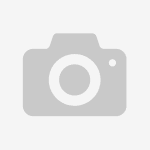
O rozwarstwieniu warstwy powierzchniowej wypraski mówimy w przypadku, gdy warstwy materiału nie są połączone ze sobą w sposób jednorodny i oddzielają się od siebie. Warstwy mogą łuszczyć się na nadlewie wtryskowym i wyprasce. Zależnie od poziomu intensywności rozwarstwienie może obejmować zarówno duże, jak i małe obszary.
Jakie są przyczyny powstawania tej wady?
Rozwarstwianie się warstwy powierzchniowej wiąże się z niewystarczającą adhezją przylegających do siebie warstw wypraski. Poszczególne warstwy wykształcają się na skutek różnych efektów przepływu strumienia oraz oddziaływania warunków chłodzenia nad przekrojem. Wysokie naprężenia ścinające, uszkodzenia termiczne lub niejednorodność mogą zmniejszać zwartość tych płytek. To z kolei powoduje odrywanie się pojedynczych warstw powierzchniowych. Wysokie naprężenia ścinające i uszkodzenia termiczne spowodowane są wysokimi prędkościami wtrysku, a także wysokimi temperaturami masy.
Niejednorodność mogą powodować następujące czynniki zanieczyszczenie lub materiały obce w granulacie, źle dobrany środek barwiący lub masterbacz, wilgoć na granulacie, nieprawidłowo roztopiona masa plastyczna.
Jedną z wad powierzchniowych wyprasek są rozwarstwienia jej warstwy powierzchniowej. Chcąc wyeliminować tę wadę powinno się dokładnie oczyścić maszynę przy zmianie tworzywa, tak aby uniknąć wszelkich zanieczyszczeń. Należy również sprawdzić czy stosowany barwnik albo masterbacz jest odpowiedni dla przetwarzanego tworzywa. Jeśli nadal będzie się otrzymywać wadliwe wypraski należy wtedy zmienić parametry przetwórstwa, tzn. zmniejszyć szybkość wtrysku i podwyższyć temperaturę przetwórstwa (wtrysku, formy).
Jeśli zaistnieje sytuacja rozwarstwienia po zmianie materiału albo koloru, to w takiej sytuacji należy podjąć kilka kroków. Trzeba sprawdzić granulat pod kątem występowania zanieczyszczeń lub materiałów obcych. Ponadto zaleca się zbadać tolerancję środka barwiącego, sprawdzić zawartość wilgoci oraz sprawdzić jednorodność topnienia i zdolność plastyfikowania. Nie należy natomiast zmniejszać prędkości posuwu ślimaka, obniżać temperatury masy oraz zwiększać temperatury ścianek formy.