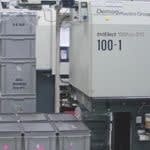
Szwajcarska firma Johnson Electric, użytkownik kilkudziesięciu wtryskarek Sumitomo, zajmuje się wytwarzaniem silników i napędów przeznaczonych do najróżniejszych zastosowań. Produkty znajdują zastosowanie przede wszystkim jako napędy w rozmaitych systemach oraz w sterowaniu światłami przednimi i przełącznikami zainstalowanymi na komponentach elektrycznych wyłączników zapłonu. Inne obszary zastosowań obejmują mechanizmy otwierania i zamykania okien, systemy ABS, pompy paliwowe i lusterka zewnętrzne.
Johnson Electric dysponuje pełnym łańcuchem produkcyjnym w przypadku podzespołów z tworzyw sztucznych. Formy wytwarzane są poza fabryką jedynie wtedy, gdy zachodzi potrzeba produkcji wyspecjalizowanych narzędzi. Johnson electric przetwarza materiały do zawartości 60 proc. włókna szklanego.
Od dawna spółka wykorzystuje w produkcji wtryskarki elektryczne. Wpływ na to ma nie tylko ich wysoki poziom obsługi. W dłuższej perspektywie czasu istotne są zwłaszcza oszczędności w zakresie energii.
Podczas gdy hydrauliczna wtryskarka 1500 kN wykorzystywana do produkcji serii resoraków o wadze14 g przy formie 4+4 pobiera średnio 516 kWh energii, wtryskarka IntElect Sumitomo (SHI) Demag 150-610 produkuje te same części wykorzystując średnio 306 kWh.
- Możemy to efektywnie wyliczyć, ponieważ często produkujemy ten sam produkt z identycznie skonstruowaną formą na kilku różnych maszynach - wyjaśniają przedstawiciele producenta. - W przypadku serii małych samochodzików ograniczenie poboru energii daje nam oszczędności rzędu 11700 franków szwajcarskich rocznie. Biorąc pod uwagę tylko te obliczenia łatwo dojdziemy do wniosku, że inwestycja w IntElect spłaca się już po upływie około pięciu lat.
Szczytowy skok energii elektrycznej w przypadku wtryskarki IntElect jest każdorazowo niższy niż w przypadku maszyn hydraulicznych. Jest to istotne w momencie ustalania wartości znamionowej mocy głównego przyłącza energetycznego. Kolejną zaletą wtryskarek IntElect ma być ich precyzja, dzięki czemu podzespoły, takie jak choćby łożyska mogą być dokładnie osadzane.
Johnson przeprowadził porównanie produkcji przy wykorzystaniu tej samej formy na wtryskarce IntElect i maszynie hydraulicznej. Następnie sprawdził charakterystykę wymiarową wszystkich wyprasek. Podczas, gdy maszyna elektryczna wyprodukowała detale o długości nieznacznie poniżej 17 mm i maksymalnej różnicy na długości wynoszącej 0,024 mm, ta sama różnica w przypadku maszyny hydraulicznej była już nawet dwukrotnie większa.
Johnson Electric przeprowadził także testy z inną przekładnią, w trakcie których wtryskarka IntElect wykazała podobny wzrost precyzji. W chwili obecnej do produkcji przekładni wykorzystywane są dwie wtryskarki IntElect 100-310 oraz formy 16-gniazdowe. W przypadku w pełni zautomatyzowanej produkcji każdy wtrysk poddawany jest kontroli jakości z pomocą robota.
Po każdym wtrysku maszyna sprawdza zgodność i w przypadku przekroczenia tolerancji jakościowej separuje wtrysk do oddzielnego pojemnika. Dzieje się to jednak niezmiernie rzadko. Dodatkowo, co dwie godziny pobierany jest kompletny wtrysk i poddawany jest badaniu mikroskopowemu i wymiarowemu.
Przekładnia jest podzespołem tzw. silnika matchbox i jest zainstalowana w obudowie wykonanej z polipropylenu wzmocnionego włóknem szklanym, która stanowi część gotowego silnika. Obudowy i pokrywy wykonywane są w formie 4+4 na wtryskarce IntElect 150-610. Każdy 14 gramowy komponent wykonywany jest w czasie 19 sekund.