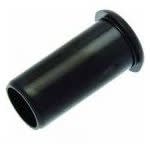
Zmiany wymiarów detali wytwarzanych wtryskowo mają miejsce podczas formowania, a mogą wystąpić także po jego zakończeniu oraz podczas późniejszej eksploatacji tychże detali. Czasami zmiany takie są wywoływane przez czynniki zewnętrzne powodujące przyspieszenie tego procesu. Niezależnie od okoliczności stabilność wymiarowa detali zależna jest od takich czynników jak skurcz, absorpcja wody, skurcz po wyjęciu z formy oraz wygrzewanie.
W celu uzyskania lepszej kontroli nad absorpcją wody i skurczem, wypraskę po wyjęciu z formy często zaleca się poddać starzeniu wilgotnościowemu, czyli nasyceniu wilgocią, a także odprężaniu poprzez wygrzewanie. Po wyjęciu wypraski z formy i ochłodzeniu do temperatury pokojowej jej wymiary są zazwyczaj mniejsze niż wymiary gniazda w formie. Różnica pomiędzy nimi, wyrażona w procentach jest określana jako skurcz wypraski.
Wielkość skurczu zmienia się znacznie w zależności od kształtu formowanych detali. Oznacza to, że aby mieć możliwość porównania tworzyw należy odpowiednio zdefiniować skurcz. Przyjmuje się, że modelowo jest to skurcz prostopadłościanu o wymiarach 127 x 12,7 x 3,2 mm, z czołowo umieszczonym otworem wtryskowym, suchego po uformowaniu w temperaturze 23 st. C.
Sam skurcz wypraski zależy natomiast od gatunku przetwarzanego tworzywa, warunków jego formowania oraz konstrukcji używanej formy. Czynniki decydujące o końcowym efekcie w każdej z wymienionych kategorii to:
- typ tworzywa: procentowa zawartość włókna szklanego, obecność zarodków krystalizacji oraz pigmenty,
- warunki przetwórstwa: temperatura formy, temperatura stopionego tworzywa, ciśnienie wtrysku i ciśnienie docisku oraz czas docisku,
- konstrukcja formy: grubość detali, konstrukcja przewężki i jej usytuowanie.
W przypadku tworzyw wzmocnionych włóknem szklanym skurcz w kierunku zgodnym z orientacją włókien jest mniejszy niż skurcz w kierunku poprzecznym. Z tego też powodu bardziej praktyczne jest zastosowanie wypraski płytowej w celu odróżnienia skurczu w kierunku przepływu od skurczu w kierunku do niego prostopadłym. Ze względu na to, że w detalach występuje kombinacja zarówno skurczu swobodnego jak i „ograniczonego”, warto być przygotowanym na obydwa rodzaje skurczów.
Ze względu na izotropię skurczu i wpływ powyższych czynników – izotropowość materiału to brak różnic we właściwościach fizycznych, takich jak rozszerzalność termiczna, przewodzenie ciepła, przewodnictwo elektryczne czy współczynnik załamania światła, niezależnie od tego w jakim kierunku są one mierzone - warto wykonywać wypraski prototypowe w celu uzyskania precyzyjnych danych wymiarowych dla części skomplikowanych i precyzyjnych.