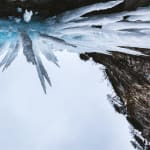
O chłodnictwie można mówić bardzo surowym językiem. Nie wierzysz? Oto przykład.
Chłodzenie to proces odbioru ciepła, w którym zazwyczaj obniżana jest temperatura. Sprężarkowe układy chłodnicze opierają się o obieg Lindego, w którym zachodzi szereg zmian termodynamicznych; izentropowe sprężanie, izobaryczne skraplanie, izentalpowe rozprężanie i izotermiczne parowanie.
W podobnym tonie książki mówią o transporcie ciepła, wykresie Moliera czy prawach termodynamiki. Mam wrażenie, że nawet moja twarz blednie, kiedy czytam takie formułki. Tymczasem termodynamika jest fascynująca - to raz. I ważna - to dwa. Bez chłodu nie powstanie większość otaczającego nas nowoczesnego świata, w tym oczywiście produkty z tworzyw sztucznych.
W przeciwieństwie do tego co powyżej, zawsze staram się pisać w sposób przystępny treści, do których warto wracać. Dlatego dziś przeczytasz wszystkie najważniejsze informacje o chłodnictwie dla twojej branży. Od przyłącza maszyny, do miejsca gdzie chiller wyrzuca ciepło do otoczenia. Napiszę o bilansie chłodniczym, o rurociągach, o pompach, o architekturze systemów chłodniczych, o tym jakie temperatury w jaki sposób się wytwarza.
Bilans chłodniczy
Bilans chłodniczy jest sumą ciepła, które musi być usunięte z układu. Składają się na niego: ciepło chłodzenia produktu, ciepło chłodzenia formy, straty na rurociągach, straty w zbiorniku, praca maszyn (praca mechaniczna ostatecznie musi być usunięta w formie ciepła) i inne - wszystkie strumienie energii, które należy usunąć z danego układu.
Uwzględniając bezpieczny zapas, całościowy bilans chłodniczy często jest dwukrotnością ciepła, które należy usunąć od samego produktu. Ciepło do usunięcia z produktu to masa półproduktu przerabiana w każdej godzinie, razy różnica temperatur wejścia/wyjścia, razy ciepło właściwe.
Bilans wyraża się w kilowatach (kW) i liczy się oddzielnie dla każdego poziomu temperatur; np. dla 10ºC - chłodzenie form, 30ºC - chłodzenie oleju, 40ºC - chłodzenie sprężarek. Wymagane moce chłodnicze w różnych temperaturach można teoretycznie dodać, ale wtedy chłód należy wytwarzać w najniższym wymaganym parametrze temperatury, co jest energetycznym barbarzyństwem. Jeśli masz wątpliwości co do tego, jaki jest bilans chłodniczy w twoim zakładzie, możesz napisać do mnie na LinkedIn.
Architektura systemu chłodzenia
W przetwórstwie tworzyw sztucznych stosuje się najczęściej wodne układy chłodnicze. Kiedy piszę wodne, mam na myśli, że chłód jest transportowany za pomocą czynnika pośredniego. Może to być woda, różnorodne mieszaniny glikoli, olej, itd. Najogólniej, schemat ideowy układu pośredniego przedstawiam poniżej. Dla prostoty, parę rurociągów oznaczyłem jedną linią. Składa się on ze źródła chłodu (chiller, drycooler, wieża chłodnicza, itd.); zbiornika buforowego/sprzęgła; zespołu pompowego pierwotnego - ładującego "chłodem" zbiornik buforowy; zespołu pompowego wtórnego - podającego "chłód" do twoich maszyn; rurociągów. Najczęściej stosuje się układy otwarte. Są one tańsze w wykonaniu i łatwiejsze w eksploatacji.
Wiem, że w poszukiwaniu oszczędności czasem próbuje się pominąć stosowanie zbiornika (i dodatkowej pompy). Jest to bardzo niepożądane, ponieważ tak ubogi układ będzie trudny w regulacji. Temperatura będzie niestabilna, skoki ciśnienia znaczne i w efekcie parametry eksploatacyjne będą znacznie gorsze. Co oczywiste, jeśli źródło chłodu znajduje się na zewnątrz, czynnikiem roboczym nie może być woda. Stosuje się wtedy glikole. Najczęściej MPG35%, który ma certyfikaty do pracy do temperatury -17ºC. W takich układach stosuje się dodatkowo wymiennik ciepła woda/glikol, lub cały układ pracuje na glikolu.
Glikol ma tendencję do zbierania wszelkich zanieczyszczeń z całego układu. Wielokrotnie widziałem instalacje, w których czynnik pośredni miał ciemnobrązowy kolor, dużo pyłów i oka oleju jak w rosole. Jest to oczywiście sygnał, że w układzie dzieje się coś złego. Zwykły filtr siatkowy nie poradzi sobie z usunięciem tego typu zanieczyszczeń. Dlatego w swojej praktyce stosuję dodatkowe, bardzo dokładne stacje filtrujące.