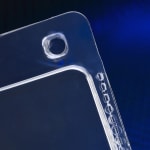
Producenci produktów z tworzyw sztucznych, w szczególności producenci opakowań, zobowiązali się do podjęcia globalnych wysiłków na rzecz ograniczenia stosowania opakowań jednorazowych i zwiększenia wykorzystania tworzyw sztucznych nadających się do recyklingu lub bio-pochodnych. W branży produkcji tworzyw sztucznych podejmowane są również wysiłki mające na celu stworzenie zasad, które poprawią zrozumienie przez społeczeństwo sposobów wykorzystania i recyklingu bio-pochodnych tworzyw sztucznych (ang. bio-based plastics - BBP) oraz biodegradowalnych i kompostowalnych tworzyw sztucznych (ang. Biodegradable and Compostable Plastics - BDCP).
Temat ten może być złożony, ponieważ bio-pochodne i biodegradowalne tworzywa sztuczne różnią się między sobą. Obecnie opakowania z tworzyw sztucznych wymagają jedynie min. 20% zawartości surowców biologicznych, aby można je było uznać za BBP; pozostała zawartość może, ale nie musi być biodegradowalna. Ponadto, chociaż BDCP ulegają biodegradacji, nie ma wytycznych dotyczących tego, czy powinny wymagać kompostowania przemysłowego, czy powinny rozkładać się w glebie lub wodzie, ani jak długo powinna trwać ich całkowita biodegradacja. Obecnie branża pracuje nad ustaleniem wytycznych, które zajmą się tymi kwestiami.
Niektóre stany USA realizują inicjatywę o nazwie Rozszerzona Odpowiedzialność Producenta (EPR), mającą na celu nałożenie na producentów większej odpowiedzialności za cykl życia ich produktów i opakowań, aby zapewnić ich ponowne wykorzystanie, recykling, kompostowanie lub biodegradację. Kilka celów inicjatywy EPR obejmuje:
- Maksymalizację recyklingu i potencjału gromadzenia odpadów
- Minimalizację wykorzystania jednorazowych opakowań oraz tworzyw sztucznych
- Rozszerzanie udziału producentów w „organizacjach odpowiedzialności producenta”
- Zwiększanie recyklingu butelek po napojach i zawartości materiałów pochodzących z recyklingu w produktach z tworzyw sztucznych
Niektórzy z wiodących światowych producentów produktów konsumenckich przyłączyli się do wysiłków i podjęli imponujące zobowiązanie, że do 2025 r. 100% ich opakowań będzie nadawało się do ponownego użycia, recyklingu lub kompostowania. Giganci korporacyjni tacy jak Johnson & Johnson, Colgate-Palmolive, Unilever, SC Johnson, Mars, Apple, Nestle, Walmart, Coca-Cola, i PepsiCo znajdują się wśród ponad 250 producentów odpowiedzialnych za produkcję ok. 20% opakowań z tworzyw sztucznych na świecie.
Producenci towarów konsumpcyjnych nie są jedynymi uczestnikami inicjatywy na rzecz przejścia na większą ilość BBP i BDCP. Producenci żywic, producenci opakowań i folii, dostawcy technologii - wszyscy w łańcuchu wartości tworzyw sztucznych – pracują nad opracowaniem bardziej zrównoważonych rozwiązań opakowaniowych z wykorzystaniem BBP i BDCP.
Firma Emerson wnosi znaczący wkład w ten globalny wysiłek, rozwijając swoją technologię łączenia tworzyw sztucznych, aby umożliwić odejście od tradycyjnych plastików. Emerson współpracuje z producentami żywic i innymi innowatorami w dziedzinie tworzyw sztucznych
w celu stworzenia nowych i skutecznych profili łączenia dla bio-plastiku, które zapewnią wydajność na poziomie komercyjnym dla milionów toreb, woreczków, kartonów, pojemników na kawę, zakrętek, filtrów czy też uszczelek.
Produkcja komercyjnych opakowań i uszczelnień z wykorzystaniem BBP i BDCP wymaga znacznie bardziej rygorystycznej kontroli temperatury i procesu w porównaniu z tradycyjnymi tworzywami sztucznymi, ponieważ zakres temperatur, w których materiały bio-pochodne topią się i skutecznie uszczelniają, zanim ulegną degradacji, jest znacznie węższy.
Podczas gdy tradycyjne metody zgrzewania termicznego ściskają dwie warstwy plastiku między podgrzewanymi prętami, proces musi być kontrolowany pod kątem temperatury, ciśnienia oraz czasu. Ponieważ BBP ma tak wąskie okno procesowe i wrażliwość na ciepło, prawie niemożliwe jest, aby zgrzewarki termiczne za każdym razem trafiały w to „idealne miejsce” – co jest niezbędne do powtarzalnego wytwarzania opakowań o wymaganej wytrzymałości i wydajności. Sprawia to, że producenci zastanawiają się, czy tradycyjny sprzęt do zgrzewania termicznego może zapewnić kontrolę oraz spójną, powtarzalną jakość potrzebną do produkcji opakowań z BBP.
W przeciwieństwie do tradycyjnych zgrzewarek termicznych, zgrzewarki ultradźwiękowe wykorzystują wibracje o wysokiej częstotliwości do wytwarzania ciepła wskutek tarcia na styku warstw tworzywa sztucznego tylko podczas krótkich (poniżej 1 sekundy) cykli zgrzewania. Producenci mogą monitorować parametry procesu zgrzewania w czasie rzeczywistym, ponieważ zgrzewarki ultradźwiękowe zapewniają wiele trybów pracy, kontrolowanych cyfrowo w pętli zamkniętej. Każdy parametr zgrzewu może być precyzyjnie kontrolowany i monitorowany - energia z dokładnością do pojedynczych dżuli, a siła nawet kilku niutonów. Dokładna częstotliwość rezonowania oprzyrządowania ultradźwiękowego umożliwia regulację amplitudy w mikroskali w celu precyzyjnego dostrojenia ciepła generowanego na styku zgrzewu. Ultradźwięki pozwalają użytkownikom ustawić limity jakościowe i skonfigurować alarmy, aby automatycznie identyfikować cykle zgrzewania niezgodne ze specyfikacją, a także umożliwiają automatyczne odrzucanie złych części. Precyzyjna kontrola zgrzewu to tylko jedna z wielu zalet, jakie oferują zgrzewarki ultradźwiękowe w procesie przetwarzania tworzyw sztucznych pochodzenia biologicznego.