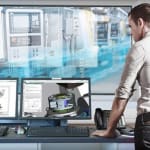
Producent form w Europie musi konkurować z producentami z mniej regulowanych rynków oraz z lokalnymi firmami, jednocześnie dostarczając produkty szybciej, by dostosować się do cyklów rozwoju produktu, które są obecnie o połowę krótsze niż kiedyś. Na przykład, w przemyśle samochodowym opracowanie nowego pojazdu trwało niegdyś dziewięć, a nawet dziesięć lat, a obecnie czas ten skrócił się do zaledwie czterech lat, co oznacza, że czas realizacji elementów jest również krótszy.
Aby poprawić efektywność produkcji, producenci części często starają się zautomatyzować niektóre kroki w procesie, wykorzystując oddzielne systemy oprogramowania, arkusze i dokumentację papierową. Jeśli nie zostanie to zrobione poprawnie, proces często staje się chaotyczny, a wartościowe informacje i krytyczne know-how nie jest wykorzystywane w sposób efektywny. Takie podejście nie sprawia, że producenci stają się bardziej skuteczni lub konkurencyjni.
By osiągnąć wyższy poziom efektywności produkcji i dotrzymać kroku konkurencji, narzędziownie potrzebują nowego modelu biznesowego, który pozwoli im wykorzystać najnowsze techniki. Wykorzystanie jednego zintegrowanego systemu oprogramowania tworzy spójne modele i procesy oraz łączy planowanie w dziale konstrukcji z wytwarzaniem na hali produkcyjnej za pośrednictwem „cyfrowej nitki”, która biegnie przez całą firmę, upraszcza proces produkcji części, obniża koszty i zwiększa prędkość.
Zamiast budowania modelów CAD, które muszą być eksportowane i importowane przez systemy komputerowe wykorzystywane na wszystkich poszczególnych etapach produkcji, możesz stworzyć kopię „digital twin” („cyfrowy bliźniak”) - precyzyjną, wirtualną kopię fizycznego produktu, która przechodzi pomiędzy poszczególnymi działami, nie tracąc na dokładności i pomagając w stworzeniu części, która będzie dokładnie odpowiadać potrzebom klienta.
Taki zdigitalizowany proces produkcji natychmiast sprawia, że nawet małe warsztaty stają się szybsze i bardziej efektywne, ale zapewnia też skalowalność, pomagając im w rozwoju działalności. Digitalizacja oznacza nie tylko uniknięcie konieczności manualnego przenoszenia i dostosowywania modelu na każdym etapie procesu. Wykorzystywanie jednego systemu oprogramowania i jednego precyzyjnego, spójnego modelu pozwala różnym zespołom pracować równolegle, a operatorzy sprawdzają plan procesu, gdy części są ciągle jeszcze programowane w module CAM. Takie podejście umożliwia automatyzację całego procesu, jednocześnie wciąż zapewniając elastyczność i adaptacyjność.
Jeśli w projekcie zostaną dokonane jakiekolwiek zmiany, automatycznie przechodzą one do wszystkich etapów procesu, bez konieczności przeprogramowania. Można porównać model do ukończonych części, wykorzystując współrzędnościowe maszyny pomiarowe (CMM), przesyłające informacje z powrotem do tego samego oprogramowania, które programuje maszyny do toczenia lub frezowania. Ułatwia to znalezienie i naprawienie wszelkich programów związanych z produkcją, zapewniając zamkniętą pętlę projektowania i udoskonaleń procesowych.