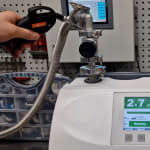
Nieszczelności w systemach próżniowych mogą powodować znaczne szkody we wrażliwych procesach przemysłowych. Zdolność pompy próżniowej do wytwarzania i utrzymania odpowiedniego poziomu próżni jest zagrożona, gdy gaz procesowy wydostaje się z pompy lub gdy przedostają się zanieczyszczenia, takie jak powietrze czy pył. Prowadzi to do przyspieszonego zużycia wewnętrznych komponentów, takich jak uszczelnienia i uszczelki, a pompa próżniowa może ulec awarii lub wymagać częstszych prac serwisowych. W rezultacie znacznie wzrastają rachunki za energię i ogólne koszty eksploatacji, a osiągi ulegają pogorszeniu. Dlatego helowe wykrywacze nieszczelności odgrywają kluczową rolę w zapewnieniu integralności sprzętu.
Nie wszystkie nieszczelności są widoczne. Niektóre z nich mogą być bardzo małe lub ukryte, co wymaga systematycznego podejścia do ich wykrywania. Warto wdrożyć nasze siedem najlepszych praktyk, aby przeprowadzać dokładne i skuteczne testy wykrywania nieszczelności. Zarówno w przypadku doświadczonych profesjonalistów, jak i u osób korzystających ze sprzętu do wykrywania nieszczelności po raz pierwszy niniejsze wytyczne poprawią wydajność procesu wykrywania nieszczelności przy użyciu helu jako gazu znakującego.
Szkolenie i środki ostrożności
Szkolenie operatorów w zakresie prawidłowego korzystania z wykrywacza nieszczelności jest niezbędne do uzyskania dokładnych wyników testów i wydłużenia żywotności sprzętu do testów. Jeśli operatorzy wiedzą, jak prawidłowo korzystać z wykrywacza nieszczelności, są mniej narażeni na rejestrowanie nieprawidłowych danych. Można to osiągnąć poprzez dokładne zapoznanie się z instrukcją obsługi i wytycznymi oraz przez udział w szkoleniach.
Ponadto konieczne jest ustalenie i przestrzeganie protokołów bezpieczeństwa. Obejmuje to prawidłowe stosowanie środków ochrony indywidualnej (ŚOI) podczas pracy z helem i innymi potencjalnie niebezpiecznymi substancjami. Na przykład należy zachować ostrożność podczas stosowania helu, ponieważ w wysokich stężeniach może on działać dusząco. Połączenie odpowiedniego szkolenia, zrozumienia specyfiki sprzętu i przestrzegania wytycznych dotyczących bezpieczeństwa pozwala zoptymalizować skuteczność wykrywacza nieszczelności przy jednoczesnym zapewnieniu bezpiecznego środowiska pracy.
Stabilne środowisko testów
Aby uzyskać dokładne wyniki, testy szczelności należy przeprowadzać w stabilnym środowisku o stałej temperaturze. Wyższe temperatury powodują rozszerzanie się cząsteczek helu, co prowadzi do zmniejszenia gęstości gazu. Powoduje to zwiększenie wyporności i rozproszenia gazu. Z drugiej strony niższe temperatury powodują, że cząsteczki helu ulegają skurczeniu, zwiększając gęstość gazu i spowalniając jego ruch. Te zmiany zachowania gazu znakującego wpływają na sposób jego przechodzenia przez obiekt testowy lub wokół niego, co przekłada się na dokładność testu wykrywania nieszczelności. Stabilne środowisko zapewnia stałe zachowanie gazu, dzięki czemu można uzyskać rzetelne wyniki. Ponadto kluczowe znaczenie ma utrzymywanie czystości zarówno w przypadku sprzętu, jak i obszaru testów. Pył, olej i inne cząstki mogą negatywnie wpływać na niezawodność sprzętu do wykrywania nieszczelności.
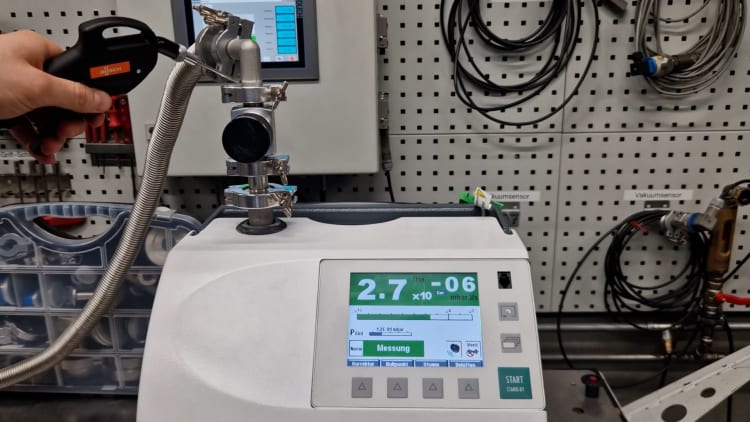
Prawidłowe ustawienie
Przed rozpoczęciem procesu wykrywania nieszczelności należy odpowiednio przygotować testowany obiekt. Testowany obiekt może być np. rurociągiem, zbiornikiem i innym elementem sprzętu. Należy zadbać o jego suchość i czystość. Wszelkie gazy lub substancje, które mogą negatywnie wpływać na dokładność procesu wykrywania nieszczelności, muszą zostać odprowadzone. Dzięki temu wyniki będą odzwierciedlać rzeczywiste warunki testowanego obiektu. Następnie należy wyzerować wykrywacz nieszczelności, tak aby zaczynał pracę z czystym rejestrem. Bez prawidłowego wyzerowania może nie wykryć małych wycieków, co prowadzi do niedokładnych wyników. Następnie należy zoptymalizować sprzęt poprzez dostosowanie ustawień czułości do oczekiwanego wskaźnika wycieku. Pozwoli to zminimalizować liczbę fałszywych alarmów.
Potem należy wybrać metodę testową, która najlepiej pasuje do danego obiektu i procesu. Na przykład test rozpylania nadaje się do komponentów w próżni. Hel jest rozpylany na powierzchnię testowanego obiektu. W przypadku nieszczelności cząsteczki gazu znakującego są wciągane do wykrywacza nieszczelności, który mierzy wskaźnik wycieku. W przypadku komponentów pod ciśnieniem najlepiej nadaje się test wykrywania nieszczelności przez wyczuwanie, ponieważ bezpośrednio wykrywa ulatniające się gazy. Hel jest pompowany do testowanego obiektu, a nad nim prowadzona jest sonda pomiarowa, narzędzie zaprojektowane do wykrywania i lokalizacji nieszczelności. Sonda pomiarowa działa podobnie jak wykrywacz metali, tylko szuka śladów helu w celu zlokalizowania nieszczelności. Obie metody testowe są łatwe w wykorzystaniu i dają dokładne rezultaty.