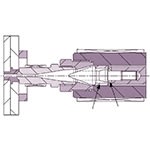
Przy przetwórstwie tworzyw sztucznych zużywanie się pewnych elementów jest zjawiskiem nieuniknionym. Na zużycie szczególnie narażone są zawory zwrotne i dysze, a w nieco mniejszym stopniu również ślimaki i cylindry. Chcąc ograniczyć zużycie do minimum, trzeba znać jego przyczyny.
Rozróżniamy zużycie abrazyjne (ścierne), którego przyczyną jest ruch ślizgowy granulatu lub stopu po metalu i które przyspieszane jest przez wysokie ciśnienia, temperatury i prędkości poślizgu oraz obecność napełniaczy i wzmacniaczy, oraz zużycie korozyjne, którego przyczyną jest chemiczne obciążenie stali przez przetwarzane tworzywo i znajdujące się w nim dodatki i które zwiększa się wraz ze wzrostem temperatury.
Zużycie elementów agregatu wtryskowego przy wtryskiwaniu tworzyw bez napełniaczy najczęściej jest małe, ale zwiększa się po dodaniu pigmentów i napełniaczy. Wzmacniacze typu włókna szklane lub węglowe oraz środki uniepalniające mogą powodować znaczne zwiększenie zużycia.
Konieczne jest regularne sprawdzanie elementów zużywających się, tzn. zaworów zwrotnych i dysz. Oznakami zużycia mogą być takie wady wyprasek, jak smugi, czarne wtrącenia i ciemne pasma. Wady w zakresie dokładności wymiarowej oraz paczenie się świadczą o zużyciu zaworu zwrotnego. Tworzenie wypływki (gratu) i przetryśnięcia informują o zużyciu płaszczyzny podziału formy.
Zużyciu abrazyjnemu można przeciwdziałać przez nadanie odpowiedniego kształtu ślimakom i zaworom zwrotnym. Do wielu tworzyw nadają się ślimaki, które przy całkowitej długości, co najmniej 20 D mają nachylenie zwojów 1 D, strefę zasilania o długości 10 do 12 D oraz strefę sprężania i dozowania o długości około 5 D.
Szczególnie ważne jest staranne wykonanie zaworów zwrotnych. Należy przy tym pamiętać, że prowadnica pierścienia blokującego musi być odpowiednio długa, a sam pierścień musi być prawidłowo osadzony i mieć prawidłowe powierzchnie uszczelniające. Gniazdo pierścienia powinno być zahartowane nieco wyżej niż pierścień. Czołowa powierzchnia dyszy musi być płaska i nieuszkodzona, tak aby szczelnie przylegała do powierzchni przeciwległej. Niedopuszczalna jest jakakolwiek szczelina, ponieważ wnikający w nią stop byłby przeciążony termicznie i ulegałby rozkładowi.