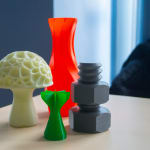
Wytwarzanie przyrostowe to proces produkcji, w którym obiekt jest tworzony warstwa po warstwie, zwykle przy użyciu technologii takich jak druk 3D. W odróżnieniu od tradycyjnych metod, które często polegają na usuwaniu materiału (np. cięcie, frezowanie) lub jego kształtowaniu (np. odlewanie, kucie), technologia przyrostowa polega na dodawaniu materiału, co pozwala na większą swobodę w projektowaniu skomplikowanych kształtów i struktur.
Pierwszy system produkcji addytywnej pojawił się w latach 80. XX w. Prace Hideo Kodamy i Charlesa Hulla doprowadziły do opatentowania i wprowadzenia na rynek urządzenia wykorzystującego proces fotopolimeryzacji żywic pod wpływem światła UV, zwany też stereolitografią (SLA).
W 1991 r. Scott Crump wynalazł technologię Fused Deposition Modeling (FDM), w której termoplastyczny polimer w kształcie drutu (zwany filamentem) jest topiony i wytłaczany przez dyszę o małej średnicy. Firma Cubital wypuściła na rynek technologię Solid Ground Curing (SGC) opartą na fotopolimerach utwardzanych silnym światłem UV. Natomiast firma Helisys wprowadziła technikę Laminated Object Manufacturing (LOM), zwaną wytwarzaniem obiektów laminowanych, polegającą na łączeniu arkuszy materiału z wykorzystaniem kleju (inną technologią tego typu jest ultradźwiękowa produkcja przyrostowa - UAM).
W 1992 r. wynaleziony i opatentowany został proces selektywnego spiekania laserowego (SLS - Selective Laser Sintering) wykorzystujący źródło energii cieplnej do stapiania określonych obszarów sproszkowanego materiału. Z kolei w 1994 r. skomercjalizowano systemy oferowane przez Solidscape, które działały w technologii "drop on demand" (DOD). Detale powstawały ze stopniowo natryskiwanego i utwardzanego materiału. W latach 1994-1997 pracowano zaś nad technologiami Directed Energy Deposition (DED), polegającymi na topieniu materiałów w trakcie ich odkładania. Istnieje kilka procesów należących do tej kategorii.
Po roku 2000 coraz więcej firm i entuzjastów zaczęło interesować się możliwościami i podstawowymi korzyściami procesowymi oferowanymi przez druk 3D. W tym czasie najbardziej rozpowszechniły się drukarki 3D do modelowania oparte na formowaniu wytłaczanego materiału (FDM).
W 2013 r. firma Markforged przedstawiła rewolucyjną konstrukcję drukarki 3D z możliwością stosowania metod takich jak Fused Filament Fabrication (FFF), w której obiekt powstaje poprzez nakładanie stopionego materiału warstwa po warstwie i Continuous Fiber Reinforcement (CFR). Drukarka CFR wykorzystuje 2 systemy wytłaczania: jeden do wytłaczania kompozytowego materiału bazowego w standardowym procesie przyrostowym oraz drugi do wytłaczania długich, mocnych włókien ciągłych, które są precyzyjnie układane warstwowo, zastępując wypełnienie FFF.
Od tego czasu produkcja addytywna rozwinęła się, rozgałęziając się na kilka różnych typów przekształcania plików typu CAD w fizyczne obiekty 3D, które zestawiono w normie ISO 52900:2021.
