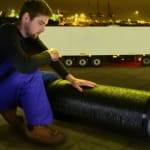
Osiągnięcie w postaci wykonanych z tworzywa zbiorników sprężonego powietrza dla przyczep do samochodów ciężarowych zostało zaprezentowane po raz pierwszy na niedawnych Międzynarodowych Targach Motoryzacyjnych Pojazdów Użytkowych w Hanowerze. Część ta została opracowana przez niemiecką spółkę Comat z użyciem precyzyjnie dobranych rodzajów poliamidu Ultramid z gamy produktów BASF.
Zbiornik ma długość 1,2 m, średnicę 32 cm i pojemność 80 l. W samochodach ciężarowych służy do magazynowania sprężonego powietrza dla potrzeb licznych funkcji mechanicznych, szczególnie układu hamulcowego i zawieszenia pneumatycznego. Do tej pory zbiorniki sprężonego powietrza wykonywano z metalu.
Zmniejszenie ciężaru o 10 kg, w połączeniu z kosztami, które są porównywalne do kosztów poprzednich zbiorników to główny powód, dla którego projekt był realizowany.
- Nowe zbiorniki sprężonego powietrza wykonane z tworzywa sztucznego spełniają wysokie wymagania, które stawialiśmy także wcześniejszym, metalowym wersjom. Jest to wielki krok w kierunku szerszego stosowania tworzyw w samochodach ciężarowych - tłumaczą przedstawiciele firmy Comat.