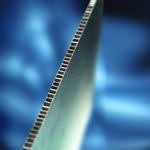
BASF sukcesywnie rozwija swoje technologie wykorzystania tworzyw sztucznych do produkcji nadwozi i podwozi samochodowych. W tym celu prowadzi jednoczesne badania nad trzema systemami matryc tworzyw sztucznych: żywicy epoksydowej, poliuretanu oraz poliamidu. Wszystko to ma doprowadzić do trwałego wzmocnienia włókien w procesie formowania wtryskowego produktów z żywic w sposób możliwy do uzyskania w produkcji masowej. W grę wchodzi też wykorzystanie metody produkcji wyrobów na formach zamkniętych (RTM).
Pod markami Baxxodur i Elastolit R koncern dostarcza rozwiązania oparte na systemach żywic epoksydowych i poliuretanu. Te termoutwardzalne materiały charakteryzują się nowatorskimi mechanizmami utwardzającymi dzięki którym wiążą się w przeciągu kilku minut. Mogą być przetwarzane przy pomocy zarówno wysoko- jak i niskociśnieniowych urządzeń. Nowe systemy poliamidowe są budowane począwszy od kaprolaktamu o bardzo niskiej lepkości, prekursora PA6, zaawansowanego aktywatora i układów katalizatorów.
Tego typu termoplastyczne kompozyty mogą być odpowiednio formowane, poddawane recyklingowi i spawane. Oprócz elementów doczepianych, takich jak drzwi, bagażniki, dachy, potencjalne zastosowanie powyższych technologii dotyczy również elementów samochodu narażonych na wysokie obciążenie.
Pierwszym modelem pokazowym firmy BASF opartym na wielowarstwowych tworzywach przetwarzanych metodą RTM jest projekt koncepcyjny wielosegmentowego, składanego dachu samochodowego.
Moduł dachu wykonany jest z poliuretanowego rdzenia piankowego umieszczonego pomiędzy warstwami wzmocnionego włókna węglowego. Warstwa rdzenia modelu pokazowego jest tworzywem spienionym o komórkach zamkniętych PUR nazwanym Elastolit D. Dzięki niskiej gęstości objętościowej działa jako separator warstw laminatu, zapewniając bardzo dużą sztywność komponentów. Jako moduł dachu, posiada również bardzo pożądane właściwości izolacyjne. Przy masie całkowitej wynoszącej 2,6 kg, dach zbudowany przy użyciu materiałów kompozytowych wzmocnionych włóknami traci swój ciężar o 40 proc. w porównaniu z technologią aluminiową, a w porównaniu z technologią stalową o ponad 60 proc.