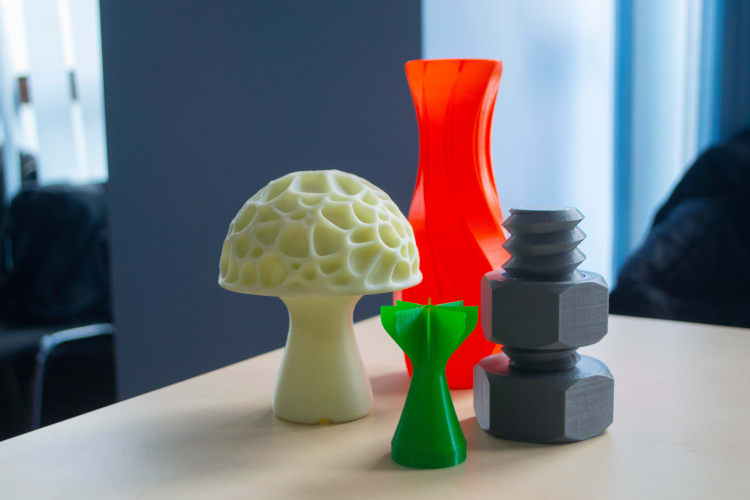
Podstawowe procesy wytwarzania przyrostowego wg ISO 52900:2021:
- VPP - VAT Photopolymerization: fotopolimeryzacja objętościowa. Proces, w którym ciekły fotopolimer w kadzi jest selektywnie utwardzany w procesie polimeryzacji aktywowanej światłem (SLA)
- MEX - Material Extrusion: wytłaczanie warstwowe materiału. Proces, w którym materiał jest selektywnie dozowany przez dyszę lub otwór (SSE, FFF)
- PBF - Powder Bed Fusion: selektywne spajanie sproszkowanego materiału. Proces, w którym energia cieplna selektywnie łączy obszary złoża proszku (SLS)
- DED - Directed Energy Deposition: ukierunkowane stapianie dostarczanego materiału. Proces, w którym do łączenia materiałów wykorzystywana jest skoncentrowana energia cieplna poprzez ich topienie w trakcie osadzania
- MJT - Material Jetting Additive: warstwowy nadruk płynnego materiału. Proces, w którym selektywnie osadzane są krople materiału wsadowego
- BJT - Binder Jetting: spajanie sproszkowanego materiału płynnym spoiwem. Proces, w którym ciekły środek wiążący jest selektywnie osadzany w celu połączenia materiałów proszkowych
- SHL - Sheet Lamination: laminacja warstwowa przekrojów. Proces, w którym w celu utworzenia detalu łączone są arkusze materiału (LOM).
Obecnie produkcja addytywna znacząco wspiera rozwój największych światowych branż - przemysłu, medycyny, motoryzacji. Przemysł lotniczy, edukacyjny i obronny również wdrażają produkcję addytywną w coraz szybszym tempie.
Współczesne techniki produkcji przyrostowej charakteryzują się m.in. niezawodnością przy większych prędkościach drukowania, łatwością obsługi i użytkowania. Nowoczesne oprogramowanie do druku 3D jest intuicyjne w użyciu i nie wymaga specjalistycznej wiedzy w zakresie produkcji addytywnej.
Gwałtowny rozwój technologii przyrostowej, pozostającej nadal stosunkowo nowym procesem, związany jest z tkwiącym w niej potencjałem do skutecznego rozwiązywania wielu problemów produkcyjnych. Zwiększa ona swobodę projektowania bez ograniczeń narzucanych przez tradycyjne technologie obróbki i kształtowania materiałów oraz pozwala drastycznie skrócić czas prototypowania i realizacji zamówień, jak również zredukować ilość odpadów.
Jak można się domyślić, w technologii przyrostowej bardziej niż elastomery rozpowszechnione są termoplasty. Materiały elastyczne odkształcają się pod wpływem naprężeń i formowane obiekty 3D mogą ulegać deformacjom. Szersze zastosowanie znalazły elastomery termoplastyczne (TPE) i kauczuki silikonowe.
TPE to polimery łączące w pewnym przedziale temperatury cechy usieciowanych chemicznie kauczuków z łatwością przetwarzania i recyklingu termoplastów. Zazwyczaj składają się z miękkiej fazy elastomerowej i twardych segmentów termoplastycznych. Umożliwiają produkcję przedmiotów przypominających gumę poprzez wytwarzanie addytywne, charakteryzując się takimi cechami jak elastyczność i sprężystość. Ponadto mają doskonałe właściwości fizykomechaniczne, są lekkie, mają zdolność wiązania się z wieloma tworzywami termoplastycznymi. Cechują się także dobrą odpornością chemiczną. Można je podzielić na 6 grup, szeregując je wg ceny i zapotrzebowania:
- styrenowe kopolimery blokowe (SBC lub TPE-S)
- elastomery poliuretanowe (TPU lub TPE-U)
- wulkanizaty termoplastyczne (TPV, TPE-V) lub inaczej mieszaniny elastomer/termoplast (EA - ang. elastomeric alloys)
- termoplastyczne poliolefiny (TPO lub TPE-O)
- kopolimery poliestrowe (COPE lub TPEE lub TPE-E)
- blokowe kopolimery amidowo-eterowe (COPA lub PEBA lub TPE-A).